Overview
iRelease has been made obsolete. If you’re interested in the capabilities, we suggest looking at our Deck Topside
iRelease is a rugged, handheld unit that’s used as part of a Lightweight Command Unit (LCU) setup on the back deck to test, load and release our legacy range of ORT and DORT acoustic release transponders.
At a glance
- Use it to test and control legacy ORT and DORT acoustic releases
- Compatible with legacy LCU dunking systems (replaces obsolete Psion unit)
- Handheld design, battery powered, rechargeable
- Splash-proof and rugged; designed for the back deck
- Easy-to-use five-button interface
Specifications table
Feature | Type 8315 | |
---|---|---|
Case | Rugged polypropylene copolymer case with styrenic over mould shock protection | |
Keypad | Sealed 5 key navigation pad | |
Display | 320 x 240 sunlight readable LED display | |
Connections | USB | Splash-proof mini-USB Type B |
Serial | 9-way D-type (male) | |
Charging | USB to PC or USB to wall adaptor | |
Internal flash memory | 1 GB | |
Battery | Li-ion 3.7 V 1,300 mAh (typical) | |
Battery life | Normal (screen on) | >5 hours (screen automatically turns off after a selectable period) |
Idle (screen off) | >12 hours (press a key or ‘shake to wake’ to turn screen back on) | |
Off | >3 months (press a key to wake) | |
Off for shipping | >1 year (requires USB connection to wake-up) | |
Operating temperature | -10 to 55°C | |
Storage temperature | -10 to 55°C | |
Dimensions (length x width x depth) | 194 x 84 x 40 mm | |
weight | 0.8 kg |
Datasheets
Manuals and quick start guides
Combined excellence
Overview
Equinox is a true example of how Covelya Group technologies combine to provide ground-breaking products. Designed around the Solstice MAS from Wavefront Systems, it is commercialised by Sonardyne and features our state-of-the-art SPRINT INS and Mini-Ranger 2 USBL for state-of-the-art navigation and positioning.
The Sonardyne and Wavefront Systems payloads are all mounted on EIVA’s renowned ScanFish 3D, a steerable remotely operated towed vehicle (ROTV). EIVA’s NaviSuite Kuda user interface is used to plan, autopilot and display the gathered data in real-time.
Producing stunningly accurate pictures, it’s ideal for vessels of opportunity or unmanned surface vessels delivering hydrographic, archaeological, search, salvage, unexploded ordnance, and mine countermeasure missions.
At a glance
- Mission ready; designed to support search, classify and map (SCM) and hydrographic operations
- Survey more ground in a single pass; effective area coverage rate (ACR) of up to 1.6 km2/hr
- Along track resolution of 0.15°; best in class delivering maximum detection rates
- Co-located side-scan image and bathy improves your situational awareness
- Real-time motion compensation and positioning accuracies better than 1 m DRMS
