Overview
ROVNav 6 has been superseded by ROVNav 6+
ROVNav 6 is a 6G Wideband 2 ranging LBL ROV Transceiver and telemetry transceiver specifically designed for installation on work class ROVs.
At a glance
- Use it with Fusion 6G
- Wideband 2 enabled
- High power, long range LBL transceiver
- 3,000, 5,000 or 7,000 m depth rated
- USBL mode for emergency ROV relocation
- Modem mode for harvesting data from Sonardyne sensors
Specifications table
Feature | 8310-3161 | 8310-5261 | 8310-7261 | |
---|---|---|---|---|
Depth rating | 3,000 m | 5,000 m | 7,000 m | |
Operating frequency | MF (20–34 kHz) | MF (20–34 kHz) | MF (20–34 kHz) | |
Transducer beam shape | Omni-directional | Omni-directional | Omni-directional | |
Transmit source level (dB re 1 µPa @ 1 m) | 187–196 dB (4 Levels) | 187–196 dB (4 Levels) | 187–196 dB (4 Levels) | |
Tone Equivalent Energy (TEE) | 193–202 dB | 193–202 dB | 193–202 dB | |
Receiver sensitivity (dB re 1 µPa) | 90–120 dB | 90–120 dB | 90–120 dB | |
Range precision | Better than 15 mm | Better than 15 mm | Better than 15 mm | |
Serial communications (software programmable) |
Primary port | RS232 or RS485 (half-duplex) | RS232 or RS485 (half-duplex) | RS232 or RS485 (half-duplex) |
Secondary port | RS232 or RS485 (half-duplex) or SYNC IN | RS232 or RS485 (half-duplex) or SYNC IN | RS232 or RS485 (half-duplex) or SYNC IN | |
Battery life Li-ion (listening) | 3 days | 3 days | 3 days | |
Operating voltage | 24 or 48 V dc (±10%) | 24 or 48 V dc (±10%) | 24 or 48 V dc (±10%) | |
External power | Active (listening) | <3 W typical (maximum 10 W when charging) | <3 W typical (maximum 10 W when charging) | <3 W typical (maximum 10 W when charging) |
Peak (during transmission) | <80 W | <80 W | <80 W | |
Serial communications connector | AGP (8-way female) |
AGP (8-way female) |
Subconn (8-way female) |
|
Remote transducer connector | AGP (4-way male) | AGP (4-way male) | Burton (3-way male) | |
Housing mechanical construction | Hard anodised aluminium 6082 |
Hard anodised aluminium 7075 |
Hard anodised aluminium 7075 |
|
Remote transducer mechanical construction | Stainless steel 316 | Stainless steel 316 | Stainless steel 316 | |
Dimensions (maximum) (length x diameter) | 768 x 200 mm | 768 x 200 mm | 768 x 200 mm | |
Housing diameter | 134 mm | 134 mm | 140 mm | |
Weight in air/water | Housing assembly | 14.3/5.3 kg | 14.7/5.7 kg | 15.5/6.0 kg |
Transducer | 3.2/2.7 kg | 3.2/2.7 kg | 3.3/2.8 kg | |
Cable (5 m) | 2.7/1.4 kg | 2.7/1.4 kg | 2.7/1.4 kg | |
Sensors | ||||
Temperature (±0.1°C) | Standard | Standard | Standard | |
Strain gauge pressure sensor (±0.1%) | Standard | Standard | Standard | |
High precision strain gauge (±0.01%) | Optional | Optional | Optional | |
Inclinometer (tilt sensor) Range ±90°, accuracy: ±1° (vertical orientation) |
Standard | Standard | Standard | |
Sound velocity sensor ±0.02 m/s accuracy under calibration conditions |
Standard | Standard | Standard |
Frequently asked questions
STP files
Datasheets
Overview
iRelease has been made obsolete. If you’re interested in the capabilities, we suggest looking at our Deck Topside
iRelease is a rugged, handheld unit that’s used as part of a Lightweight Command Unit (LCU) setup on the back deck to test, load and release our legacy range of ORT and DORT acoustic release transponders.
At a glance
- Use it to test and control legacy ORT and DORT acoustic releases
- Compatible with legacy LCU dunking systems (replaces obsolete Psion unit)
- Handheld design, battery powered, rechargeable
- Splash-proof and rugged; designed for the back deck
- Easy-to-use five-button interface
Specifications table
Feature | Type 8315 | |
---|---|---|
Case | Rugged polypropylene copolymer case with styrenic over mould shock protection | |
Keypad | Sealed 5 key navigation pad | |
Display | 320 x 240 sunlight readable LED display | |
Connections | USB | Splash-proof mini-USB Type B |
Serial | 9-way D-type (male) | |
Charging | USB to PC or USB to wall adaptor | |
Internal flash memory | 1 GB | |
Battery | Li-ion 3.7 V 1,300 mAh (typical) | |
Battery life | Normal (screen on) | >5 hours (screen automatically turns off after a selectable period) |
Idle (screen off) | >12 hours (press a key or ‘shake to wake’ to turn screen back on) | |
Off | >3 months (press a key to wake) | |
Off for shipping | >1 year (requires USB connection to wake-up) | |
Operating temperature | -10 to 55°C | |
Storage temperature | -10 to 55°C | |
Dimensions (length x width x depth) | 194 x 84 x 40 mm | |
weight | 0.8 kg |
Datasheets
Manuals and quick start guides
Combined excellence
Overview
Equinox is a true example of how Covelya Group technologies combine to provide ground-breaking products. Designed around the Solstice MAS from Wavefront Systems, it is commercialised by Sonardyne and features our state-of-the-art SPRINT INS and Mini-Ranger 2 USBL for state-of-the-art navigation and positioning.
