Overview
Acoustic release transponders are a vital piece of ocean equipment – relied upon by energy, defence and science users to moor valuable equipment strings for years at a time, and when commanded to do so, reliably return equipment and logged data to the surface.
Transponders need to be tough, reliable and easy to work with. RT 6-6000 meets these requirements.
Part of our new range of acoustic releases, RT 6-6000 combines the extensive mechanical design track record of our renowned ORTs and DORTs with the flexibility of our 6G platform, resulting in enhanced battery life and perhaps most significantly, compatibility with our Ranger 2 USBL family
With RT 6-6000, you can use your vessel’s Ranger 2 USBL to deploy, track, locate and command the instrument – removing the need for a separate topside unit. If you don’t have access to a Ranger 2 USBL, our rugged and lightweight Deck Topside with an over-the-side dunker is all you need to both configure and command RT 6-6000s.
At a glance
- Tested, loaded, deployed and released using Deck Topside
- Also works with Sonardyne Ranger 2 USBL to deploy, track and command in very deep water
- Highly reliable release mechanism design and thousands are in service globally
- Working Load Limit 1,275 kg (4:1)
- Depth rated to 6,000 m
- External battery disconnect to maximise battery life with no need to open unit
- Compact and rugged design
RT 6-6000s are most commonly used to anchor oceanographic moorings to the seabed. However, their compact size and compatibility with Ranger 2 makes them ideal for incorporation into instrument frames or lowered platforms to enable deployment of sub-system packages.
Standard features include a Working Load Limit of 1,275 kg (at 4:1) and a spring-assisted release mechanism. RT 6-6000 is compatible with our standard tandem and high-load release frames for scenarios requiring a higher WLL. Speak to us about your requirements as custom frames are also an option.
A battery disconnect fob is located on the transducer and uses an internal magnetic switch to electronically disconnect the battery when not in use. This means you do not have to open the unit to manually disconnect the battery, saving time and reducing the risk of incorrect re-assembly.
RT 6-6000s use the same trusted spring-assisted release mechanism that has been in service for many years and used on thousands of Sonardyne transponders globally.
Choice of topsides
You can use our rugged Deck Topside, or if you’ve got access to a Ranger 2 USBL system on your survey or research vessel, then you have everything you need to control your RT 6-6000.
Versatile
RT 6-6000 is more than just an acoustic release. It can be tracked with our Ranger 2 USBL making relocating and recovering it fast and simple.
High WLL
Use it with our Heavy-Duty Release Frames and significantly increase your Working Load Limit when deploying seabed structures.
Support
You can find a wide range of support articles for our family of acoustic release transponders on our knowledge base.
Specifications table
Feature | Type 8321-6250 |
---|---|
Depth Rating | 6,000 m |
Operating Frequency | LMF (14–19 kHz) |
Transducer Beam Shape | Hemispherical |
Transmit Source Level (dB re 1 µPa @ 1 m) | 188 dB |
Tone Equivalent Energy (TEE) | 192 dB |
Receive Threshold (dB re 1 µPa) | <90 dB |
Working Load Limit (4:1) | 1,275 kg |
Proof Load | 2,550 kg |
Breaking Load | 5,100 kg |
Maximum Safe Release Load | 1,700 kg |
Battery Life (Alkaline) | >32 months |
Inclinometer Accuracy | ±5° |
Surface Unit | Deck Topside, Ranger 2 USBL |
Mechanical Construction | Aluminium bronze and duplex stainless steel |
Operating Temperature | -5 to 40°C |
Storage Temperature | -20 to 55°C |
Dimensions (Length x Diameter | 700 x 142 mm (27.5 x 5.6”) |
Weight in Air/Water | 20/15 kg |
Standards | CE Marked to EN-60945, EN-61010 |
Options | Deep Water Deck Kit (Deck Topside) – 602-0180 |
Heavy Duty Release Frames (7.5 T, 15 T and 25 T) |
Frequently asked questions
What is an Acoustic Release and how does it work?
Why isn’t serial communication available using the iWand in RT 6 Dunker Mode?
6G Terminal Lite Range Test
What is the safe working load for different RT 6 products?
What should I use instead of an ORT and DORT?
How to correctly set an RT 6-6000 release mechanism
How to change the battery on an RT 6-3000 or RT 6000
How to load the release on an RT 6-3000 and RT 6-6000
Which RT 6 is correct for my operations?
How to release an RT 6 acoustic release transponder using Ranger 2
How long can an RT 6-3000 and RT-6 6000 be deployed for?
Deployment
STP files
Software and control hardware
Manuals and quick start guides
Did you know?
RT 6-6000 can be used with our Ranger 2 USBL family or Deck Topside
Overview
Designed for the deployment of our range of USBL and modem transceivers (including Gyro USBL) and Sentinel IDS sonar heads, our through-hull machine provides survey grade rigidity for use with USBL systems up to seven knots (total through water speed) with the ability to survive short duration exposure to higher speeds.
Where the pole is required to be longer than three metres, or where operational water currents may reach 10 knots (total through water speed), the pole must be installed using our heavy duty installation requirements. For specialist or demanding applications, machines of this general type can be custom engineered to suit customer specific requirements. Please consult us if your application has an operational through water speed greater than seven knots.
The machine consists of an electronically controlled but hydraulically operated pole running through a sealed bearing section. A service section (or sea chest) is provided with inspection door to allow fitting and servicing access to the transceiver or sonar head. It is designed to fit on to DN350 and DN500 gate valves however, other gate valves are also supported.
The machine can be controlled from a main control panel or locally at the machine. A bridge control is also available as an option. Hydraulic control of the gate valve is provided as an option. The hydraulic power pack and main control can be mounted remotely if the machine is to be configured for Zone 1 Ex rated classification.
The standard machine can be configured to the meet individual vessel requirements by changing the height of the machine and providing adaptor flanges for different size or specification gate valves. We can provide detailed application advice on positioning, installing and commissioning your machine.
At a glance
- Allows you to deploy instruments from your vessel with maximum performance
- Optimised for Ranger 2 USBL (including HPT modem configurations), Marksman LUSBL, Modem and Sentinel IDS systems
- Choice of through-hull, through-tube and over-the-side designs
- Global track record on all types of vessel: new build and retrofit
- Options for permanent or short term installations on vessel-of-opportunity
Over-the-side
Our modular, over-the-side deployment machine is for vessels where through-hull deployment is not available or practical, or where a temporary installation is required on a vessel-of-opportunity. The design still provides survey grade rigidity without the high cost of dry docking and fitting a gate valve. It can work at operational speeds of up to five knots without degrading USBL positioning performance and to have a survival speed of up to ten knots.