- Automatically follows terrain and avoids obstacles
- Suitable for site survey and characterisation and high tempo MCM missions
Why Equinox is perfect for your operations
The ScanFish 3D is a trusted ROTV and, thanks to its inherent stability, the ideal platform to operate Solstice from. At a total weight of 220 kg in air, Equinox can be easily mobilised.
Unlike towed Synthetic Aperture Sonar (SAS) systems, Equinox offers you an affordable, lower-logistics alternative still capable of providing high area coverage rates. By combining leading navigation and positioning from Mini-Ranger 2 USBL and SPRINT INS, imaging data is geo-referenced with an accuracy that’s unrivalled for these types of applications at this price.
Planning a mission is easy. Using NaviSuite Kuda software, you can define your sailing route and run-lines by simply selecting the area you would like to cover. During the mission, NaviSuite Kuda continuously updates the vessel and ScanFish 3D position in real-time.
Equinox also provides real-time geo-rectified waterfall, mosaics and DTM maps and the user interface tools that enable an operator to mark and process objects, including automatic target recognition using AI.
That’s not all; ScanFish 3D can carry heavier payloads and there is room in the fibre cable to include additional payload sensors such as gap fillers. Equinox users can count on improved probability of detection and decreased probability of false alarms, improving the efficiency of your mine countermeasures, archaeological, search and salvage missions.
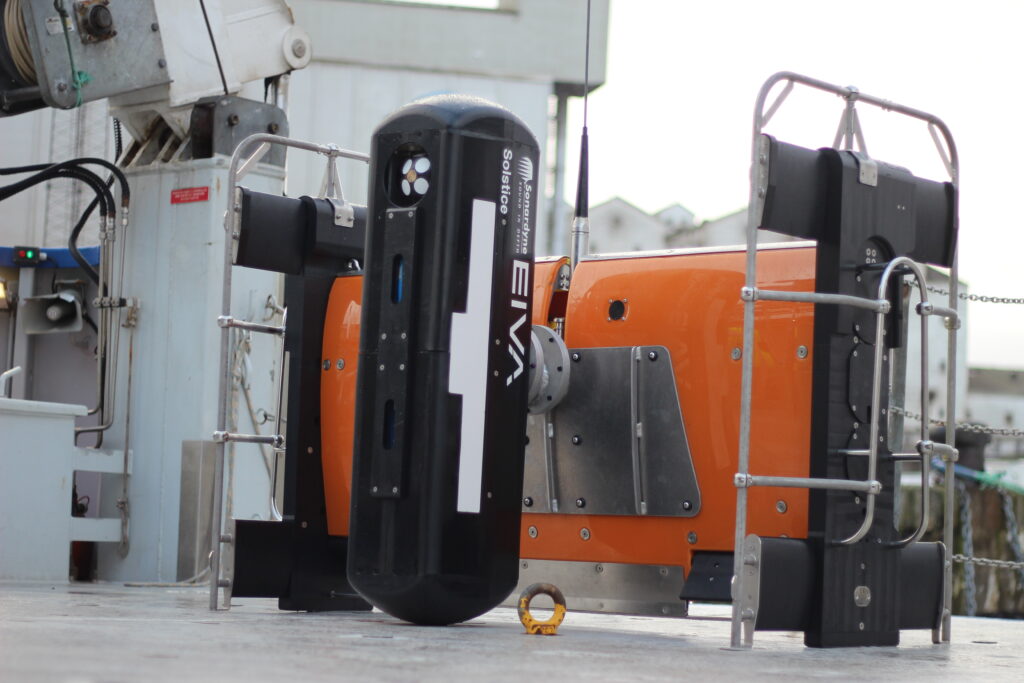
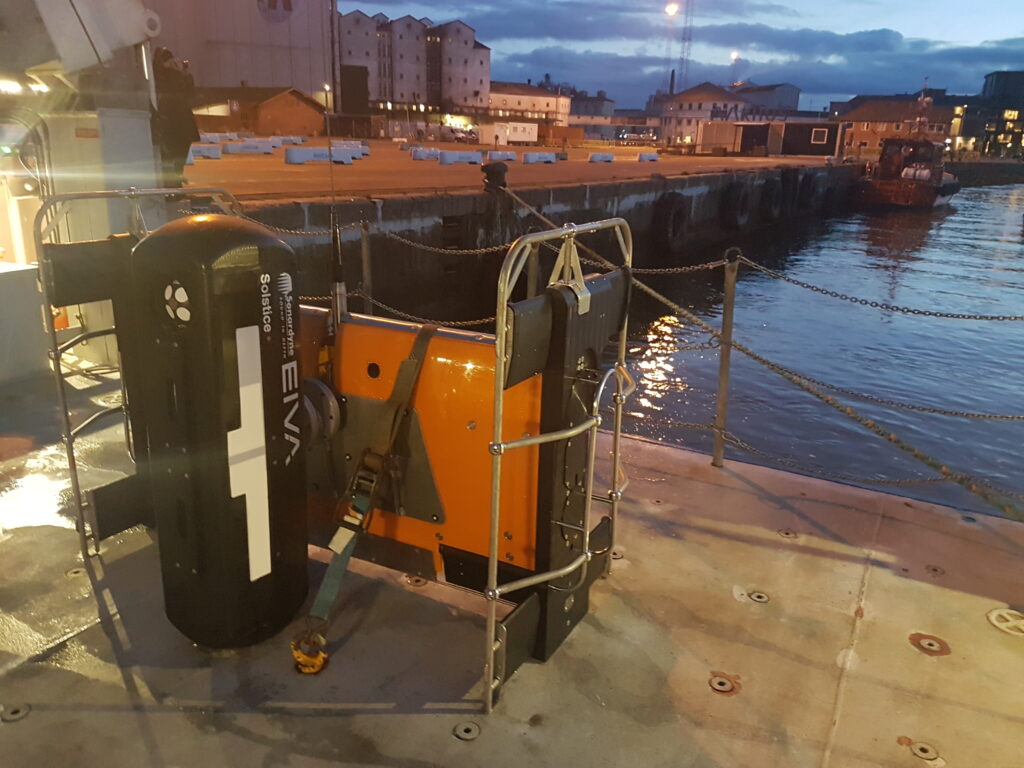
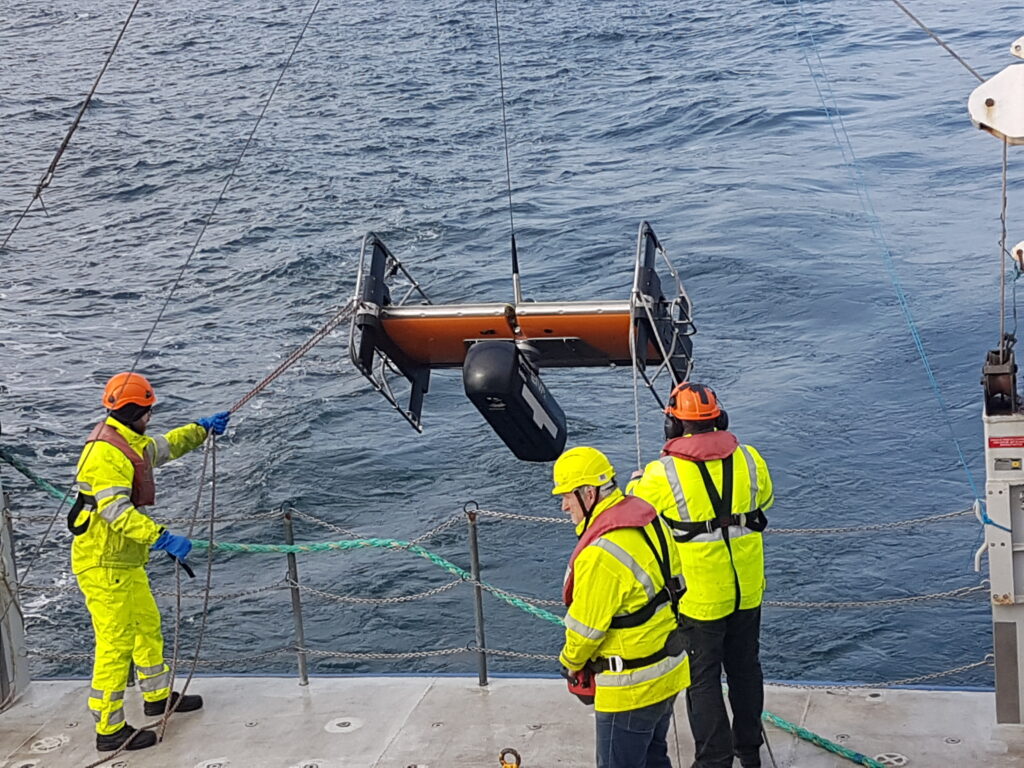
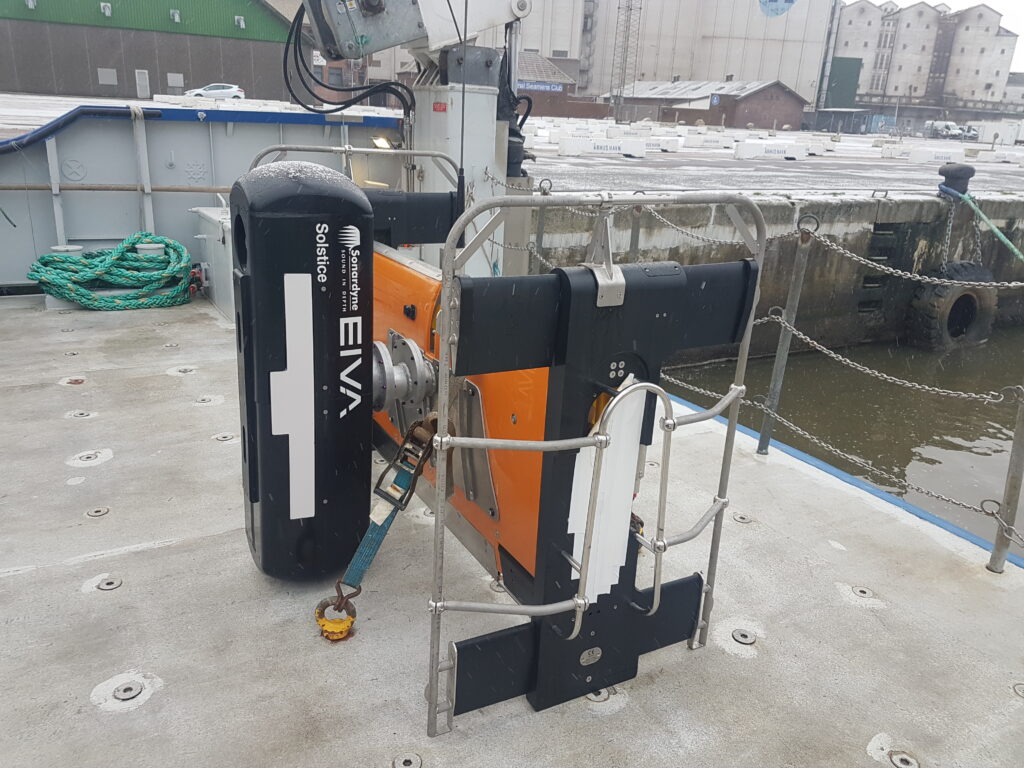
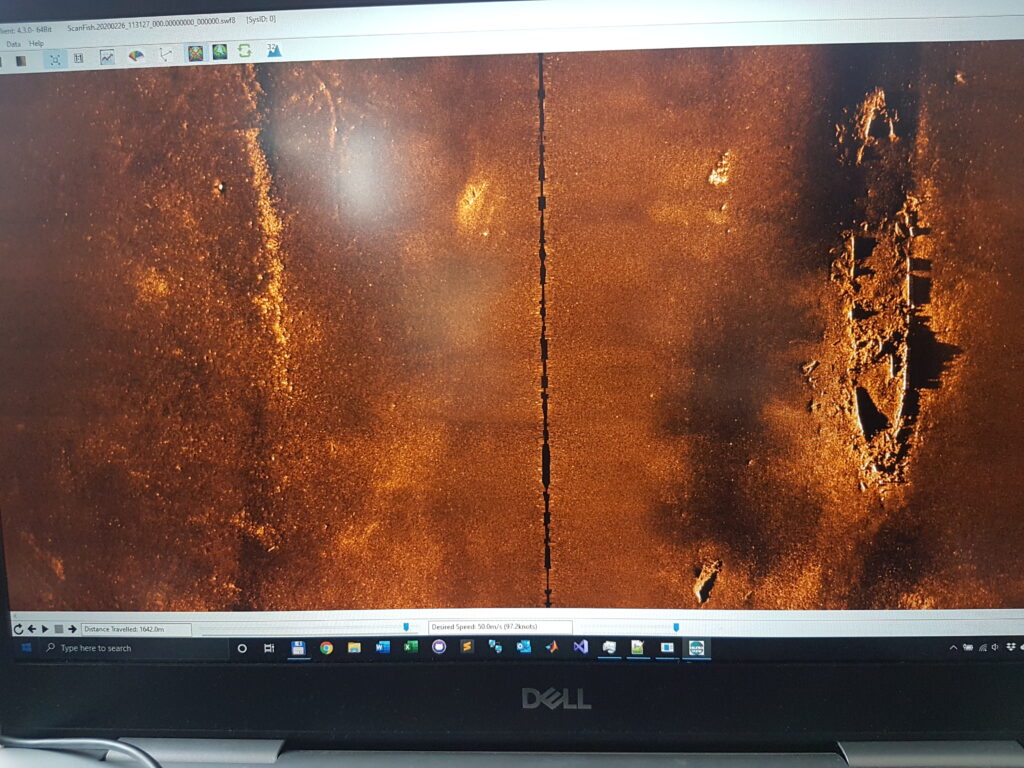
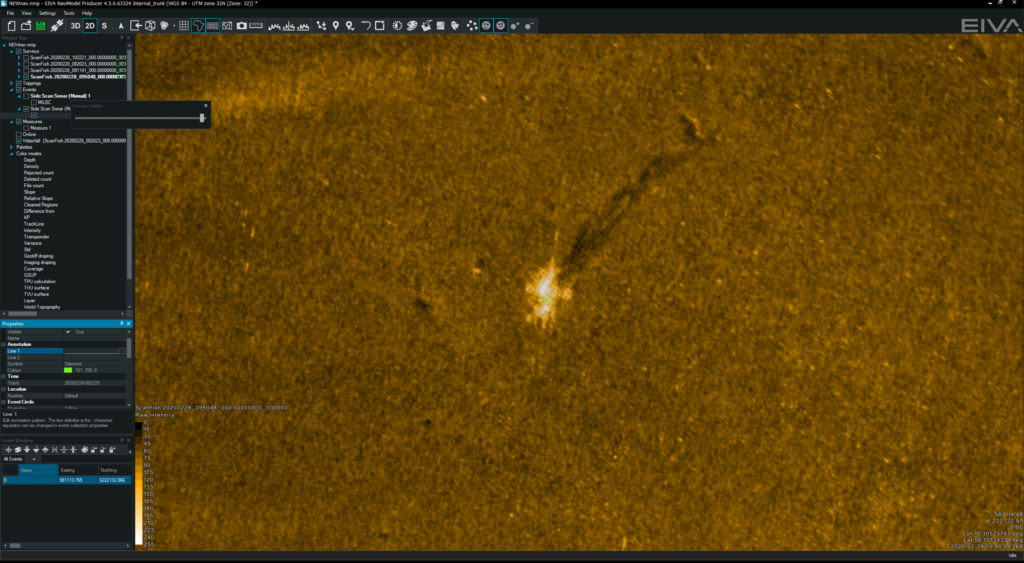
Equinox case studies
General
• All-in-one, rapidly mobilised solution for MCM, SCM and hydrography
• High stability platform with automatic terrain following
• NaviSuite Kuda software reduces planning times and improves processing times
• Everything supplied, including winch and 1Gbps cable
Performance
• Depth rated to 300 m
• Across track resolution 37.5 mm
• Along-track resolution 0.15°
• Geo-rectified waterfall display
• Image resolution 30 mm x 30 mm
• Co-located 200m swath side-scan and bathy
• Real-time CAD/CAC option
Design (SCANFISH)
• 1210 mm x 1858 mm x 1049 mm, 220 kg in air (73 kg in water)
• Survey speeds 3 to 6 knots
• Pitch and roll stabilised
• Automatic altitude following
Ownership
• What’s in the box: ScanFish 3D, NaviSuite Kuda software, cable and winch, Solstice MAS, Mini-Ranger 2 USBL, WSM 6+, SPRINT 500 INS, DVL
• Warranty: 1 year return to Sonardyne/EIVA service centre
• ITAR Controlled: No
• UK Export License: TBD
Datasheets
Capture every feature and every detail in ultra-high resolution.