The Sonardyne and Wavefront Systems payloads are all mounted on EIVA’s renowned ScanFish 3D, a steerable remotely operated towed vehicle (ROTV). EIVA’s NaviSuite Kuda user interface is used to plan, autopilot and display the gathered data in real-time.
Producing stunningly accurate pictures, it’s ideal for vessels of opportunity or unmanned surface vessels delivering hydrographic, archaeological, search, salvage, unexploded ordnance, and mine countermeasure missions.
At a glance
- Mission ready; designed to support search, classify and map (SCM) and hydrographic operations
- Survey more ground in a single pass; effective area coverage rate (ACR) of up to 1.6 km2/hr
- Along track resolution of 0.15°; best in class delivering maximum detection rates
- Co-located side-scan image and bathy improves your situational awareness
- Real-time motion compensation and positioning accuracies better than 1 m DRMS
- Automatically follows terrain and avoids obstacles
- Suitable for site survey and characterisation and high tempo MCM missions
Why Equinox is perfect for your operations
The ScanFish 3D is a trusted ROTV and, thanks to its inherent stability, the ideal platform to operate Solstice from. At a total weight of 220 kg in air, Equinox can be easily mobilised.
Unlike towed Synthetic Aperture Sonar (SAS) systems, Equinox offers you an affordable, lower-logistics alternative still capable of providing high area coverage rates. By combining leading navigation and positioning from Mini-Ranger 2 USBL and SPRINT INS, imaging data is geo-referenced with an accuracy that’s unrivalled for these types of applications at this price.
Planning a mission is easy. Using NaviSuite Kuda software, you can define your sailing route and run-lines by simply selecting the area you would like to cover. During the mission, NaviSuite Kuda continuously updates the vessel and ScanFish 3D position in real-time.
Equinox also provides real-time geo-rectified waterfall, mosaics and DTM maps and the user interface tools that enable an operator to mark and process objects, including automatic target recognition using AI.
That’s not all; ScanFish 3D can carry heavier payloads and there is room in the fibre cable to include additional payload sensors such as gap fillers. Equinox users can count on improved probability of detection and decreased probability of false alarms, improving the efficiency of your mine countermeasures, archaeological, search and salvage missions.
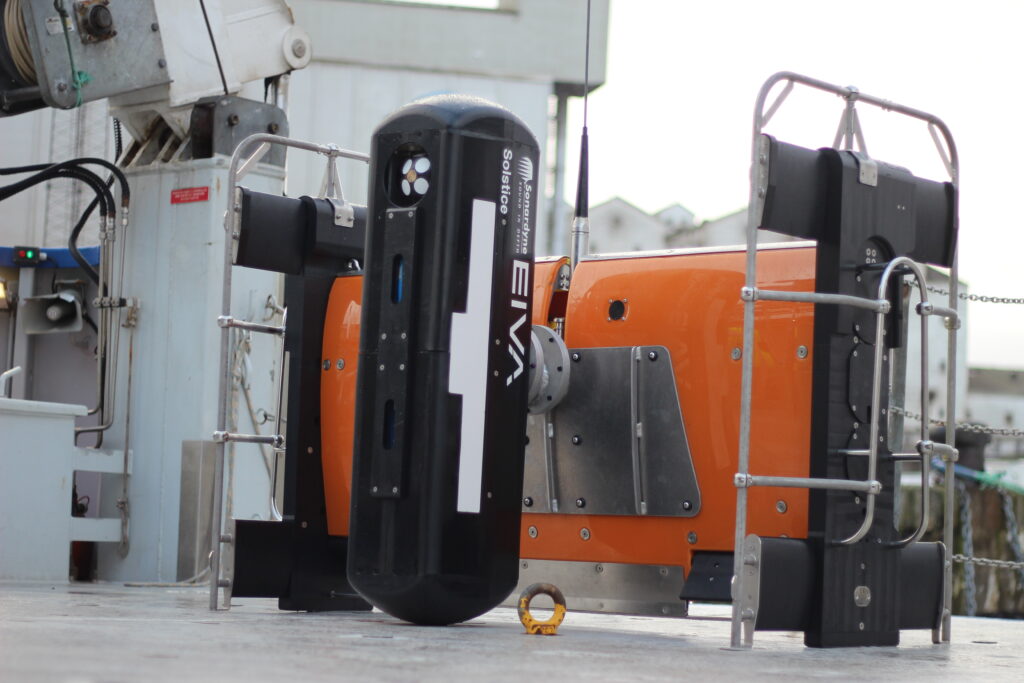