Based on a pivoting sectional pole, the system can be supplied with either a hull or deck mount for the pivot, depending on the vessel arrangement. A brace/lock assembly positioned near the water line and three or four pole sections bolted together to form the arm such that the transceiver on the end of the arm is positioned below the hull by at least 1.5 m. The lower portions of the sectional pole are faired to mitigate against vortex induced vibration which can reduce performance.
The system is not limited to deploying Sonardyne instrument. We can custom engineer adapters for the end of the pole to accommodate third-party sensors.
Through-tube
Popular on very large vessels including drilling rigs, our through-tube deployment machine consists of a hydraulically operated pole, a sealed bearing section and a sea chest service section, with inspection door. The whole machine sits on a gate valve which in turn is mounted on the flange of a through hull penetration pipe.
The ideal deployed length is dependent on your particular application, but in general terms it is best to minimise the deployed pole length to achieve a specified acoustic performance. Typically, a length of between one and three metres below the hull has been found to be acceptable. The pole is very rugged and is designed to be highly resistant to vibration caused by vortex shedding. Operational speeds of up to ten knots through the water may be achieved safely with the ability to survive short duration exposure to higher speeds.
We provide detailed application advice on positioning, installing and commissioning the machine. The sea chest, when the gate valve is closed, provides easy access to the retracted transceiver or sonar for service and inspection purposes. The gate valve also allows the machine to be removed without dry docking. An optional hydraulic drive for the valve is available.
The machine can be controlled from a main control panel or locally at the machine. A bridge control is also available as an option. The hydraulic power pack and main control can be mounted remotely if the machine is to be configured for Zone 1 classification. The standard form of machine can be simply configured to the meet individual vessel requirements by changing the height of the machine and providing adaptor flanges for different size or specification gate valves.
For specialist or demanding applications, machines of this general type can be engineered to suit your specific requirements.
Through-hull
Choose this machine if you’re permanently installing a Sonardyne system on your vessel. Can be retrofitted in existing vessels as well as new.
Over-the-side
Choose this machine if you’re using a vessel-of-opportunity for a short-term project. Can be installed alongside in a harbour and is easy to transport.
Through-tube
Choose this machine if your large vessel has an existing stem tube that can be utilised. Machine is supplied in sections for easy on-site assembly.
Support
Our knowledge base boasts a wide range of articles from our customer support team about deployment machines – from how to protect them, to deployment machine maintenance.
Specifications table
Feature | Type 7950 Through-Hull Transceiver Deployment Machine | ||
---|---|---|---|
Deployment Machine | Transducer Pole | Nickel based (Inconel 625) coated steel pole for corrosion resistance | |
Guide Sealing Section | Contains bronze support bearings plus high integrity 2 stage seal | ||
Service Section | Removable door access to the transceiver without the need to lift the machine | ||
Operational Speed | Standard | 7 knots operational (15 knots survival) | |
Heavy Duty | 10 knots, operational (15 knots survival) | ||
Emergency Operation | Manual hand pump | ||
Length | Maximum available deployed length is 3 m to face of transceiver | ||
Weight | 1,200 kg | ||
Gate Valve | Hydraulic drive available (DN350 and DN500 gate valves available on request) | ||
Power Supply | Nominal 440 V 50-60 Hz 3-phase 3.0 kW (690 V 50-60 Hz 3-phase available) | ||
Limit Switches | Sense position of the transceiver pole and the gate valve. Enable safety interlock | ||
Hydraulic Power Pack | Dimensions (HxWxD) | 632 x 908 x 300 mm | |
Weight | 60 kg | ||
Tank volume | 50 litres Mobil DTE 24 | ||
Working pressure | 100 bar operational (180 bar max.) | ||
Main Control Cabinet | Dimensions (HxWxD) | 600 x 600 x 210 mm | |
Weight | 25 kg | ||
Supply | 24 V dc (internally generated from 440 V) | ||
Local Control Box | Dimensions (HxWxD) | 300 x 150 x 159 mm | |
Weight | 5 kg | ||
Supply | 24 V dc from main control cabinet | ||
Bridge Control (Optional) | As the local control box with dimmer control (flat plate version also available) | ||
Certification | DNV, ABS, Lloyds, BV, CCS, RMRS (others on request) |
Frequently asked questions
Protect your deployment pole & vessel
How to bleed air from a Through-Hull Deployment Machine
Introduction to Through-Hull Deployment Machine
How to create an alarm to warn that the transceiver deployment pole has been left deployed
How to enter Transceiver & Lodestar Offsets for Optimised USBL
Do deployment machines require any kind of maintenance?
What type of grease does the Type 7950 through-hull deployment require?
What type of hydraulic oil does the Type 7950 through-hull deployment machine require?
Which USBL Deployment Machine is most suitable for my vessel?
Deployment
Resources
Software and control hardware
Datasheets
Did you know?
Our deployment machines have been optimised for Ranger 2 USBL, Marksman LUSBL, Modem and Sentinel IDS systems
Overview
Marker 6 is a low cost acoustic positioning transponder for when a compact design and deep operating capability are important operational factors. It enables targets such as underwater structures, vehicles or instrumentation packages to be marked, located or tracked using a Ranger 2 USBL system – Micro, Mini or Standard.
The instrument incorporates Near Field Communications (NFC) allowing for fast set-up. Its acoustic address can be selected from over 200 unique identities meaning that multiple Marker 6s can be deployed in close proximity to each other without causing interference.
At a glance
- Mark and relocate underwater equipment, vehicles and points of interest
- Compatible with all Ranger 2 USBL systems
- Depth rated up to 7,000 m
- More than 30 months’ listening life (lithium battery option)
- Over 200 unique acoustic addresses
On the backdeck, the address can be quickly programmed into each transponder using a suitable NFC enabled handset (including an NFC enabled Android™ handset with the Sonardyne NFC App) or a dedicated HF Radio Frequency Identification (RFID) reader.
Sonardyne Wideband signal encoding reduces the interference both on and by adjacent Sonardyne and other acoustic positioning systems.
The NFC link provides the ability to enter Marker 6 into a storage mode when not in use, thereby significantly increasing the overall battery endurance.