Key benefits
- Mission ready; designed to support search, classify and map (SCM) and hydrographic operations
- Small and compact arrays; optimised for low-logistic AUVs and towed bodies
- Survey more ground in a single pass; 200 m-wide swath ensures high coverage rates
- Along track resolution of 0.15°; best in class delivering maximum detection rates
- Collocated side scan image and bathy improves your situational awareness
- Consumes only 18 W power: budget friendly and increases your AUV’s endurance
- Depth rated to 300 or 600 m
Solstice offers enhanced underwater detection capabilities for various missions, including mine countermeasures, archaeological, search, and salvage operations. The system provides high-performance coverage with large 200m swaths on each side, enabling efficient site characterisation without sacrificing detail. Its class-leading imagery allows you to make confident classification decisions more quickly, with the added versatility of deployment on both autonomous underwater vehicles (AUVs) and towfish platforms. By improving probability of detection and decreasing false alarms, Solstice significantly increases the overall efficiency and reliability of underwater exploration and survey missions. It is suitable for:
- Autonomous underwater vehicles (AUV)
- Site survey and characterisation
- Mine countermeasures (MCM)
- Remotely operated vehicles (ROV)
- Delivering pixel perfect imaging
Exceptional high-contrast seafloor imagery across diverse water depths
How it works
Solstice, designed by Wavefront Systems and commercialised by Sonardyne, is a world-leading side scan sonar for autonomous underwater vehicles (AUVs) and towed bodies. Its advanced technology delivers exceptional seafloor imagery through multiple aperture arrays with 32 multibeam elements, enabling superior signal-to-noise ratio performance and stunning imagery at extended ranges. The sonar’s unique back-projection beam-forming technique ensures focused imaging for every pixel, eliminating distortions caused by platform motion and guaranteeing 100% ground coverage across diverse water depths.