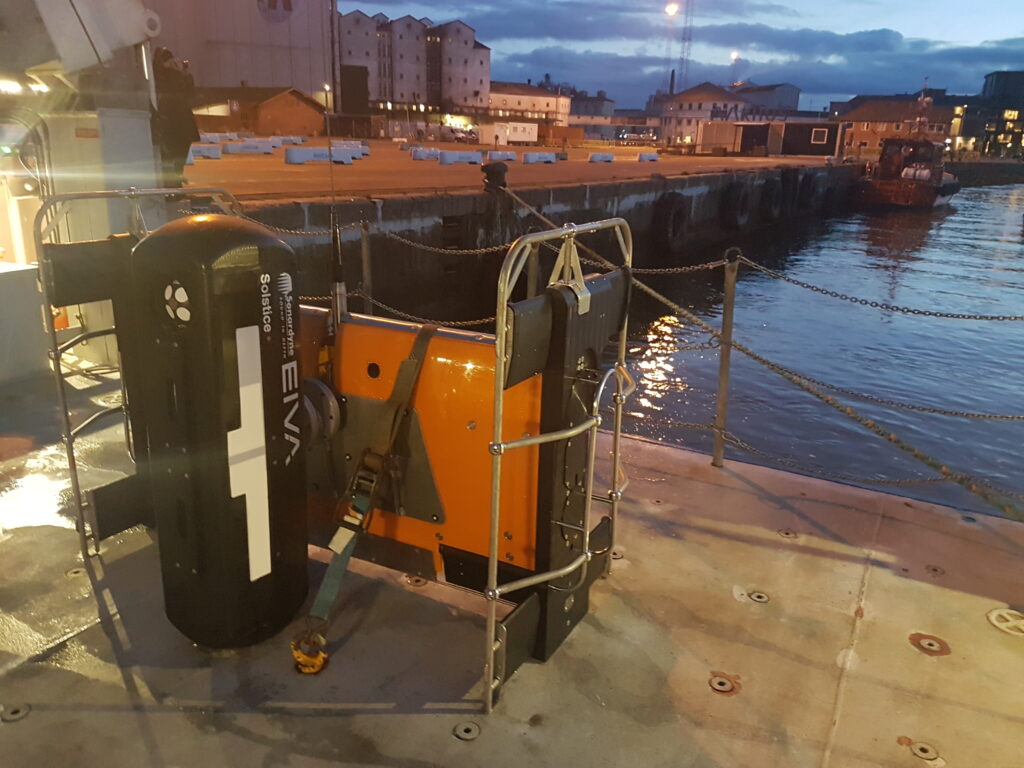
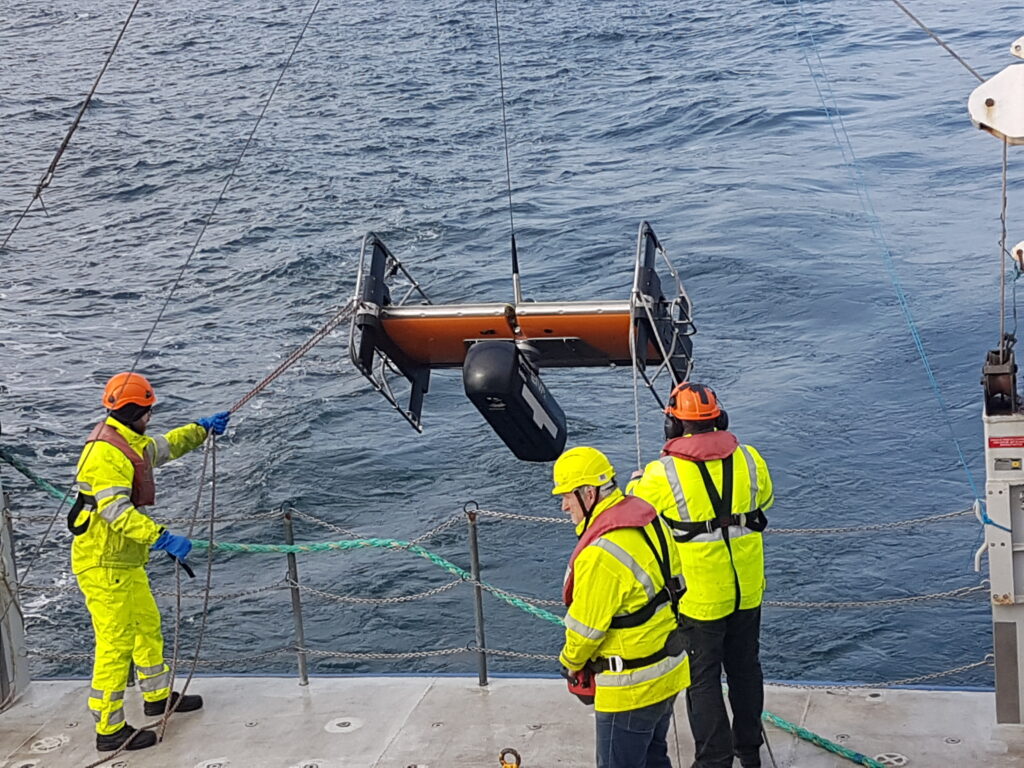
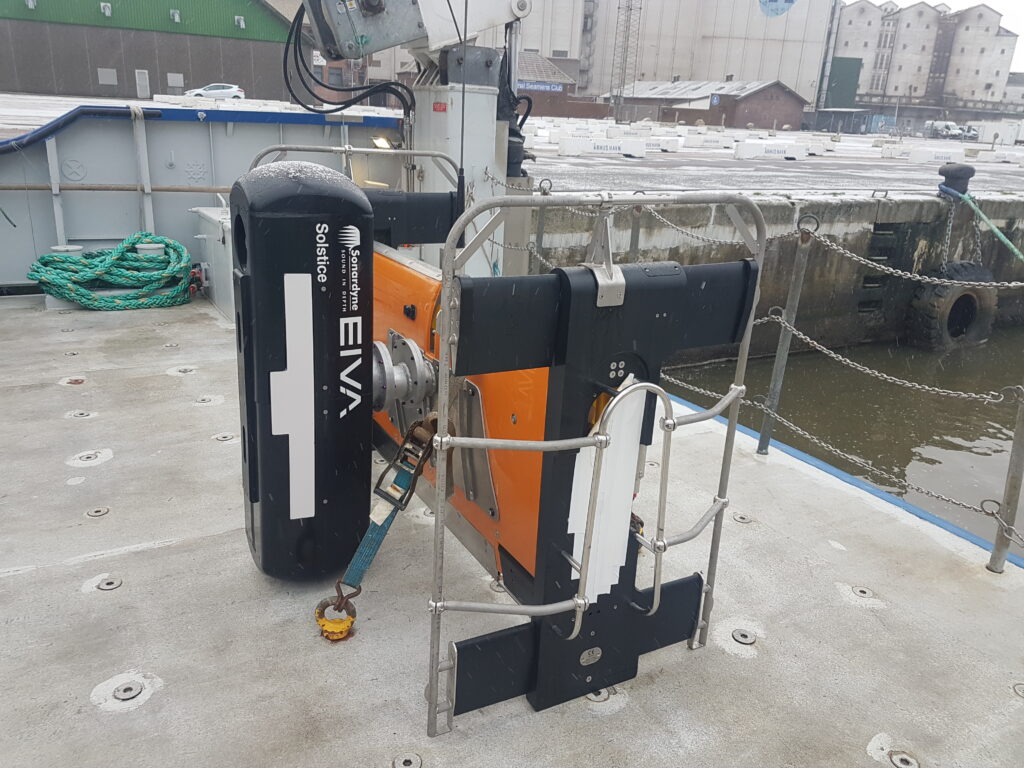
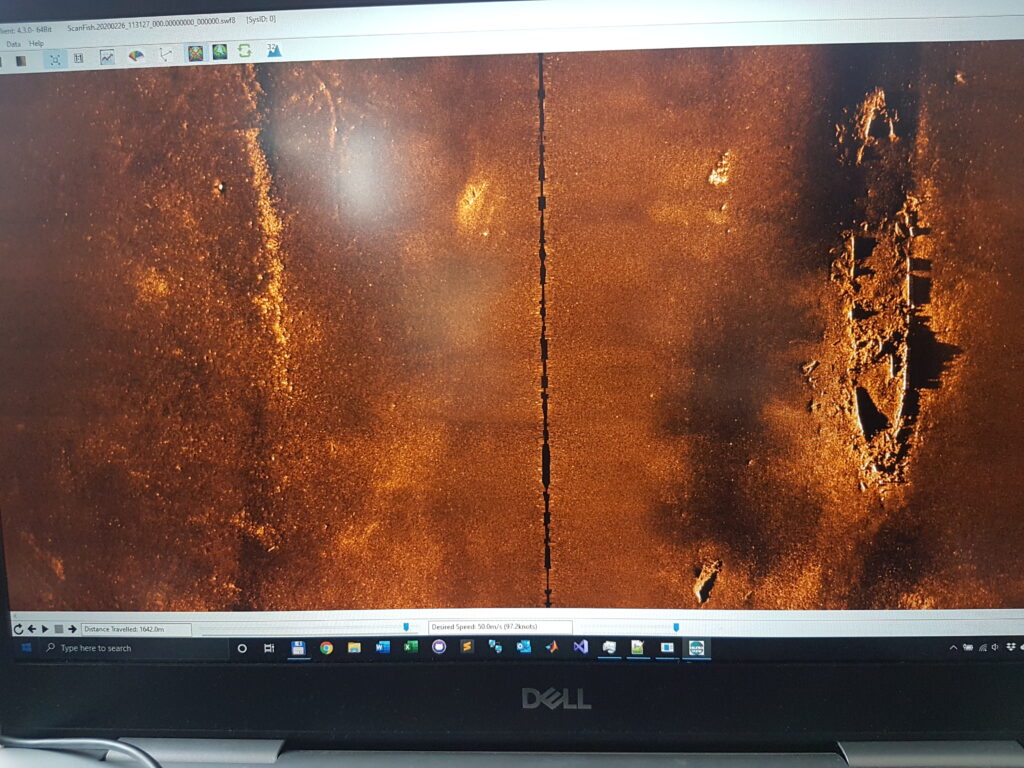
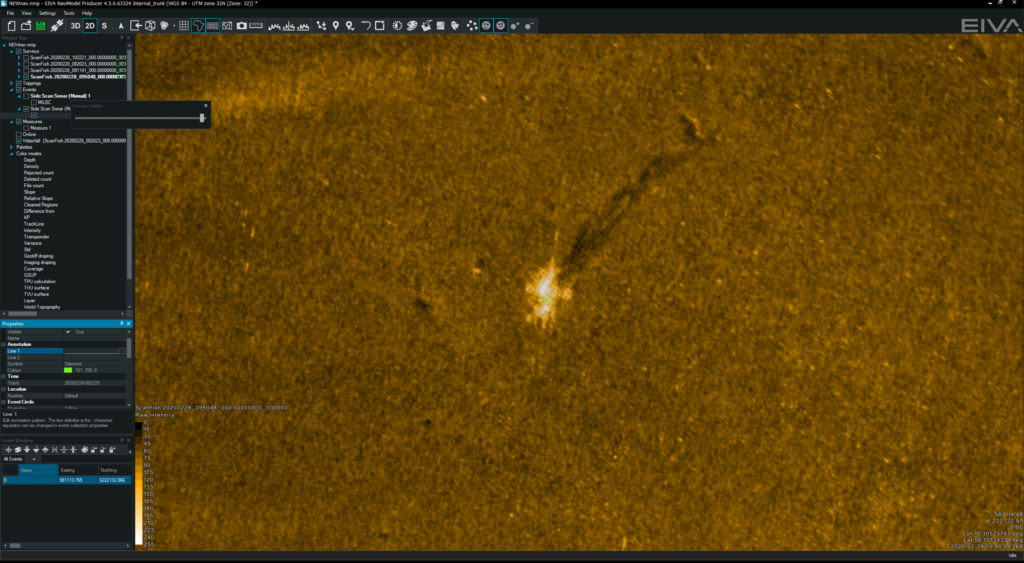
Equinox case studies
General
• All-in-one, rapidly mobilised solution for MCM, SCM and hydrography
• High stability platform with automatic terrain following
• NaviSuite Kuda software reduces planning times and improves processing times
• Everything supplied, including winch and 1Gbps cable
Performance
• Depth rated to 300 m
• Across track resolution 37.5 mm
• Along-track resolution 0.15°
• Geo-rectified waterfall display
• Image resolution 30 mm x 30 mm
• Co-located 200m swath side-scan and bathy
• Real-time CAD/CAC option
Design (SCANFISH)
• 1210 mm x 1858 mm x 1049 mm, 220 kg in air (73 kg in water)
• Survey speeds 3 to 6 knots
• Pitch and roll stabilised
• Automatic altitude following
Ownership
• What’s in the box: ScanFish 3D, NaviSuite Kuda software, cable and winch, Solstice MAS, Mini-Ranger 2 USBL, WSM 6+, SPRINT 500 INS, DVL
• Warranty: 1 year return to Sonardyne/EIVA service centre
• ITAR Controlled: No
• UK Export License: TBD
Datasheets
Capture every feature and every detail in ultra-high resolution.