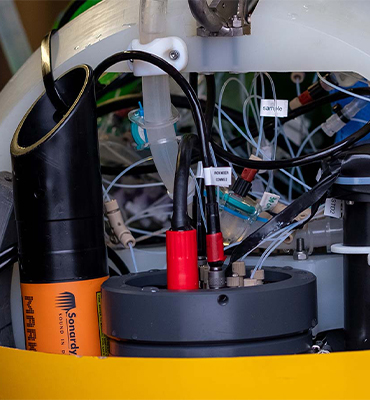
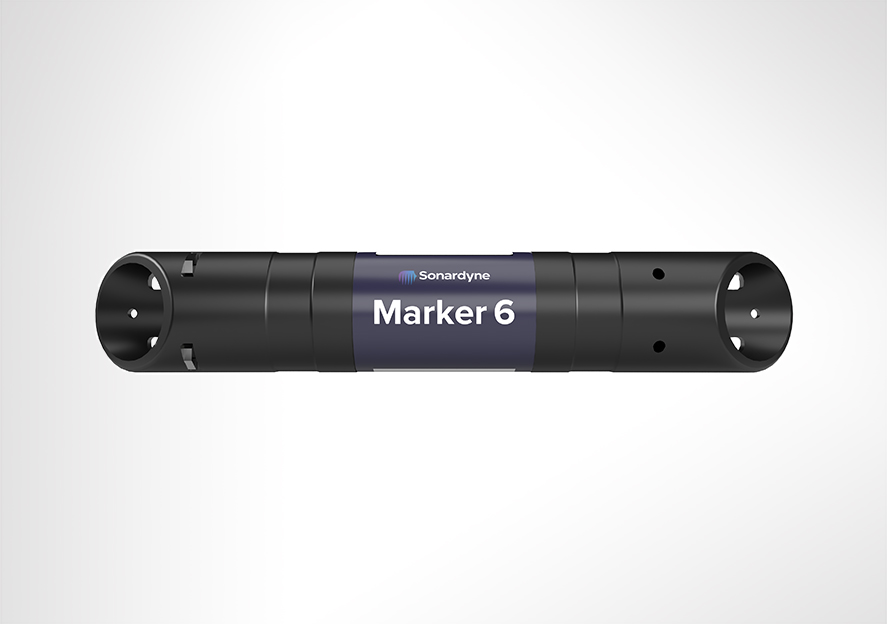
Specifications table
Feature | Type 8326-4311 | Type 8326-7511 | |
---|---|---|---|
Depth Rating | 4,000 m | 7,000 m | |
Operating Frequency | MF (20–34 kHz) | MF (20–34 kHz) | |
Transducer Beam Shape | Omni-directional ±130º | Omni-directional ±130º | |
Transmit Source Level (re 1 µPa @1 m) | 187 dB | 187 dB | |
Inclinometer Sensor | ±5° | ±5° | |
Battery Life (Continuously Listening) | Alkaline | >9.5 months | >9.5 months |
Lithium | >30 months | >30 months | |
Storage Mode (Battery Disconnect via NFC) | Alkaline | 5 years (battery self-discharge limited) | 5 years (battery self-discharge limited) |
Lithium | >10 years (battery self-discharge limited) | >10 years (battery self-discharge limited) | |
Operating Temperature Range | -5 to 40°C | -5 to 40°C | |
Storage Temperature Range | -20 to 55°C | -20 to 55°C | |
Mechanical Construction | Outer Housing | Polypropylene | Polypropylene |
Inner Housing | Duplex stainless steel | Titanium grade 5 | |
Dimensions (Length x Diameter) | 383.0 x 63.0 mm (15.1 x 2.5”) | 383.0 x 63.0 mm (15.1 x 2.5”) | |
Weight in Air/Water | 2.0/1.3 kg | 1.5/0.7 kg |
Frequently asked questions
Software and control hardware
Datasheets
Manuals and quick start guides
Did you know?
Marker 6 is compatible with all of our Ranger 2 USBL systems
Overview
Built around our field-proven 6G hardware and Wideband 2 acoustic signal platforms, Modem 6 surface units support secure subsea-to-surface wireless data transfer at speeds between 200 and 9,000 bps.
This makes them ideal for applications such as: near real-time data streaming, data harvesting from third party sensors or subsea command and control of equipment.
Modem 6 acoustic modems are aimed at simple data transfer applications which do not require the more complex functions such as integrated (USBL) positioning, on-board sensors or complex multi-node array telemetry. If you need any of these capabilities, or an OEM solution which you can integrate into your own instrument or vehicle, our application experts will be happy to discuss your requirements and identify the right solution for you.
We offer a variety of surface deployed acoustic Modem 6 to suit any operational deployment scenario and data transfer mission. You can mount them on a variety of surface platforms ranging from buoys to all sizes of vessels – both manned and uncrewed – to interact with any of our subsea deployed Modem 6 instruments.
At a glance
- Transfers data at up to 9,000 bps
- Highly reliable – built around our Wideband 2 acoustic and 6G hardware platform
- Options for buoys, uncrewed surface vehicles and ships
Modem 6 Transceiver
Manufactured in Aluminium Bronze, the Modem 6 Transceiver is intended to be fitted temporarily or permanently to a vessel’s through-hull or over-the-side pole or mounted in a dunker cage assembly. The unit uses the same array as our HPT 5000/7000 transceiver so can be upgraded in the field to offer this capability if integrated communications and target tracking is required. As standard, the unit is supplied with Surface Interface Unit (SIU), deck cable, 100 m cable drum and a dunker cage which allows deployment over the side in the absence of a through-hull deployment pole.
Modem 6 Dunker
Modem 6 Dunker is a popular option for low-logistic data recovery missions using survey vessels-of-opportunity. Depth rated to 1,000 m, it can also be fitted to ROVs for close range data transfer from seafloor sensors. It’s available in MF and LMF, with omni-directional or directional transducer designed for excellent horizontal and shallow water communication. Modem 6 Dunker is powered using a supplied Surface Interface Unit (SIU).
Modem 6 Mini Dunker
Modem 6 Mini-Dunker is our smallest topside option. It is compact, easy-to-mount and suitable for transmission and recovery of data from a wide range of sensors including: current profilers, temperatures, depth and custom instrumentation. The Modem 6 Mini-Dunker is available in MF with an omnidirectional transducer designed for excellent horizontal and shallow water communication. The surface system comprises of a Modem 6 Mini-Dunker, Surface Interface Unit (SIU) and 20 m deck cable.
All of our family of underwater Modem 6 instruments benefit from same mechanics and electronics you’ll find in our other 6G transponders. These are trusted by leading offshore operators to perform in the most demanding marine environments and operational scenarios.