Designed for a wide range of marine missions including hydrographic, archaeological, search, salvage, and mine countermeasure operations, Solstice stands out through its innovative features. Its real-time array calibration dynamically recalibrates hydrophone elements multiple times per second, compensating for dynamic strains and maintaining linear element alignment. The system produces high-contrast imagery in environments ranging from 600-metre depths to very shallow littoral waters, utilising a specialised array technology that provides wide swath coverage with exceptional shadow contrast.
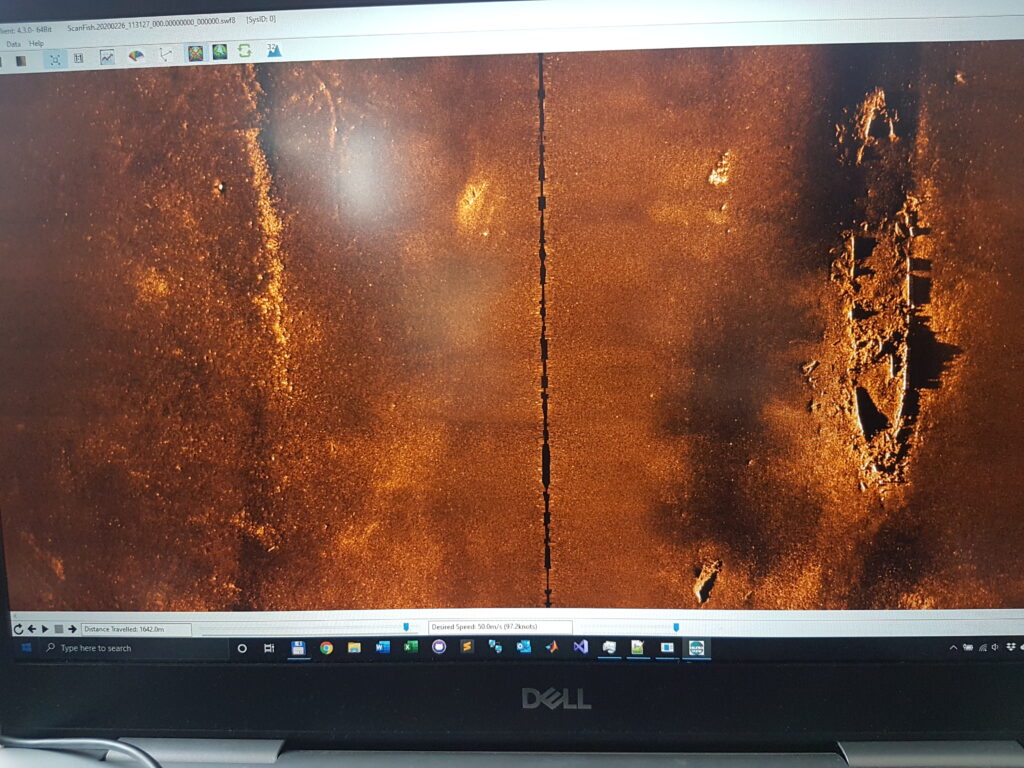
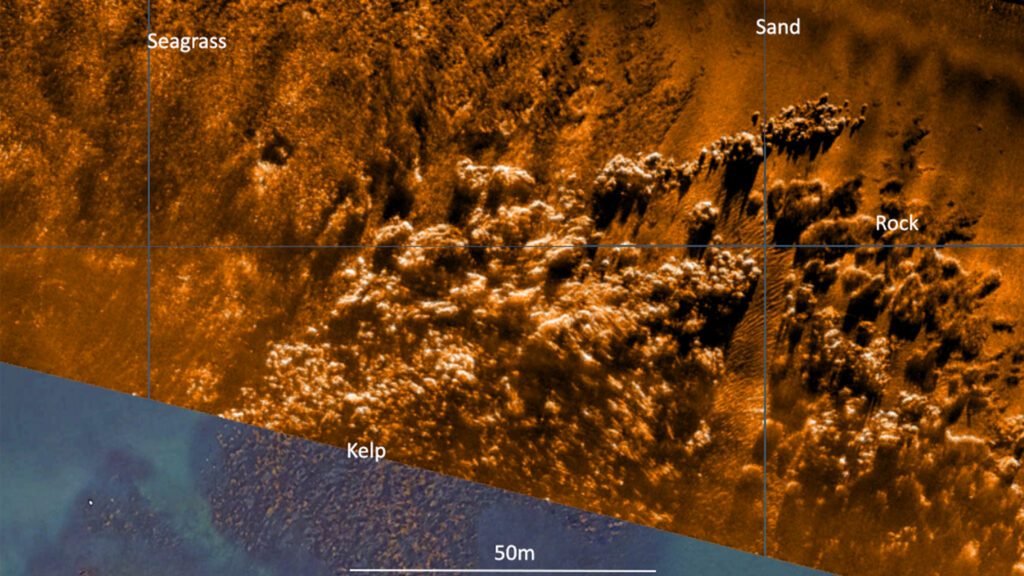
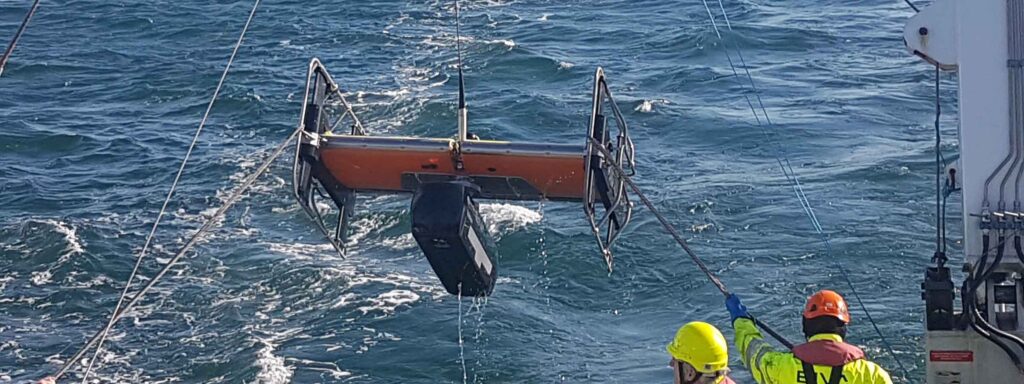
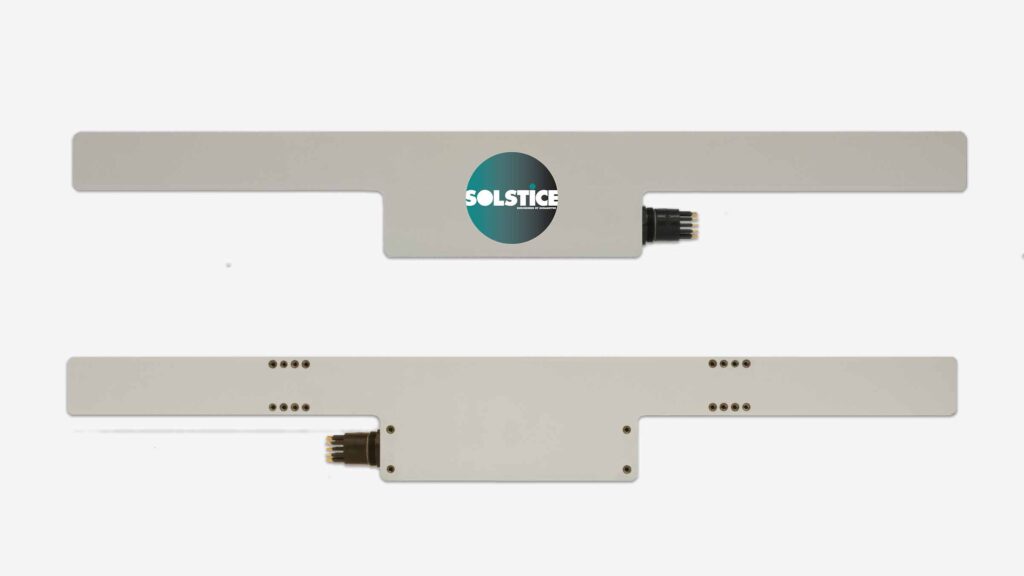
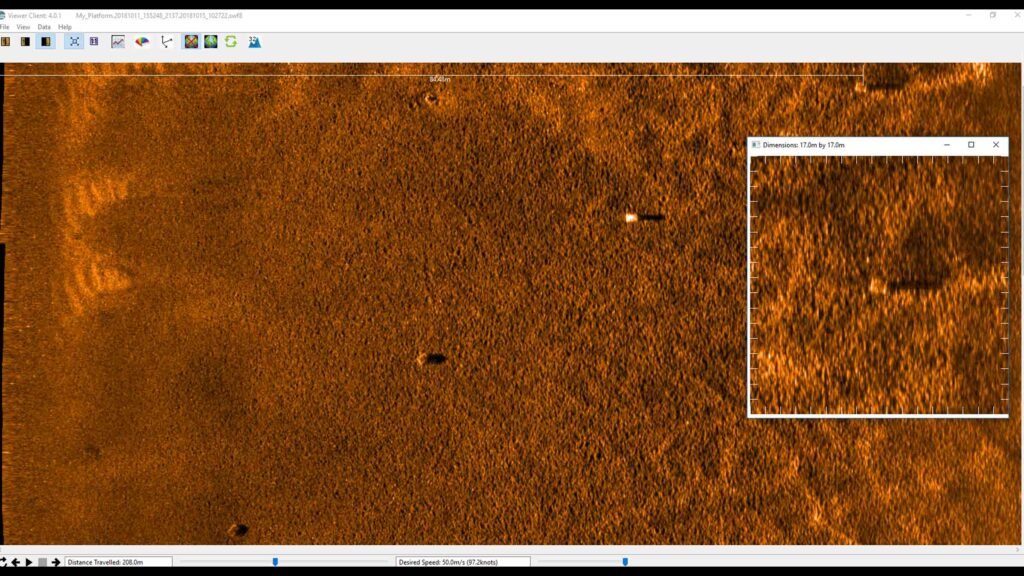
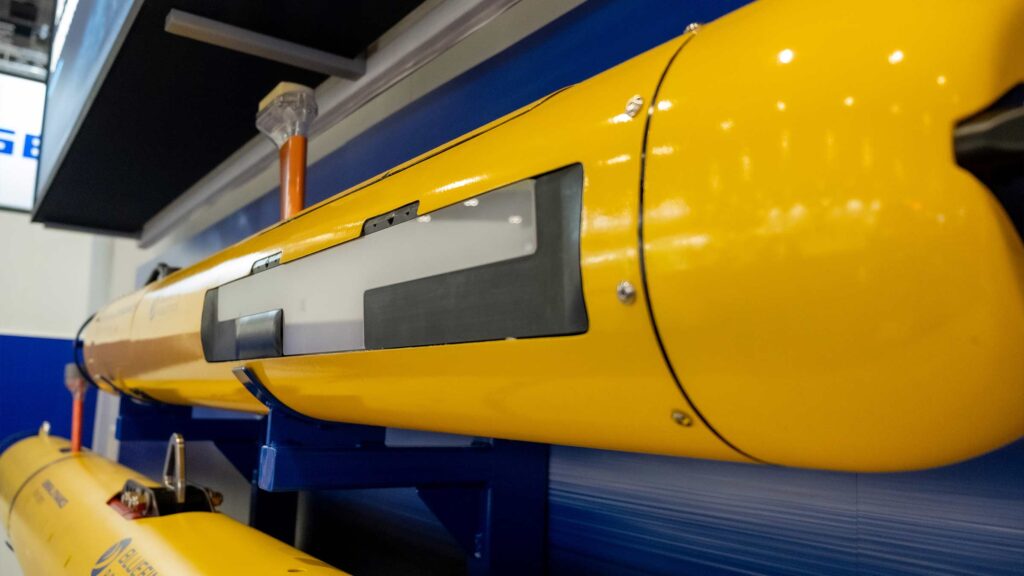
Solstice case studies
Using a hammer to crack a nut? Try using a USV instead
USVs are no longer new. They’ve been used in defence for some time now, for a range of tasks from surveillance to mine counter measures. USVs are being used to survey coastal and offshore waters in hydrographic surveys, for ocean science and in oil and gas
The challenge
Crewed vessels used in offshore construction projects are costly and can even hinder progress. But it doesn’t have to be that way. Other sectors that operate in the marine space are now finding new, smaller, smarter, cleaner tools. They’ve been using uncrewed surface vessels (USVs), so the big, crewed vessels can stick to the jobs they’re good at.
So why are we not using them heavily in offshore construction?
One reason may be because offshore construction was in fact an early adopter. But, at the time, there were only a handful of commercial USV operators whose vehicles were just too big for what was needed, making them unwieldy to deploy from an offshore vessel, defeating the point of the exercise.
Another may be the worry of the complexity involved in offshore construction. Creating complex structures on shore is one thing. Creating them under metres of salt water is entirely another.
Then there is the issue of communication and control over the construction process. Making sure each step is taken exactly as planned is fundamental to the overall success of a construction project.