Key benefits
- Mission ready; designed to support search, classify and map (SCM) and hydrographic operations
- Small and compact arrays; optimised for low-logistic AUVs and towed bodies
- Survey more ground in a single pass; 200 m-wide swath ensures high coverage rates
- Along track resolution of 0.15°; best in class delivering maximum detection rates
- Collocated side scan image and bathy improves your situational awareness
- Consumes only 18 W power: budget friendly and increases your AUV’s endurance
- Depth rated to 300 or 600 m
Solstice offers enhanced underwater detection capabilities for various missions, including mine countermeasures, archaeological, search, and salvage operations. The system provides high-performance coverage with large 200m swaths on each side, enabling efficient site characterisation without sacrificing detail. Its class-leading imagery allows you to make confident classification decisions more quickly, with the added versatility of deployment on both autonomous underwater vehicles (AUVs) and towfish platforms. By improving probability of detection and decreasing false alarms, Solstice significantly increases the overall efficiency and reliability of underwater exploration and survey missions. It is suitable for:
- Autonomous underwater vehicles (AUV)
- Site survey and characterisation
- Mine countermeasures (MCM)
- Remotely operated vehicles (ROV)
- Delivering pixel perfect imaging
Exceptional high-contrast seafloor imagery across diverse water depths
How it works
Solstice, designed by Wavefront Systems and commercialised by Sonardyne, is a world-leading side scan sonar for autonomous underwater vehicles (AUVs) and towed bodies. Its advanced technology delivers exceptional seafloor imagery through multiple aperture arrays with 32 multibeam elements, enabling superior signal-to-noise ratio performance and stunning imagery at extended ranges. The sonar’s unique back-projection beam-forming technique ensures focused imaging for every pixel, eliminating distortions caused by platform motion and guaranteeing 100% ground coverage across diverse water depths.