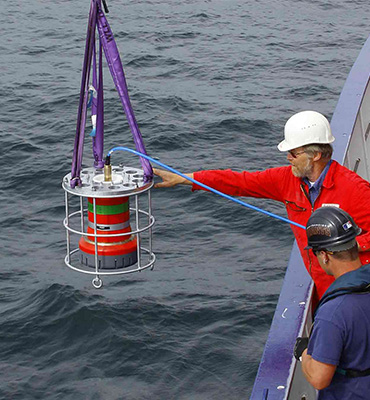
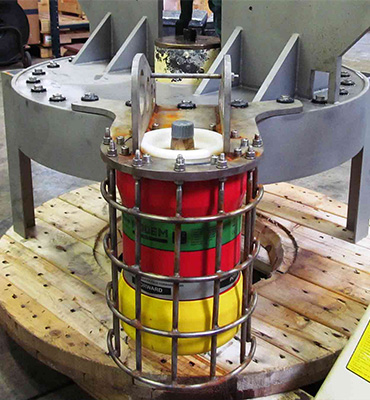
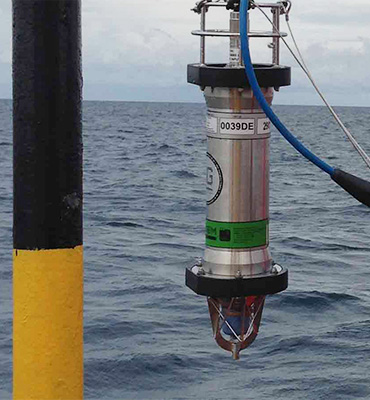
Specifications table
Feature | Type 8244-3151 | Type 8244-3155 | Type 8307-1351 | Type 8307-1353 | Type 8307-1355 | Type 8307-1356 | Type 8182-0001 | Type 8193-0012 |
---|---|---|---|---|---|---|---|---|
Depth Rating | 3,000 m | 3,000 m | 1,000 m | 1,000 m | 1,000 m | 1,000 m | Up to 7,000 m (operating range) | Up to 12,000 m (operating range) |
Operating Frequency | MF (20–34 kHz) | LMF (14–19 kHz) | MF (20–34 kHz) | MF (20–34 kHz) | LMF (14–19 kHz) | LMF (14–19 kHz) | MF (20–34 kHz) | LMF (14–19 kHz) |
Beam Shape | Omni-directional | Omni-directional | Omni-directional | Directional | Omni-directional | Directional | Omni-Directional | Directional |
Transmit Source Level (dB re 1 µPa @ 1 m) | 181-187 dB | 187-190 dB | 187–196 dB (4 levels) |
190–202 dB (4 levels) |
187–196 dB (4 levels) |
187–202 dB (4 levels) |
200 dB | 200 dB |
Power Supply | Lithium-ion or external 24 V | Lithium-ion or external 24 V | Lithium-ion or external 24 V | Lithium-ion or external 24 V | Lithium-ion or external 24 V | Lithium-ion or external 24 V | External Supply | External Supply |
Battery Life | 30 days | 30 days | 3 days | 3 days | 3 days | 3 days | n/a | n/a |
Operating Temperature | -5 to 40°C | -5 to 40°C | -5 to 40°C | -5 to 40°C | -5 to 40°C | -5 to 40°C | -5 to 40°C | -5 to 40°C |
Storage Temperature | -20 to 55°C | -20 to 55°C | -20 to 55°C | -20 to 55°C | -20 to 55°C | -20 to 55°C | -20 to 45°C | -20 to 45°C |
Dimensions (Length x Diameter) | 518 x 94 mm | 604 x 94 mm | 608 x 200 mm | 660 x 200 mm | 577 x 200 mm | 632 x 230 mm | 370 x 225 mm | 439 x 310 mm |
Weight in Air/ Water | 5.1/ 2.2 kg | 7.0/ 3.5 kg | 24/ 16 kg | 26/ 17 kg | 20/ 14 kg | 28/ 17 kg | 28/ 15 kg | 41/ 20 kg |
Frequently asked questions
How is data validated with Modem 6?
What modes are available with Modem 6?
How is data sent over the MDFT link with Modem 6?
Is there a handshaking mechanism or other link-establishing sequence?
Does Modem 6 support the MODBUS protocol?
Is simultaneous broadcasting and reception of messages supported with Modem 6?
What data rates should i expect from Modem 6?
What is the typical power consumption of a Modem 6?
How many topside modems do i need?
Which Modem 6 product best suits my application?
Modem 6 (point to point) or 6G telemetry (network comms)
Integration guides
Did you know?
Modem 6 (surface) is depth rated up to 12,000 m
Overview
Built around our field-proven 6G hardware and Wideband 2 acoustic signal platforms, Modem 6 subsea units support secure subsea-to-surface wireless data transfer at speeds between 200 and 9,000 bps.
This makes them ideal for applications such as: near real-time data streaming, data harvesting from third party sensors or subsea command and control of equipment.
Modem 6 acoustic modems are aimed at simple data transfer applications which do not require the more complex functions such as integrated (USBL) positioning, on-board sensors or complex multi-node array telemetry. If you need any of these capabilities, or an OEM solution which you can integrate into your own instrument or vehicle, our application experts will be happy to discuss your requirements and identify the right solution for you.
We offer a variety of subsea-deployed acoustic Modem 6 units to suit any operational deployment scenario and data transfer mission. You can mount them on a variety of platforms ranging from seafloor installations to an AUV and transmit sensor or platform status data between instruments or to a surface buoy or vehicle.
At a glance
- Recommended for simple data retrieval projects
- Low cost and simple to configure
- Delivers up to 9,000 bps user data rate
- Depth ratings to 5,000 m
Modem 6 Sub-Mini
Modem 6 Sub-Mini is a compact and easy-to-mount instrument, suitable for transmission of data from a wide range of sensors including: current profilers, temperatures, depth and custom instrumentation. Type 8377-1111 is depth rated to 1,000 m and has an omni-directional transducer designed for excellent horizontal and shallow water communication. Type 8377-4112 is depth rated to 4,000 m and has a directional transducer.
Modem 6 Mini
Modem 6 Mini is available in MF with an omni-directional or directional transducer designed for excellent horizontal and shallow water communication. Both versions are depth rated to 3,000 m and have an internal battery offering 30 days listening life. External trickle charging is also supported.
Modem 6 Standard
Based on the field proven mechanics of Compatt 6 and DPT 6, Modem 6 Standard is a full-sized transponder with large internal battery pack making it suitable for long term deployments of multiple years. It’s also able to power external, third party sensors. Depth ratings of 5,000 m are available.
All of our family of underwater Modem 6 instruments benefit from same mechanics and electronics you’ll find in our other 6G transponders. These are trusted by leading offshore operators to perform in the most demanding marine environments and operational scenarios.