The solution
USV technology has come a long way since their inception. They’ve been used in defence for some time now, for a range of tasks from surveillance to mine countermeasures. USVs are being used to survey coastal and offshore waters in hydrographic surveys, for ocean science and in oil and gas. They’re being used to go out and gather data, either as a platform for oceanographic instruments or by carrying acoustic communications systems to harvest data from sensors deployed at the seabed. You could think of them being like a remote-controlled Dunker.
USVs are now part of the toolbox across a number of sectors and the levels of sophistication and capability are increasing. Worries about lack of control, the complexity of operations or large clunky kit that isn’t up to the delicate tasks required in offshore construction are today unfounded.
In offshore renewables and oil and gas USVs are being used as part of site and seismic surveys, and then through field life, for inspection operations. They’re also being used for maintenance and repair, by acting as deployment platforms for autonomous underwater vehicles (AUVs), remotely operated vehicles (ROVs) and even aerial drones (UAVs).
The results
Today there’s a wide choice of USVs to choose from. From one-man portable USVs to full sized vessels, and on to fully electric coastal systems and hybrid long-range ocean-going vehicles that can operate for weeks on end. The range of commercial models has also grown. You can buy them outright or purchase a data service where you just order the end result – be it data or an inspection campaign.
USVs can now play a central role in construction operations. They can streamline operations and reduce risk for manned offshore construction teams. When deployed they reduce reliance on heavier, costlier tools and free-up crewed assets to be used on elements of a project where they’ll bring more value.
Long endurance monitoring of tectonic motion
Subduction zones are tectonic plate collision boundaries where typically higher density oceanic crust is being pushed under continental crust. This is one of the most important processes in the evolution of the Earth’s morphology.
The challenge
Subduction zones comprise extremely large thrust faults, known as megathrusts, and are the source of the world’s most dangerous volcanoes and earthquakes. In between larger earthquakes, megathrusts comprise complex heterogeneous distributions of locking and therefore strain accumulation.
On land, GPS and laser observations enable precise geodetic measurements. Until recently, the inability to undertake cost-effective complementary observations subsea in the outermost subduction zone offshore, has been a critical flaw. This is where much of the elastic strain build-up and release occurs. Improving scientific understanding of the seafloor movement in these regions is an important basis for future seismic hazard assessment.
The solution
In response to this challenge, Sonardyne has worked with a number of research institutes, including GEOMAR, to supply networks of Autonomous Monitoring Transponders (AMTs ) – seabed instruments that are capable of taking hundreds of thousands of stable, highly precise geodetic observations, safely log the data and on command, wirelessly transmit it up to the surface.
Originally developed for the offshore industry to precisely measure vertical and horizontal seabed displacements caused by reservoir depletion, AMT is a long-life (up to five years depending configuration), deep-rated acoustic instrument fitted with high resolution pressure, sound velocity and temperature sensors. All of this is built around our 6G hardware platform and Wideband 2 digital signal technology.
AMTs run a fully automated logging regime gathering acoustic travel time (range) between neighbouring units, pressure, sound velocity, temperature and tilt data at intervals defined by the user. A passing AUV, vessel of opportunity, gateway buoy or unmanned surface platform can harvest data on demand and at any point, the user may amend the logging regime of any or all of the AMTs, using the bi-directional communications link.
GEOMAR have now deployed three AMT seabed arrays in Chilean seas. The largest array is the Geodetic Earthquake Observatory on the SEAfloor (GeoSEA) project, offshore northern Chile on the Nazca-South American plate boundary.
The last rupture resulting in a major earthquake at the array location was in 1877. This was identified as a seismic gap prior to the 2014 Iquique/ Pisagua 8.1 magnitude earthquake.
Nevertheless, the southern portion of the segment remains unbroken by recent earthquake activity and so, with the two plates converging at a rate of around 65 millimetres per year, new tension is being continuously built up. ‘Therefore the region is a focus site for seismologists to understand strain build-up prior to an earthquake,” says Professor Kopp
The GeoSEA array consists of 23 AMTs deployed from the German Research Vessel Sonne in late 2015 and comprises three sub-arrays that monitor different sections of the megathrust. The tectonic nature of the seabed gives rise to a variety of complex topographies.
Sonardyne’s in-house Survey Support Group worked closely with scientists from GEOMAR to plan the subarray layouts. Positioning of the AMTs were based on multibeam data collected during the preceding research leg. Precise placement in the order of a few tens of metres was required and in one case, an AMT had to be sited on a ledge on the side of a ridge that was only 50 metres wide and 150 metres long.
The first area is located on the middle continental slope between the main trench and the Chile coast and consists of eight transponders laid in pairs on a stairway-like feature of four topographic ridges at a depth of around 2,800 metres. The ridges, which are surface expressions of faults at depth, are approximately 100 metres high with around an 800 metre flat area between.
On the opposite (seaward) side of the trench from Chile, a further five AMTs were deployed in depths approaching 4,100 metres to monitor extension across plate bending related normal faults. Here, faulting of the Nazca Plate is caused by stretching of its surface as it is pushed downwards under the South American plate, and thus the fault lines are relatively new and active. The AMTs were laid at the intersection of multiple fault lines separating three or four blocks, with two being placed on the same block to provide a sound speed reference baseline.
The deepest area, located between 5,100 and 5,400 metres deep, is on the lower continental slope and comprises a circular pattern of eight AMTs surrounding two central instruments. This pattern provides a variety of short and long baselines to measure diffuse strain build-up in a highly faulted area made up of separate geological blocks, which are under high compression.
To cope with these extreme conditions, the AMTs used for the GeoSEA project are 6,000 metre-rated Lower Medium Frequency (LMF 14-19 kHz) omnidirectional units. Sampling at rates between one and a half and three hours, the GeoSEA AMTs are planned for an initial three and a half year deployment. However, the four metre high seabed frame in which each unit sits enables it to be easily removed by ROV, returned to the surface to allow its battery to be exchanged then placed back in the frame in the same position – giving scientists the option of extending the survey if required.
The results
Since initial deployment, data from the array has been recovered by a US research ship using a Sonardyne HPT 7000 dunking modem deployed over the side, as well as GEOMAR’s GeoSURF Wave Glider, equipped with a 6G acoustic communication module fitted in its hull.
“Overall, our experience with Sonardynes instruments is superb and our results have been beyond our expectations. It has been a pleasure for us to work with infrastructure that we can fully rely on.” Professor Kopp from GEOMAR commented.
The success of the AMT’s performance in the Nazca-South American plate boundary arrays has resulted in two smaller arrays in the Sea of Marmara off Turkey and on the submerged flanks of Mount Etna. Although the results of these surveys were yet to be published at the time of writing, scientists were excited by the new opportunities Sonardyne’s technology offers.
GEOMAR’s Doctor Dietrich Lange summarises that, “With this approach, we are taking a new path in earthquake research since previously, measurements of a few millimetres, were hardly possible.”
Rewriting the subsea survey rules
The underwater survey and construction sector is necessarily risk-averse. The potential negative impact from downtime, rectification events or environmental damage caused by changes to procedures and methods can be burdensome. The result is a preference for tried and true methods, techniques and equipment.
The challenge
In recent years, different combinations of subsea positioning technologies have been used in support of survey and construction projects. Whilst delivering an incremental improvement, they have also resulted in increased complexity in integration and operation. Separate inertial navigation systems (INS) and Long BaseLine (LBL) solutions require integration via online navigation software. Along with this, there is the added complication of the physical mounting, calibration and interfacing of INS and Doppler velocity logs (DVL) on remotely operated vehicles (ROVs).
The increased complexity adds cost in training and support, as well as increasing risk through having to control many separate parts from different vendors.
There is clearly a need to be smarter and more efficient. Reducing vessel days increases safety and lessens our environmental footprint. There is no need to lose the accuracy or reliability of subsea positioning or increase the complexity of operations either. If both the number of Compatts needed for an LBL pipeline installation array and calibration routine could be reduced, days – not just hours – of vessel time would also be lowered as would the entire complexity of such projects.
The solution
i-Tech 7 adopted our Fusion 2 all-in-one software platform for their INS and LBL operations.
This allowed them to take advantage of the Fusion 2’s real-time simultaneous localisation and mapping (SLAM) capability. Choosing to operate a sparse LBL can deliver a reduction of Compatts. However, if the sparse array cannot be calibrated using traditional LBL baseline calibration, the benefit may be lost. Extra time for performing additional ‘box-ins’ or collecting data to perform post processed SLAM positioning of the Compatts becomes necessary.
This isn’t the case with real-time SLAM. The number of Compatt transponders used to create the ‘sparse’ LBL array is reduced and the calibration of those Compatts is managed by flying the ROV through the array and acquiring the necessary observables to SLAM the array. With careful planning, this real-time SLAM process can be done during other ROV survey operations, such as pre-lay surveys. This removes the entire baseline calibration work flow from the project schedule.