Designed for a wide range of marine missions including hydrographic, archaeological, search, salvage, and mine countermeasure operations, Solstice stands out through its innovative features. Its real-time array calibration dynamically recalibrates hydrophone elements multiple times per second, compensating for dynamic strains and maintaining linear element alignment. The system produces high-contrast imagery in environments ranging from 600-metre depths to very shallow littoral waters, utilising a specialised array technology that provides wide swath coverage with exceptional shadow contrast.
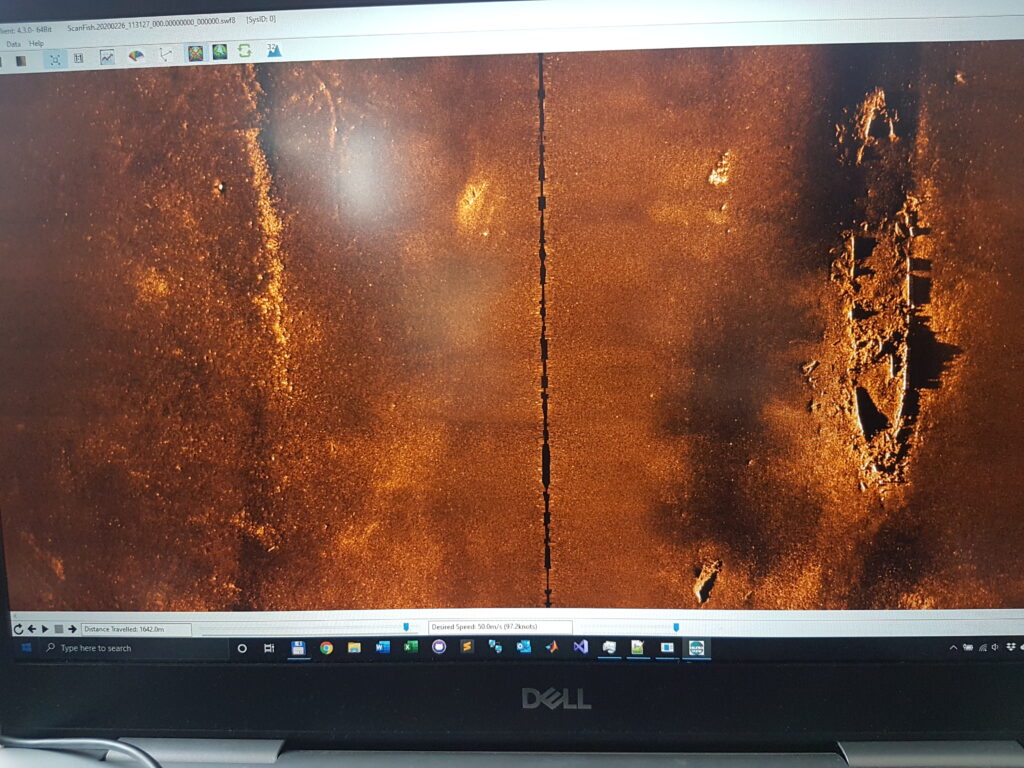
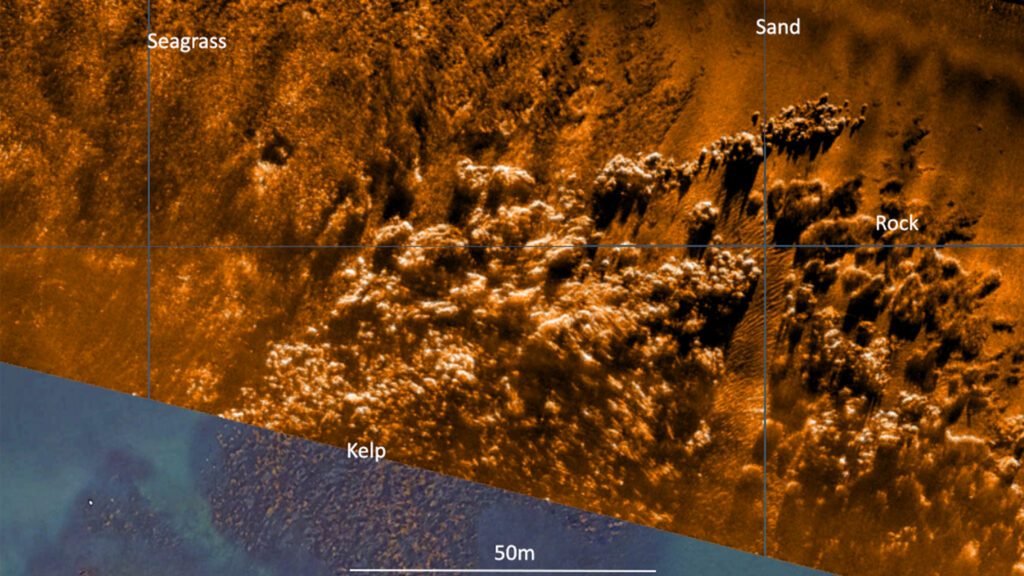
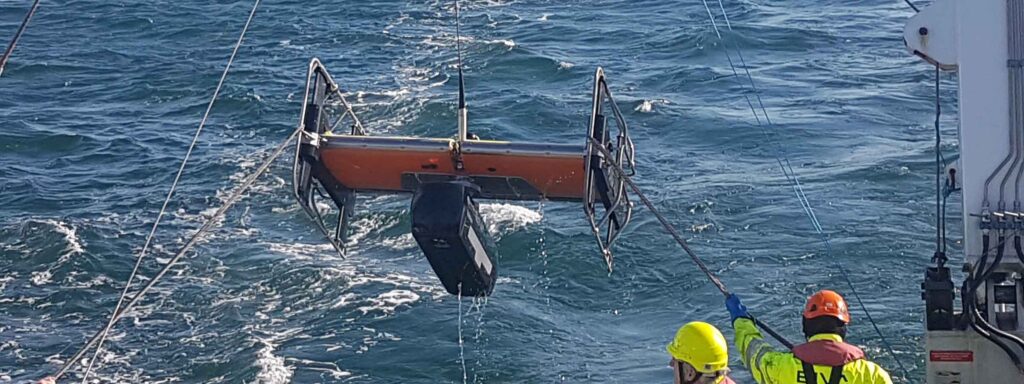
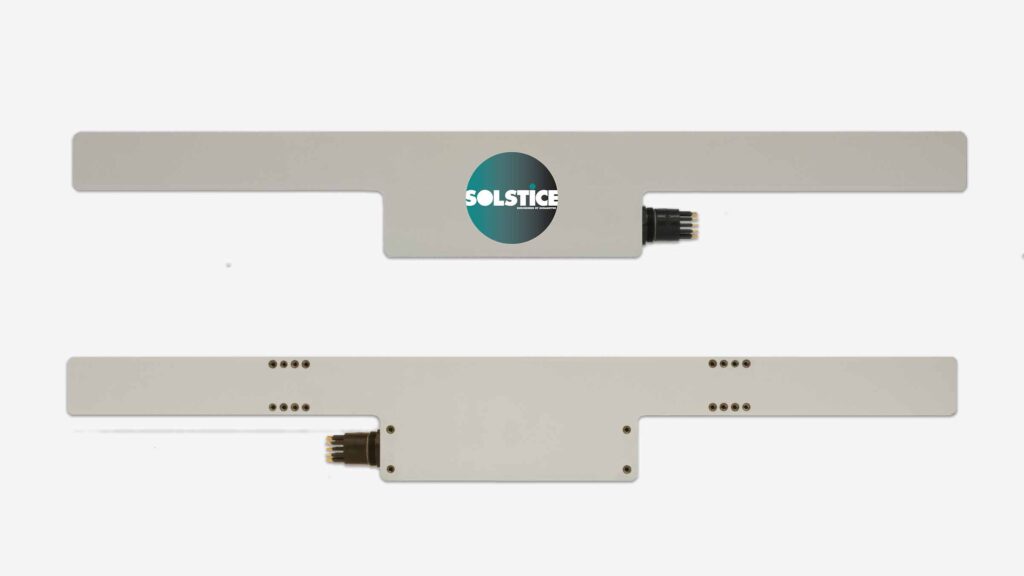
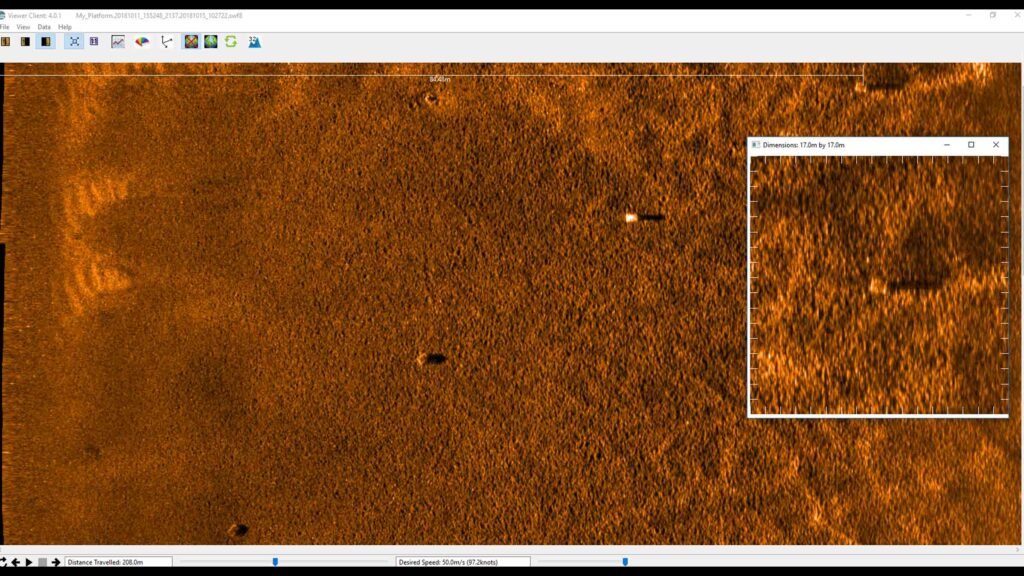
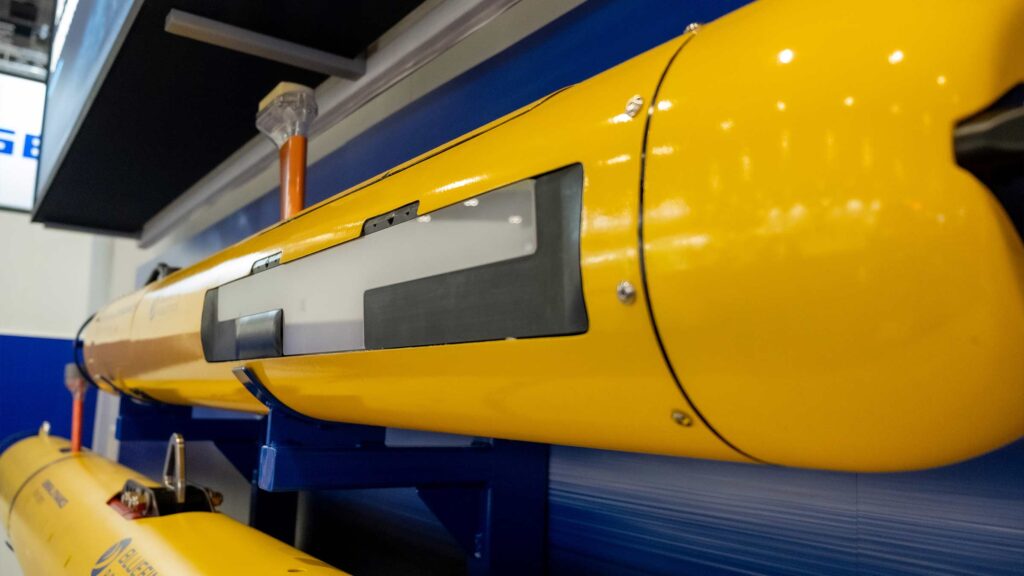
Solstice case studies
Using a hammer to crack a nut? Try using a USV instead
USVs are no longer new. They’ve been used in defence for some time now, for a range of tasks from surveillance to mine counter measures. USVs are being used to survey coastal and offshore waters in hydrographic surveys, for ocean science and in oil and gas
The challenge
Crewed vessels used in offshore construction projects are costly and can even hinder progress. But it doesn’t have to be that way. Other sectors that operate in the marine space are now finding new, smaller, smarter, cleaner tools. They’ve been using uncrewed surface vessels (USVs), so the big, crewed vessels can stick to the jobs they’re good at.
So why are we not using them heavily in offshore construction?
One reason may be because offshore construction was in fact an early adopter. But, at the time, there were only a handful of commercial USV operators whose vehicles were just too big for what was needed, making them unwieldy to deploy from an offshore vessel, defeating the point of the exercise.
Another may be the worry of the complexity involved in offshore construction. Creating complex structures on shore is one thing. Creating them under metres of salt water is entirely another.
Then there is the issue of communication and control over the construction process. Making sure each step is taken exactly as planned is fundamental to the overall success of a construction project.
The solution