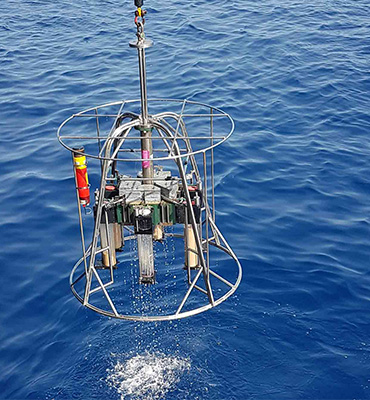
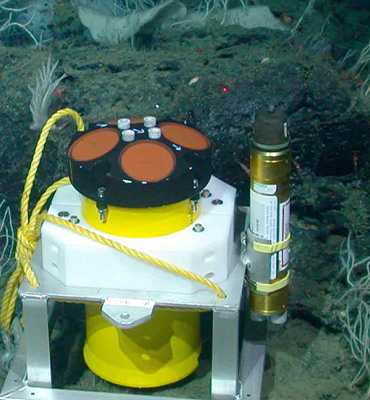
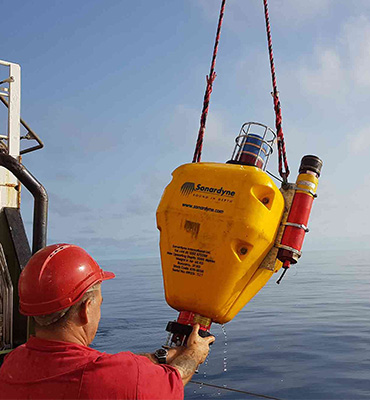
Specifications table
Feature | Type 8377-1111 | Type 8377-4112 | Type 8244-3111 | Type 8244-3112 | Type 8307-3111 | Type 8307-3113 | Type 8307-5213 |
---|---|---|---|---|---|---|---|
Depth Rating | 1,000 m | 4,000 m | 3,000 m | 3,000 m | 3,000 m | 3,000 m | 5,000 m |
Operating Frequency | MF (20–34 kHz) | MF (20–34 kHz) | MF (20–34 kHz) | MF (20–34 kHz) | MF (20–34 kHz) | MF (20–34 kHz) | MF (20–34 kHz) |
Transceiver Beam Shape | Omni-directional | Directional | Omni-directional | Directional | Omni-directional | Directional | Directional |
Transmit Source Level (dB re 1 µPa @ 1 m) | 181 dB | 187 dB | 181-187 dB | 187-193 dB | 187–196 dB (4 levels) | 190–202 dB (4 levels) | 190–202 dB (4 levels) |
Power Supply | Rechargeable NiMH battery or external 24 V |
Rechargeable NiMH battery or external 24 V |
Lithium-ion or external 24 V | Lithium-ion or external 24 V | Alkaline or Lithium battery or external 24 V |
Alkaline or Lithium battery or external 24 V |
Alkaline or Lithium battery or external 24 V |
Battery Life | >35 days | >35 Days | 30 Days | 30 Days | Alkaline = 833 days Lithium = 1390 days |
Alkaline = 833 days Lithium = 1390 days |
Alkaline = 833 days Lithium = 1390 days |
Operating Temperature | -5 to 40°C | -5 to 40°C | -5 to 40°C | -5 to 40°C | -5 to 40°C | -5 to 40°C | -5 to 40°C |
Storage Temperature | -20 to 55°C | -20 to 55°C | -20 to 55°C | -20 to 55°C | -20 to 55°C | -20 to 55°C | -20 to 55°C |
Dimensions (Length x Diameter) | 420 x 75 mm | 429 x 97 mm | 501 x 94 mm | 512 x 97 mm | 955 x 200 mm (excluding release) | 925 x 200 mm (excluding release) | 925 x 200 mm (excluding release) |
Weight in Air/ Water | 3.2/ 1.3 kg | 5.5/ 3.2 kg | 5.1/ 2.2 kg | 7.0/ 3.5 kg | 23.8/ 11.8 kg | 23.8/ 11.8 kg | 23.8/ 11.8 kg |
Frequently asked questions
How is data validated with Modem 6?
What modes are available with Modem 6?
How is data sent over the MDFT link with Modem 6?
Is there a handshaking mechanism or other link-establishing sequence?
Does Modem 6 support the MODBUS protocol?
Is simultaneous broadcasting and reception of messages supported with Modem 6?
What data rates should i expect from Modem 6?
What is the typical power consumption of a Modem 6?
How many topside modems do i need?
Which Modem 6 product best suits my application?
Modem 6 (point to point) or 6G telemetry (network comms)
How to replace a battery in Compatt 6 and 6+ family of transponders
Datasheets
Integration guides
Did you know?
Modem 6 (subsea) is available in a range of sizes to suit your application
Overview
Our range of subsea floatation collars enable acoustic navigation and positioning transponders to be deployed, moored on the seabed and then recovered to the surface.
The floats are compatible with all our transponders including: Compatt 6+, Compatt 6, AMT 6 and DPT 6. They can be used with directional and omni-directional transducer types.
Manufactured from high performance materials appropriate to the required depth rating, each float assembly comes in two halves and is clamped around the transponder using stainless steel fixings made of super duplex stainless steel.
Bright colours make sure good visibility, either when subsea and viewed from an ROV’s camera, or when floating on the surface prior to recovery.
At a glance
- Use it to recover seabed transponders without ROV intervention
- Choice of shapes to suit application and environment
- Available in 3,000, 5,000 and 7,000 metre depth ratings
We also supply ultra low-drag light bulb shaped float that provide significant reduction of the deflection caused by water currents and dramatically improves the stability of the transponder. The levels of both the deflection and stability directly affect the quality of the achievable positioning. The light bulb float therefore ensures optimum performance from the seabed installed transponders.
The ultra low-drag and highly stable float further allows users to deploy transponders much higher off the seabed increasing the achievable acoustic range. This reduces the required number of transponders enabling life of field positioning without requiring complicated deflection correction methods.