Co-locating our SPRINT INS with a separate DVL onto i-Tech 7’s ROVs was the first step in reducing the complexity of these operations. Using SPRINT enabled the optimisation of sparse LBL operations, reducing the number of Compatts required for an LBL array by 50-66%, with the post-processing SLAM calibrations being managed by us.
The SLAM calibration technique was run alongside arrays with full LBL sections and sparse LBL arrays which were SLAM calibrated. When results were compared they showed centimetric agreement, proving real-time SLAM gives near traditional LBL levels of precision and accuracy.
All the experience and knowledge gained since i-Tech 7’s first use of our SPRINT INS in 2012 has enabled us to build SLAM calibration routines directly into Fusion 2. That step has taken the simplification to a new level. Real-time SLAM operations in i-Tech 7’s 2019 project have far more efficient trajectories than previous operations.
The results
Between August and November 2019, a minimum of 11 vessel days were saved across five separate i-Tech 7 deep water (1,000-1,500 m) projects in the US Gulf of Mexico. Thanks to Fusion 2’s real-time SLAM capability, operators were able to access first oil faster.
Having already reduced the number of Compatts needed for an array – by reducing how much time is spent deploying them and calibrating them – the time allocated on project schedules for the lengthy box-in routines required in a traditional array can also be reduced, if not completely negated.
In fact, following a pre-lay survey, an offshore manager asked one of i-Tech 7’s offshore surveyors how long the array calibration would take before pipelay operations could start. The answer? It had already been done.
i-Tech 7 and Subsea 7 have proved the simplification of pipeline installation projects can be smarter, more efficient, quicker and safer. What’s more, they help lessen the overall environmental footprint of major subsea installation projects. This can all be done without losing positioning accuracy or reliability.
Shallow water site investigation for offshore wind
From the topside to the underwater instruments, our goal is to make offshore operations easier and less time-consuming, but also highly accurate. As PDE Offshore discovered, with Mini-Ranger 2, our 6G hardware and our Wideband 2 digital acoustic technology onboard, safe and efficient shallow-water site investigation operations, from tracking towfish to positioning seabed geotechnical equipment, are assured.
The challenge
In a short period of time, Taiwan has quickly become a leader in the global build-out of offshore wind. Starting from scratch in 2018, the country has been quick to ramp up its offshore wind capability. Taiwanese company PDE Offshore, based in New Taipei City, was quick to get involved in this new industry and came to us for a USBL system to underpin its offshore wind geotechnical site investigation service offering.
Specifically, it was looking for a system to support geotechnical site and soil investigation works for a new offshore wind farm in the shallow water Taiwan Strait. This involves deploying geotechnical drilling equipment on the seabed at each planned turbine site in just 20 – 60 m water depth. The frame holding the equipment has to be positioned accurately to ensure it’s aligned with the drill string deployed from PDE Offshore’s geotechnical survey vessel.
The solution
PDE Offshore chose a combination of our Mini-Ranger 2 USBL system and our Wideband Sub-Mini 6+ (WSM 6+) transponder/responders to track and position their drilling frame on the seabed. Mini-Ranger 2 is built around the same market-leading 6G hardware and Wideband 2 digital acoustic technology you’ll find in our entire family of USBL systems – even the software is the same.
Critically, it’s designed to easily handle just the kind of shallow waters PDE Offshore had to work in on the project in the Taiwan Strait. At the heart of Mini-Ranger 2 is our HPT 3000, a highly capable surface-deployed USBL transceiver that’s optimised for high performance in shallow water, as well as high elevation and long lay back operating scenarios and data telemetry.
It was a simple choice for PDE Offshore, not least as their onboard surveyor was already familiar with Mini-Ranger 2. What’s more, it’s also a great option for smaller vessels and even unmanned surface vessels (USVs).
A wide range of Sonardyne 6G transponders can be used with Mini-Ranger 2, allowing you to select the most appropriate took for each task. For its operations in the Taiwan Strait, PDE Offshore chose our Wideband Sub-Mini 6+ (WSM 6+) transponder/responders. Designed for positioning ROVs, towfish and other mobile targets in water depths up to 4,000 m, WSM 6+ incorporates our Wideband signal technology, so it offers superior ranging accuracy and fast USBL position updates as well as full two-way Wideband support – interrogation and reply signals.
Targeting
0
GW
by 2025
0
m/s
average wind speed
Average water depth
0
m
for each turbine
The results
PDE Offshore spent summer 2020 performing site investigation works from the MV Geo Energy in the Taiwan Strait. Our WSM 6+s were mounted on the seabed frame and tracked using the Mini-Ranger 2’s HPT 3000, which was deployed on an over-the-side deployment pole from the MV Geo Energy.
Huang Hsin-chih, president of PDE Offshore, says, “Where we work in the Taiwan Strait, water depth is from 20 to 60 meters; in the future, there might be a chance to work in offshore wind farm with water depth from 50 to 200 meters, so whilst we do need a very precise USBL, we don’t need one that’s full ocean depth capable. Through renting, we became familiar with Mini-Ranger 2 and the benefits it brought to our busy geotechnical operations. So it was a simple choice to decide to go ahead and purchase one of our own and it has proven fully capable for our needs on this and future offshore wind projects.”
Optimising shallow water positioning for combined magnetometer and hydrographic surveys
Seabed surveys are now on the critical path towards meeting global renewable energy generation targets. That’s why Ocean Floor Geophysics are working on ways to improve how pipelines and cables are detected and monitored. Our positioning and navigation technologies were used to support a demonstration of their Hypermag gradiometer with Covelya Group company EIVA.
The Challenge
Detecting cables or pipelines on the seabed and checking or monitoring cable depth are essential requirements in the development and management of most offshore energy projects. With a global target of 80 GW of offshore wind to be built annually by 2030, these tasks are also now on the critical path.
Magnetometers or gradiometers (comprising an in-line array of magnetometers) are a key tool for these operations. Accurately knowing the position of these instruments in the water throughout a survey ensures that target detection resolution is as high as possible. So, Canada-based Ocean Floor Geophysics’ (OFG) has developed the Hypermag gradiometer.
Rather than towing a magnetometer or gradiometer from a vessel or ROV, OFG’s Hypermag has been designed with multiple vector magnetometers installed in a scalable array that can be integrated directly onto a remotely operated towed vehicle (ROTV), such as EIVA’s ScanFish. This removes any positional uncertainties seen when using a layback offset when towing a magnetic sensor. The multi-vector gradiometer could then acquire compensated magnetic data in real-time
OFG possesses advanced multiphysics capability, particularly in fusing acoustic data with magnetic and electromagnetic field data, in this case magnetic field interpretation across multiple three-vector sensors. The team, therefore, required optimum shallow water positioning of the ROTV to demonstrate the gradiometer at its highest capability. “A high-quality, accurate navigation solution is a key component in achieving the full potential from our next generation of magnetic vector gradiometer sensors,” says OFG CEO Matthew Kowalczyk. “In shallow water environments, such as near-shore windfarms and UXO survey sites, it can also be one of the most difficult datasets to produce.”
The solution
Covelya Group companies EIVA and Sonardyne supported a demonstration of the Hypermag in the vicinity of a wind farm in the North Sea. EIVA provided ScanFish support, including integration of the Hypermag configuration, a Norbit multibeam and a NaviPac software solution. Sonardyne provided a SPRINT-Nav Mini INS system alongside Ranger 2 equipped with a Gyro USBL transceiver, providing OFG with comprehensive position and behaviour accuracy of the ScanFish platform and it’s offset Hypermag sensors.
The SPRINT-Nav Mini Navigator is our smallest form factor hybrid navigation instrument, combining an INS, AHRS, Doppler velocity log (DVL) and pressure sensor.
By using this integrated INS system, updated by the Ranger 2 Gyro USBL, positioning errors or any erroneous USBL pings or dropouts could be mitigated. The INS can, in real-time, reject outliers in the data and output AHRS data, velocity, depth and altitude, as well as outputting real-world positional data in real-time, mitigating the need for post-processing. In addition, the SPRINT-Nav Mini could support multibeam data acquisition when a combined multibeam and magnetic gradiometer solution is used.
To put the approach to the test, a vessel of opportunity, the 22 m Marshall Art survey vessel, was mobilised. We used our Ranger 2 Gyro USBL system, which comes pre-calibrated, for easy mobilisation, with a Norbit iWBMSh multibeam echosounder (MBES) on Marshall Art providing RTK GNSS into the Gyro USBL.
On the ScanFish there were two OFG Hypermag panels, comprising a total of eight magnetometers, our SPRINT-Nav Mini Navigator, an omnidirectional Wideband Sub Mini 6+ transponder and a Norbit multibeam. An OceanEnviro fibreoptic winch system was installed on the vessel to tow the ScanFish. Orientation and position data was provided by the SPRINT-Nav Mini.