USV technology has come a long way since their inception. They’ve been used in defence for some time now, for a range of tasks from surveillance to mine countermeasures. USVs are being used to survey coastal and offshore waters in hydrographic surveys, for ocean science and in oil and gas. They’re being used to go out and gather data, either as a platform for oceanographic instruments or by carrying acoustic communications systems to harvest data from sensors deployed at the seabed. You could think of them being like a remote-controlled Dunker.
USVs are now part of the toolbox across a number of sectors and the levels of sophistication and capability are increasing. Worries about lack of control, the complexity of operations or large clunky kit that isn’t up to the delicate tasks required in offshore construction are today unfounded.
In offshore renewables and oil and gas USVs are being used as part of site and seismic surveys, and then through field life, for inspection operations. They’re also being used for maintenance and repair, by acting as deployment platforms for autonomous underwater vehicles (AUVs), remotely operated vehicles (ROVs) and even aerial drones (UAVs).
The results
Today there’s a wide choice of USVs to choose from. From one-man portable USVs to full sized vessels, and on to fully electric coastal systems and hybrid long-range ocean-going vehicles that can operate for weeks on end. The range of commercial models has also grown. You can buy them outright or purchase a data service where you just order the end result – be it data or an inspection campaign.
USVs can now play a central role in construction operations. They can streamline operations and reduce risk for manned offshore construction teams. When deployed they reduce reliance on heavier, costlier tools and free-up crewed assets to be used on elements of a project where they’ll bring more value.
Rewriting the subsea survey rules
The underwater survey and construction sector is necessarily risk-averse. The potential negative impact from downtime, rectification events or environmental damage caused by changes to procedures and methods can be burdensome. The result is a preference for tried and true methods, techniques and equipment.