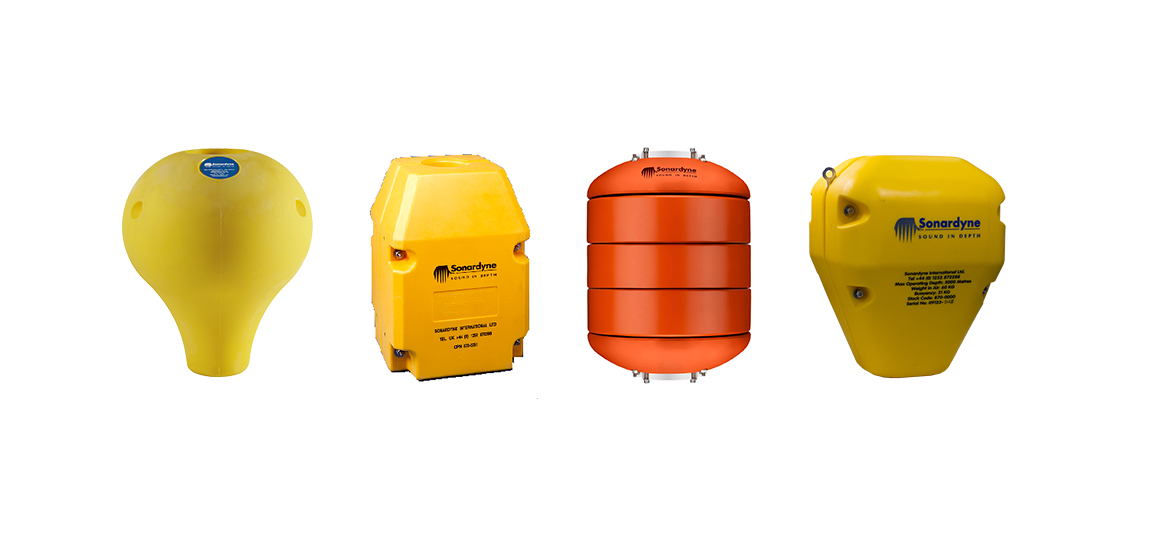
Ultra Low-Drag transponder floatation collar
Compatt/DPT transponder floatation collar
Modular float
Compatt/DPT floatation collar (directional units only)
Specifications table
Model | Specification | |
---|---|---|
Floatation Collar – 3,000 m | Depth rating | 3,000 m |
Weight in air | 64 kg | |
Nett buoyancy | 32.7 kg | |
Dimensions (length x width x diameter) | 595 x 445 x 445 mm | |
Floatation Collar – 5,000 m | Depth rating | 5,000 m |
Weight in air | 64.2 kg | |
Nett buoyancy | 32.1 kg | |
Dimensions (length x width x diameter) | 595 x 445 x 445 mm | |
Floatation Collar – 7,000m | Depth rating | 7,000 m |
Weight in air | 64 kg | |
Nett buoyancy | 27 kg | |
Dimensions (length x width x diameter) | 595 x 445 x 445 mm | |
Floatation Collar – Directional | Depth rating | 5,000 m |
Weight in air | 61 kg | |
Nett buoyancy | 35 kg | |
Dimensions (length x width x diameter) | 650 x 500 x 500 mm | |
Floatation Collar – Ultra Low Drag | Depth rating | 3,000 m |
Weight in air | 60.5 kg | |
Nett buoyancy | 34.5 kg | |
Dimensions (length x width x diameter) | 699 x 600 mm |
Frequently asked questions
Transponders
Datasheets
Did you know?
Our floatation collars are suitable for both Compatts and DPTs and are depth rated up to 7,000 m
Overview
Gyro iUSBL combines our generation high performance HPT Inverted USBL transceiver and a Lodestar Attitude and Heading Reference System (AHRS)/Inertial Navigation System (INS) in the same titanium pressure rated mechanical assembly capable of operating at depths of 7000 m.
With the AHRS/INS in fixed mechanical alignment to the iUSBL’s pressure balanced acoustic array, the Gyro iUSBL can be quickly deployed without need for a calibration to determine the alignment of the ship’s motion sensors to the acoustic transceiver. For many applications, this can enable significant time savings and operational costs.
At a glance
- Designed to work with Ranger 2 USBL
- Tracks your deep tow vehicle beyond 10,000 m
- Integrated USBL transceiver and SPRINT INS
- Depth rated to 7,000 m
- Offers 10x improvement in positioning precision
Specifications table
Features | Type 8084-000-7535 | |
---|---|---|
Operational Frequency | MF (20–34 kHz) | |
Transceiver Performance |
Operating Range | Up to 7,000 m |
Pressure Rating | Up to 7,000 m | |
Acoustic Coverage | Up to ± 90° | |
Range Accuracy Positioning Repeatability | Better than 15 mm All transceivers tested to Better Than 0.1% of Slant Range 1 drms |
|
Transmit Source Level (dB re 1 µPa @ 1 m) | 200 dB | |
Tone Equivalent Energy (TEE) | 206 dB | |
Heading | Range | 0–360° |
Accuracy | 0.05 to 0.1° secant latitude | |
Settle Time | <5 minutes | |
Follow Up Speed | 500° / second | |
Resolution | 0.01° | |
Pitch & Roll | Range | ±180º (No physical limit) |
Accuracy | 0.01° | |
Resolution | 0.01° | |
Heave | Range | ±99 m |
Accuracy (Real Time) | 5 cm or 5% (whichever the greater) | |
Resolution | 0.01 m | |
Electrical | +48 V dc maximum 160 W | |
Communication | RS485, baud rate switchable, ethernet 100 Mbps | |
Operating Temperature | -5 to 40°C | |
Storage Temperature | -20 to 55°C | |
Dimensions (Length x Diameter) | 475.5 mm x 240 mm (without end connector) | |
Weight in Air/Water | 45/24 kg |
Frequently asked questions
Software and firmware
Datasheets
Manuals and quick start guides
Did you know?
Gyro iUSBL is depth rated up to 7,000 m
Overview
iWand is our small, splashproof acoustic transponder test and configuration device. Use it with your 6G acoustic subsea hardware to set up transponders quickly and efficiently – whether you’re in the workshop getting ready for your next mobilisation or out on the back deck and just about to deploy.
iWand is used in conjunction with 6G configuration software running on your survey room or workshop PC. It enables all 6G (excluding WSM 6 which can only be acoustically tested) transponders to be easily configured. The configuration of the various transponders can then be exported to a document as an audit trail, or to a file that can be imported into Sonardyne positioning system navigation software packages like Fusion 2.
The simple to use interface and sunlight readable display makes it easy to test, gather and download configurations in all weathers, day or night.
At a glance
- Engineered for the workshop or out on the back deck
- Works with all 6G transponders
- Use it to acoustically test, configure and save settings for QC
- Splash-proof, rugged and portable design
- Speeds up pre-deployment checks – allows batch settings to be uploaded
Communication to a transponder is via the acoustic ‘wand’ antenna which is held against the transponder’s acoustic transducer. This tests the acoustic transmission and reception functions of the transponder ensuring they are operating correctly – a key performance indicator.
iWand has various PC connection options: Bluetooth, USB or serial. The USB is used to recharge the internal battery.
The internal GPS receiver provides UTC time tagging of communication to transponders and PC and can also be used to synchronise multiple transponders to UTC for logging applications.