The results
“This was a great collaboration,” says Matthew Kowalczyk. “The combination of Sonardyne’s Ranger 2 Gyro USBL system and SPRINT-Nav Mini allowed us to quickly produce a navigation solution for the Hypermag system that exceeded our expectations.
“A high-quality navigation solution is necessary for achieving the full potential from our next generation of marine magnetic vector gradiometer sensors. Sonardyne’s support contributed to the trial’s overwhelming success.”
Another benefit of using SPRINT-Nav Mini on the ScanFish is that it can support its 3D steer algorithm, which can make surveying more efficient, reducing overall survey costs.
Pipelines and cables are often surveyed using a zig-zag pattern to decrease survey time. However, the most efficient way to survey a pipe would be to run parallel to the pipe, which EIVA 3D Steering allows with a suitable navigation solution because the position of the data measurement can be known with higher certainty.
Greater efficiency, lower overheads, with underwater autonomy in deepwater seismic
Shell Brasil, in partnership with Petrobras, Sonardyne and Brazilian research institute SENAI CIMATEC are working together to bring a step-change to 4D seismic data gathering in Brazil’s deepwater pre-salt region.
Discover how we’re collaborating to develop innovative autonomous technology that will make monitoring these challenging deepwater fields more efficient, with fewer people and lower environmental footprint.
Scroll down to read this case study in Portuguese.
The challenge
Seismic data is an essential part of offshore field development activity, especially to support proactive reservoir management and production optimisation. Techniques for gathering this data have evolved dramatically over the decades; from the use of marine streamers for large exploration seismic campaigns to the now routine use of remote operated vehicles (ROV) to deploy ocean bottom nodes (OBN) for high-resolution imaging of pre-salt reservoirs.
Yet, gathering seismic data for pre-salt reservoir imaging remains intensive work. It involves large, costly and carbon-emitting crewed vessels for deployment and recovery of, typically, thousands of nodes. As an example, for a 10-month campaign over one of Brazil’s giant pre-salt fields, a node handling vessel could emit close to 10,000 tons of CO₂. Costly and complex operations can mean a reduction in frequency of surveys, including of those done to gather what’s called time lapse or 4D seismic data, which is required to monitor the pre-salt reservoirs.
Shell and Petrobras came to us believing that there could be a lower-cost, more sustainable, way of acquiring 4D seismic data, as well as other parameters such as seafloor subsidence, to help better monitor reservoirs. They also saw this could be done with a lower environmental footprint and while keeping more people safe.
The solution
Together, Shell Brasil, Petrobras, and Sonardyne joined forces with SENAI CIMATEC to develop an advanced seismic data acquisition system under a Brazilian National Agency of Petroleum, Natural Gas and Biofuels (ANP) promoted research and development project.
At its core is an On-Demand Ocean Bottom Node, or OD OBN. This semi-permanent seabed system is used for the acquisition of high resolution seismic and seafloor subsidence data.
Like conventional seabed nodes (OBN), each OD OBN contains three geophones and one hydrophone, a data recording system, batteries and a highly accurate clock. The sensors detect pressure waves emitted by an airgun source, usually towed by a ship, as they are reflected upwards towards the seabed from the underlying layers of rock surrounding the reservoir.
Unlike conventional nodes, these OD OBNs remain on the seabed, down to 3,000 m, gathering seismic data for up to five years. This significantly reduces the cost of repeated ocean bottom seismic campaigns, as the node handling vessel is removed from the operations. It also reduces the impact on the environment and marine ecosystems.
The activation of the nodes, verification of subsidence event alarms, calibration of internal clocks and harvesting of seismic data will be performed using an autonomous underwater vehicle (AUV) called Flatfish developed, in a closely interlinked ANP project, by partners Shell Brasil, Petrobras, SENAI CIMATEC and Saipem.
Flatfish will find each node using Sonardyne’s 6th generation (6G) of acoustic positioning systems. Our acoustics will also support data telemetry with the nodes, for health checks, configuration and acoustic time synchronization. The Flatfish will then hover above each node, in turn. Using an extremely high bandwidth and energy efficient laser-based variant of Sonardyne´s BlueComm optical communications device, it will wirelessly harvest many gigabytes of seismic data in just a few minutes.
This variant uses two rapidly modulated lasers to produce simultaneous bi-directional communications over more than five meters range. It is optimised for peak data transfer performance, with speeds of over 600 megabits per second demonstrated. This makes it excellent for harvesting large amounts of data from seabed nodes.
“Using OD OBN in combination with Flatfish, a 4D seismic campaign in the pre-salt may be executed in a simpler manner, with lower operational cost, lower risk of human exposure and lower environmental impact,” says Jorge Lopez, Manager of Subsurface Technology at Shell Brasil. “On top of this, the nodes also measure seafloor deformation and can continuously monitor for possible subsidence events that may occur during the production of the field.”
The results
In the first phase of the OD OBN project, eight fully functional prototype nodes were built. These comprised of two different concept types and were designed and built by SENAI CIMATEC in Salvador, Bahia together with Sonardyne Brasil.
In 2021, initial tests of seismic data recording were conducted at the Sapinhoá pre-salt field offshore Brazil and interoperability tests between the nodes and the Flatfish AUV were performed in shallow water in Trieste, Italy.
A very intensive laboratory and offshore testing and demonstration program is being conducted over the next 18 months to ensure the OD OBN system meets its operational requirements. This program will increase the maturity of the solution, with tests in pre-salt fields for recording seismic data with the OD OBN prototypes and the communication and data harvesting AUV missions.
In the next phase of the project, starting later in 2022, Shell and Petrobras will sign a new agreement to manufacture 600 nodes and deploy them for three years of reservoir monitoring in a Brazilian pre-salt field.
Maior eficiência, baixo custo de operação, para sísmica em águas profundas através de autonomia submarina
A Shell Brasil, em parceria com a Petrobras, a Sonardyne e o instituto de pesquisa brasileiro SENAI CIMATEC estão trabalhando juntos para trazer uma mudança radical na coleta de dados sísmicos 4D na região do pré-sal em águas profundas do Brasil.
Descubra como estamos colaborando para desenvolver tecnologia autônoma inovadora que tornará o monitoramento desses desafiadores campos em águas profundas mais eficiente, com menos pessoas e menor impacto ambiental.
O desafio
Os dados sísmicos são uma parte essencial da atividade de desenvolvimento de campos offshore, especialmente para apoiar o gerenciamento proativo de reservatórios e a otimização da produção. As técnicas para coletar esses dados evoluíram dramaticamente ao longo das décadas; desde o uso de streamers marinhos para grandes campanhas sísmicas de exploração até o uso rotineiro de veículos operados remotamente (ROV) para implantar nós de fundo oceânico (OBN) para imagens de alta resolução de reservatórios do pré-sal.
No entanto, a coleta de dados sísmicos para imagens de reservatórios do pré-sal continua sendo um trabalho intensivo. Envolve embarcações tripuladas grandes, caras e emissoras de carbono para implantação e recuperação de, normalmente, milhares de nós. Como exemplo, para uma campanha de 10 meses em um dos campos gigantes do pré-sal brasileiro, uma embarcação de manuseio de nós pode emitir cerca de 10.000 toneladas de CO₂. Operações caras e complexas podem reduzir a frequência de levantamentos, inclusive daqueles feitos para coletar o lapso temporal que é chamado de dados sísmicos 4D, necessários para monitorar os reservatórios do pré-sal.
A Shell e a Petrobras nos procuraram acreditando que poderia haver uma forma mais barata e sustentável de adquirir dados sísmicos 4D, além de outros parâmetros, como subsidência do fundo do mar, para ajudar a monitorar melhor os reservatórios. Eles também viram que isso poderia ser feito com um impacto ambiental menor e mantendo mais pessoas seguras.
A solução
Juntos, Shell Brasil, Petrobras e Sonardyne uniram forças com o SENAI CIMATEC para desenvolver um sistema avançado de aquisição de dados sísmicos em um projeto de pesquisa e desenvolvimento promovido pela Agência Nacional do Petróleo, Gás Natural e Biocombustíveis (ANP).
Em seu núcleo está um On-Demand Ocean Bottom Node, ou OD OBN. Este sistema semipermanente do fundo do mar é usado para a aquisição de dados sísmicos de alta resolução e subsidência do fundo do mar.
Assim como os nós convencionais do fundo do mar (OBN), cada OD OBN contém três geofones e um hidrofone, um sistema de gravação de dados, baterias e um relógio de alta precisão. Os sensores detectam ondas de pressão emitidas por uma fonte do tipo airgun, rebocada por um navio, à medida que são refletidas para cima em direção ao fundo do mar a partir das camadas subjacentes de rocha ao redor do reservatório.