Specifications table
Feature | Type 8315 | |
---|---|---|
Operating frequency | LMF (14–19 kHz), MF (20–34 kHz), HMF (34–40 kHz) | |
Transducer beam shape (Wand) | Directional | |
Case | Rugged polypropylene copolymer case with styrenic over mould shock protection | |
Keypad | Sealed 5 key navigation pad | |
Display | 320 x 240 sunlight readable LED display | |
Connections | USB | Splash-proof mini-USB Type B IP67 |
Serial | 9-way D-Type (male) IP67 | |
Bluetooth | V2.1 + EDR Class 2 (+4 dBmi) | |
BNC | Acoustic wand | |
Charging | USB to PC or USB to wall adaptor | |
Internal flash memory | 1 GB | |
Battery | Li-ion 3.7 V 1,300 mAh (typical) | |
Battery life | Normal (screen on) | >5 hours (screen automatically turns off after a selectable period) |
Idle (screen off) | >12 hours (press a key or ‘shake to wake’ to turn screen back on) | |
Off | >3 months (press a key to wake) | |
Off for shipping | >1 year (requires USB connection to wake) | |
Operating temperature | -10 to 55°C | |
Storage temperature | -10 to 55°C | |
Dimensions (length x width x depth) | 276 x 84 x 40 mm | |
Weight | 0.8 kg |
Frequently asked questions
Why isn’t serial communication available using the iWand in RT 6 Dunker Mode?
How to change the address of a DART using an iWand
How to set the latitude on a Gyro Compatt 6
How to correctly set a DPT 6 release mechanism
How can I deploy my Compatt 6+ using iWand?
How to correctly set a Compatt 6+ release mechanism
How to correctly set an RT 6-6000 release mechanism
How to correctly set a PIES release mechanism
How to load the release on an RT 6-3000 and RT 6-6000
Software and firmware
Datasheets
Manuals and quick start guides
Did you know?
iWand has various PC connection options: Bluetooth, USB or serial
Overview
The instrument is a turn-key solution comprised of carefully selected high grade and highly reliable inertial sensors integrated into in-house designed inertial measurement unit (IMU).
The selected inertial sensors are the standard for commercial aviation with a proven 20+ year track record. These sensors have a highly desirable characteristic being insensitive to vibration, temperature changes and having very limited initial errors. The result is a system which is highly suitable for the marine environment where performance, robustness and data integrity need to be available from initialisation, even during the harshest conditions.
Lodestar requires no external aiding and settles robustly in dynamic conditions in less than five minutes. On-board data storage and backup battery functionality ensures continued operation and eliminates the risk of data loss even if communications or external power are lost. Power-pass through to external aiding sensors is supported to ease integration requiring only a single cable for comms and power.
If a full INS solution is required, Lodestar can easily be field upgraded to a SPRINT system (apart from Lodestar 200). This makes the Lodestar a flexible and future-proof solution for both ROV guidance and survey applications.
Lodestar has a proven track record spanning more than 10 years in the field in diverse applications from ROV guidance and autopilot to demanding survey applications. The instrument is available in 4,000 and 6,000 metre depth ratings with a variety of connector options and configurations.
At a glance
- Designed to aid subsea vehicle guidance: AUVs, ROVs and UUVs
- Uses high quality Honeywell gyro and accelerometers
- Sensors available in three performance levels: 200, 300 and 500
- Fast settling time so you can get straight to work
- Integrated DVL option available; Lodestar-Nav
- Factory upgradeable to SPRINT INS
Lodestar-Nav 200
Lodestar-Nav 200 provides all-in-one navigation solution for subsea vehicles by combining a Lodestar 200 AHRS with our Syrinx Doppler Velocity Log (DVL) and a high accuracy pressure sensor in a single housing. This saves cost, payload space and the complexity of integrating and operating separate sensors from different vendors.
Lodestar-Nav is pre-calibrated providing the ROV pilots with a robust and reliable solution, even in the most challenging operational scenarios, without needing to worry about sensor offsets.
Syrinx DVL inside that provides a large altitude range and high precision at all altitudes; this combines the best of 300 and 1200 kHz DVLs. Each DVL transducer is fitted with a full depth rated water block to ensure protection of the internal components and easy replacement if damaged.
Lodestar-Nav can be interfaced via a single connection and/or the DVL can be interfaced separately depending on requirements. Continuous on-board data storage supports post-mission diagnostics and post-processing.
Size
Measuring just 260 mm tall, the 4,000 m rated titanium housing allows easy fitment to any subsea vehicle. 6,000 m housing option.
Long life sensors
Lodestars and SPRINTs use Honeywell-supplied RLGs and inertial sensors with 400,000 MTFB, which have been proven in over 20 years in commercial aircraft.
Connectivity
Most Lodestars can be upgraded to SPRINT in the field as your requirements grow so there’s no need to remove and re-install a different instrument.
Specifications
Feature | Lodestar 300 | Lodestar 500 | |
---|---|---|---|
Depth rating | 4,000 / 6,000 m | 4,000 / 6,000 m | |
Heading | 0.2° | 0.1° | |
AHRS settle time | <5 minutes in dynamic conditions | <5 minutes in dynamic conditions | |
Roll and pitch | 0.01° | 0.01° | |
Power requirement | 20–50 V dc, 15 W nominal, 35 W maximum | 20–50 V dc, 15 W nominal, 35 W maximum | |
Power pass through | 3 x for external aiding sensors (up to 3A per sensor) | 3 x for external aiding sensors (up to 3A per sensor) | |
Back up battery type/life | Li-ion/5 minutes | Li-ion/5 minutes | |
Data storage | 8 GB internal memory | 8 GB internal memory | |
Serial ports/protocol | 4x RS232 or RS485 | 4x RS232 or RS485 | |
Other ports | 1x Ethernet, 4 triggers | 1x Ethernet, 4 triggers | |
Output rate | Up to 100 Hz | Up to 100 Hz | |
Output telegrams | Industry standard AHRS/INS telegrams including acceleration and rotation rates | Industry standard AHRS/INS telegrams including acceleration and rotation rates | |
Connectors | 4x Seacon / Seanet, 1x Seacon / Seanet | 4x Seacon / Seanet, 1x Seacon / Seanet | |
Mechanical construction | Titanium | Titanium | |
Dimensions (diameter x height) |
4,000 m (Seacon) | 205 x 260 mm | 205 x 260 mm |
6,000 m (Seacon) | 205 x 280 mm | 205 x 280 mm | |
4,000 m (Seanet) | 205 x 250 mm | 205 x 250 mm | |
Weight in air/water | 4,000 m | 18.5/11.5 kg | 18.5/11.5 kg |
6,000 m | 22/14 kg | 22/14 kg | |
Operating temperature | -20 to +55°C | -20 to +55°C | |
Storage temperature | -20 to +60°C | -20 to +60°C | |
Shock rating | 22 g, 11 ms half sine | 22 g, 11 ms half sine |
Frequently asked questions
SPRINT, SPRINT-Nav, Lodestar and Lodestar-Nav troubleshooting
How to connect to the Lodestar within a Gyro USBL via an NSH
How to enter Transceiver & Lodestar Offsets for Optimised USBL
What cables do I need for my Lodestar?
How do I mate and calibrate a DVL to my Lodestar?
Can I power my subsea instruments with Lodestar or SPRINT?
How do I mate and calibrate a SPRINT or Lodestar to my Syrinx DVL?
What’s the difference between FOG and RLG?
STP files
Software and firmware
Software and control hardware
Manuals and quick start guides
Technical bulletin
Did you know?
Lodestar is highly optimised for cost, size, weight and power (C-SWaP)
Overview
ROVNav 6+ uses our new Wideband 3 signal technology, which is key to unlocking the benefits of your Fusion 2 LBL system.
It allows, for the first time, sensor telemetry data (e.g. pressure, depth or temperature) from a seabed or structure deployed Compatt 6+ to be embedded within navigation (ranging) data. This change has a big impact on operations such as structure installation, as breaks in tracking to get sensor reading updates at vital moments are now a thing of the past.
Its compatibility with Wideband 3 and Wideband 2 telemetry commands, and support of high power Wideband 2 ranging protocols, proven for their accuracy and robustness, means the ROVNav 6+ offers improved range and acoustic performance in challenging conditions such as on noisy vehicles or in multipath environments.
At a glance
- High power, long range LBL transceiver for ROVs
- Wideband 3-enabled supporting embedded sensor data with ranging data
- Optimised for Fusion 2 and compatible with Fusion 1
- 3,000, 5,000 or 7,000 m depth rated options
- USBL mode for emergency ROV relocation
- Modem mode for harvesting data from Sonardyne logging sensors; Fetch, AMT…
ROVNav 6+ is also a fully functional USBL responder or transponder, compatible with Wideband 2 USBL systems and HPR400. The internal li-ion rechargeable battery pack also enables emergency transponder mode, so if the umbilical and therefore power is cut to the ROV it can still be located by USBL.
The omni-directional remote MF transducer makes installation on an ROV easy. ROVNav 6+ is designed to be rugged and relatively lightweight and utilises robust underwater connectors. ROVNav 6+ supports a range of internal sensors including: strain gauge pressure, PRT temperature and MEMS based inclinometer.
ROVNav 6+ is also fully compatible with our modem and logging equipment such as AMT and Fetch products, allowing it to be used to retrieve data or configure logging regimes. It supports all of our Wideband 2 and Wideband 3 spread spectrum acoustic communication; 100 to 9,000 bps data rates can be selected depending on the environment.
Sensor options include a Digiquartz pressure sensor, precision inclinometer and altimeter interface. This provides a fully featured ROV manipulator deployable tool/sensor pack for a range of different applications including metrology, bathy survey and structure deployment operations, without the requirement for any additional interfacing on the ROV.
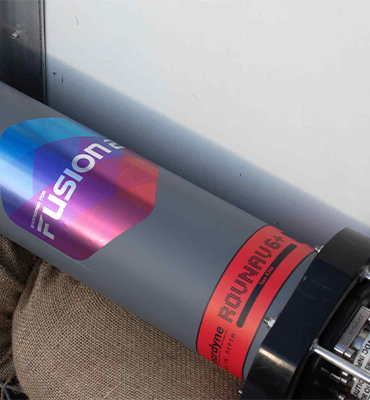
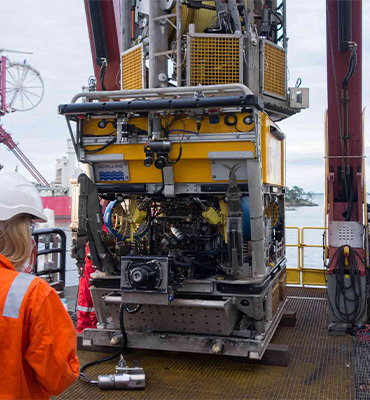
Specifications table
Feature | 8340-3161 | 8340-5261 | 8340-7261 |
---|---|---|---|
Depth Rating | 3,000 m | 5,000 m | 7,000 m |
Operating Frequency | MF (20–34 kHz) | MF (20–34 kHz) | MF (20–34 kHz) |
Transducer Beam Shape | Omni-directional | Omni-directional | Omni-directional |
Transmit Source Level (dB re 1 µPa @ 1 m) | 187–196 dB (4 levels) | 187–196 dB (4 levels) | 187–196 dB (4 levels) |
Range Precision | Better than 15 mm | Better than 15 mm | Better than 15 mm |
Serial Communications | RS232 or RS485 (half-duplex) | RS232 or RS485 (half-duplex) | RS232 or RS485 (half-duplex) |
Battery Life Li-ion (Listening) | 3 days | 3 days | 3 days |
Operating Voltage | 24 or 48 V dc (±10%) | 24 or 48 V dc (±10%) | 24 or 48 V dc (±10%) |
Serial Communications Connector | Subconn (8-way female) | Subconn (8-way female) | Subconn (8-way female) |
Remote Transducer Connector | Burton (3-way male) | Burton (3-way male) | Burton (3-way male) |
Housing Mechanical Construction | Hard anodised aluminium 6082 | Hard anodised aluminium 7075 | Hard anodised aluminium 7075 |
Remote Transducer Mechanical Construction | Stainless steel 316 | Stainless steel 316 | Stainless steel 316 |
Dimensions (Maximum) (Length x Diameter) | 768 x 200 mm | 768 x 200 mm | 768 x 200 mm |
Weight in Air/Water | 14.3/5.3 kg | 14.7/5.7 kg | 15.5/6.0 kg |
Frequently asked questions
If I’m using Fusion 2, can I choose to use Wideband 2 or Wideband 3 telemetry?
Can ROVNav 6+ be used with standard Compatt 6s?
Will my ROVNav 6 work with Fusion 2?
Do I need to upgrade to Compatt 6+ and ROVNav 6+?
Where should I install my ROVNav 6+ transducer?
What are the differences between a ROVNav 6+ and Mini ROVNav 6+ ?
How to QC a Sound Velocity (SV) in Fusion 2
How far can my Compatt 6+ be above the seabed?
How do I perform an LBL calibration in Fusion 2?
STP files
Software and firmware
Transponders
Datasheets
Manuals and quick start guides
Technical bulletin
Did you know?
ROVNav 6+ is compatible with Fusion 1 and can be depth rated up to 7,000 m