Ao contrário dos nós convencionais, os OD OBNs permanecem no fundo do mar, até 3.000 m, coletando dados sísmicos por até cinco anos. Isso reduz significativamente o custo de repetidas campanhas sísmicas no fundo do oceano, uma vez que a embarcação de manuseio de nós é removida das operações. Também reduz o impacto no meio ambiente e nos ecossistemas marinhos.
A ativação dos nós, a verificação dos alarmes dos eventos de subsidência, a calibração dos relógios internos e a coleta dos dados sísmicos serão realizados por meio de um veículo submarino autônomo (AUV) denominado Flatfish, desenvolvido em um projeto ANP estreitamente interligado, pelos parceiros Shell Brasil, Petrobras, SENAI CIMATEC e Saipem.
O Flatfish encontrará cada nó usando a 6ª geração (6G) de sistemas de posicionamento acústico da Sonardyne. Nossa acústica também suportará telemetria de dados com os nós, para verificações de integridade, configuração e sincronização de tempo acústico. O Flatfish irá então pairar acima de cada nó, por sua vez. Usando uma largura de banda extremamente alta e uma variante baseada em laser com eficiência energética do dispositivo de comunicação óptica BlueComm da Sonardyne, ele coletará sem fio muitos gigabytes de dados sísmicos em apenas alguns minutos.
Esta variante usa dois lasers modulados rapidamente para produzir comunicações bidirecionais simultâneas em um alcance de mais de cinco metros. Ele é otimizado para desempenho de transferência de dados de pico, com velocidades demonstradas de mais de 600 megabits por segundo. Isso o torna excelente para coletar grandes quantidades de dados de nós do fundo do mar.
“Usando OD OBN em combinação com o Flatfish, uma campanha sísmica 4D no pré-sal pode ser executada de forma mais simples, com menor custo operacional, menor risco de exposição humana e menor impacto ambiental”, afirma Jorge Lopez, Gerente de Tecnologia de Subsuperfície da Shell Brasil. “Além disso, os nós também medem a deformação do fundo do mar e podem monitorar continuamente possíveis eventos de subsidência que podem ocorrer durante a produção do campo”.
Os resultados
Na primeira fase do projeto OD OBN, doze nós protótipos totalmente funcionais foram construídos. Estes são compostos por dois tipos de conceito diferentes e foram projetados e construídos pelo SENAI CIMATEC em Salvador, Bahia em conjunto com a Sonardyne Brasil.
Em 2021, os testes iniciais de registro de dados sísmicos foram realizados no campo do pré-sal de Sapinhoá no litoral brasileiro e os testes de interoperabilidade entre os nós e o Flatfish AUV foram realizados em águas rasas em Trieste, Itália.
Um intenso trabalho em laboratório e um programa de demonstração e testes offshore estará sendo realizado nos próximos 18 meses para garantir que o sistema OD OBN atenda aos seus requisitos operacionais. Este programa aumentará a maturidade da solução, com testes em campos do pré-sal para registro de dados sísmicos com os protótipos OD OBN e as missões AUV de comunicação e coleta de dados.
Na próxima fase do projeto, a partir do final de 2022, a Shell e a Petrobras assinarão um novo acordo para fabricar 600 nós e implantá-los para três anos de monitoramento de reservatórios num campo do pré-sal brasileiro.
Facing the challenge of speeding up consent in offshore renewable energy
The drive for cleaner, greener energy set against financial constraints in a challenging world market could mean testing times ahead for offshore renewable energy (ORE).
In order to meet pressing timescales, cost saving criteria and governmental targets for energy production, the industry needs shorter consenting periods for offshore wind projects but also better characterisation data. Better data would suggest the need for a longer, more costly, consenting period. So how can this challenge be met?
At Sonardyne, we believe our Origin® acoustic Doppler current profilers (ADCPs) may offer at least part of the solution. ADCPs use acoustics to measure the water column to determine currents and many can also measure wave motion and turbulence. They can provide metocean data for decision making on where to place floating turbines to ensure moorings are not stressed, determining where scour may occur that will damage cables or structures, array cable selection, route planning and cable’s depth of burial predictions etc.
Obtaining high quality, accurate, current and wave data has always been a challenge in the marine environment. Which is far from ideal when there’s a need for more timely, precise data. Meanwhile, traditional ADCP technology does not have resolution high enough to distinguish fine-scale turbulence. The correct measurement of turbulence is a key factor in ensuring that any planning at the consenting stage is based on accurate data.
With accurate data at the consenting stage, developers can reduce options and decide on the exact foundation solution, maximum turbine size etc. They can then plan with certainty and model simple environmental impact assessments for presentation to the consenting authorities.
Enter Origin…
Our Origin 600 and 65 ADCPs signify a sea change in ocean floor ADCP technology and are the most advanced ADCP’s presently on the market.
Alongside industry standard PD0, new and exclusive A-gram and B-gram proprietary data formats offer up to ten times greater spatial resolution and provide superior quality data for more informed decision making.
The inbuilt acoustic modem provides the ability to; check operating status, test data quality and change schedules mid-mission. It also provides remote access to the customisable Edge data processing applications on Origin. This means that while the device is deployed, it can be programmed to output concise, relevant information, rather than bulky raw data that would normally be processed once the device is recovered from the water. All without the cost and risk associated with interfacing an external modem or running a cabled ADCP operation.
Realising the potential
Taking this a step further and combining Origin’s data and communication capabilities with autonomous data collection via an uncrewed surface vehicle (USV) or surface buoy potentially offers many advantages.
Operators can make informed decisions faster as more frequent, concise data samples can be collected throughout the deployment, rather than waiting for the ADCP’s retrieval. Data can be collected at intervals via a USV passing overhead or transmitted to Cloud storage via a LiDAR buoy.
Reduction of carbon emissions during missions can also be achieved. USV data harvesting and an ADCP battery life of over three months are just two in which the need for a carbon-heavy crewed vessel would be reduced. The associated costs and HSE exposure hours would be reduced too.
Origin’s ability to provide high fidelity data, often in near real-time – depending on the harvesting method – offers the potential to meet the data requirements within a shorter timeframe.
Concept testing
A proof-of-concept trial was conducted in Plymouth Sound in April 2023, with the aim of establishing the range and quality of data transmittable from the seabed via Origin and a USV to the shore.
An Origin 600 was mounted on a tripod frame and integrated with a third-party turbidity sensor before being deployed at a depth of approximately 8m in Cawsand Bay. For the purposes of the test, Origin was configured, via the Edge processing app, to average out its readings alongside those from the turbidity sensor for the previous 20 minutes and to send the results acoustically every five minutes. In a real-world scenario, this update rate would usually be configured less frequently.
Our USV ‘Decibel’ was fitted with; an Avtrak6 Nano to receive the data, a deck topside box running the Origin topside software and a control unit payload supplied by the Metocean, Science and Technology team at RPS, to push the data to a Cloud storage via Iridium. For this trial, the team at RPS took LiDAR technology and integrated it into a buoy with power, data storage and satellite communication capabilities. Applying deep expertise of offshore measurement, the design and development process was focussed on creating a reliable design to maximise data accuracy and return, while making the process of information gathering easier and more cost-effective.
Decibel then hovered on the surface above Origin and performed a slow drift off test to establish an understanding of communication coverage/range limits. A lateral excursion of 87 metres was achieved, which equates to a very small elevation angle of almost five degrees – important for shallow water buoys in areas with strong tidal patterns. Once the test was complete, data that had been stored by Origin was compared to the data it had transmitted to the Cloud, via the acoustic modem, Nano and the RPS control unit.
As expected, there was no significant difference between the two data sets other than Origin storing more data than was transmitted to the cloud. This was due to the USV drifting off location to test its range. In a real-life situation, a USV or buoy would maintain a set position and link to the Cloud so more data would be transmitted.
The trial proved proof of concept getting data into the Cloud. Further work is now underway into how we can further integrate Origin with floating LiDAR buoys.
Edge’s future value to offshore wind
As discussed, Edge computing enables users to process data directly on the Origin 600 and send only the critical information over the acoustic modem to the topside. This approach has numerous benefits, including early data insights, more efficient data management at the front end and a sense of relief that the unit is performing as expected (or reducing PDA: post-deployment anxiety!).
Implementing Edge computing via an Origin ADCP can help revolutionise the way in-situ ORE monitoring is conducted in the future. Processing the data at source before transmission reduces data overload by focusing solely on critical information. When combined with AI learning, it will reduce data swamping, lead to quicker but better decision-making and, hopefully, help get turbines in the ground sooner. All while advancing the move towards cleaner, greener, autonomous ORE operations.