The challenge
In recent years, different combinations of subsea positioning technologies have been used in support of survey and construction projects. Whilst delivering an incremental improvement, they have also resulted in increased complexity in integration and operation. Separate inertial navigation systems (INS) and Long BaseLine (LBL) solutions require integration via online navigation software. Along with this, there is the added complication of the physical mounting, calibration and interfacing of INS and Doppler velocity logs (DVL) on remotely operated vehicles (ROVs).
The increased complexity adds cost in training and support, as well as increasing risk through having to control many separate parts from different vendors.
There is clearly a need to be smarter and more efficient. Reducing vessel days increases safety and lessens our environmental footprint. There is no need to lose the accuracy or reliability of subsea positioning or increase the complexity of operations either. If both the number of Compatts needed for an LBL pipeline installation array and calibration routine could be reduced, days – not just hours – of vessel time would also be lowered as would the entire complexity of such projects.
The solution
i-Tech 7 adopted our Fusion 2 all-in-one software platform for their INS and LBL operations.
This allowed them to take advantage of the Fusion 2’s real-time simultaneous localisation and mapping (SLAM) capability. Choosing to operate a sparse LBL can deliver a reduction of Compatts. However, if the sparse array cannot be calibrated using traditional LBL baseline calibration, the benefit may be lost. Extra time for performing additional ‘box-ins’ or collecting data to perform post processed SLAM positioning of the Compatts becomes necessary.
This isn’t the case with real-time SLAM. The number of Compatt transponders used to create the ‘sparse’ LBL array is reduced and the calibration of those Compatts is managed by flying the ROV through the array and acquiring the necessary observables to SLAM the array. With careful planning, this real-time SLAM process can be done during other ROV survey operations, such as pre-lay surveys. This removes the entire baseline calibration work flow from the project schedule.
Co-locating our SPRINT INS with a separate DVL onto i-Tech 7’s ROVs was the first step in reducing the complexity of these operations. Using SPRINT enabled the optimisation of sparse LBL operations, reducing the number of Compatts required for an LBL array by 50-66%, with the post-processing SLAM calibrations being managed by us.
The SLAM calibration technique was run alongside arrays with full LBL sections and sparse LBL arrays which were SLAM calibrated. When results were compared they showed centimetric agreement, proving real-time SLAM gives near traditional LBL levels of precision and accuracy.
All the experience and knowledge gained since i-Tech 7’s first use of our SPRINT INS in 2012 has enabled us to build SLAM calibration routines directly into Fusion 2. That step has taken the simplification to a new level. Real-time SLAM operations in i-Tech 7’s 2019 project have far more efficient trajectories than previous operations.
The results
Between August and November 2019, a minimum of 11 vessel days were saved across five separate i-Tech 7 deep water (1,000-1,500 m) projects in the US Gulf of Mexico. Thanks to Fusion 2’s real-time SLAM capability, operators were able to access first oil faster.
Having already reduced the number of Compatts needed for an array – by reducing how much time is spent deploying them and calibrating them – the time allocated on project schedules for the lengthy box-in routines required in a traditional array can also be reduced, if not completely negated.
In fact, following a pre-lay survey, an offshore manager asked one of i-Tech 7’s offshore surveyors how long the array calibration would take before pipelay operations could start. The answer? It had already been done.
i-Tech 7 and Subsea 7 have proved the simplification of pipeline installation projects can be smarter, more efficient, quicker and safer. What’s more, they help lessen the overall environmental footprint of major subsea installation projects. This can all be done without losing positioning accuracy or reliability.
Shallow water site investigation for offshore wind
From the topside to the underwater instruments, our goal is to make offshore operations easier and less time-consuming, but also highly accurate. As PDE Offshore discovered, with Mini-Ranger 2, our 6G hardware and our Wideband 2 digital acoustic technology onboard, safe and efficient shallow-water site investigation operations, from tracking towfish to positioning seabed geotechnical equipment, are assured.
The challenge
In a short period of time, Taiwan has quickly become a leader in the global build-out of offshore wind. Starting from scratch in 2018, the country has been quick to ramp up its offshore wind capability. Taiwanese company PDE Offshore, based in New Taipei City, was quick to get involved in this new industry and came to us for a USBL system to underpin its offshore wind geotechnical site investigation service offering.
Specifically, it was looking for a system to support geotechnical site and soil investigation works for a new offshore wind farm in the shallow water Taiwan Strait. This involves deploying geotechnical drilling equipment on the seabed at each planned turbine site in just 20 – 60 m water depth. The frame holding the equipment has to be positioned accurately to ensure it’s aligned with the drill string deployed from PDE Offshore’s geotechnical survey vessel.
The solution
PDE Offshore chose a combination of our Mini-Ranger 2 USBL system and our Wideband Sub-Mini 6+ (WSM 6+) transponder/responders to track and position their drilling frame on the seabed. Mini-Ranger 2 is built around the same market-leading 6G hardware and Wideband 2 digital acoustic technology you’ll find in our entire family of USBL systems – even the software is the same.
Critically, it’s designed to easily handle just the kind of shallow waters PDE Offshore had to work in on the project in the Taiwan Strait. At the heart of Mini-Ranger 2 is our HPT 3000, a highly capable surface-deployed USBL transceiver that’s optimised for high performance in shallow water, as well as high elevation and long lay back operating scenarios and data telemetry.
It was a simple choice for PDE Offshore, not least as their onboard surveyor was already familiar with Mini-Ranger 2. What’s more, it’s also a great option for smaller vessels and even unmanned surface vessels (USVs).
A wide range of Sonardyne 6G transponders can be used with Mini-Ranger 2, allowing you to select the most appropriate took for each task. For its operations in the Taiwan Strait, PDE Offshore chose our Wideband Sub-Mini 6+ (WSM 6+) transponder/responders. Designed for positioning ROVs, towfish and other mobile targets in water depths up to 4,000 m, WSM 6+ incorporates our Wideband signal technology, so it offers superior ranging accuracy and fast USBL position updates as well as full two-way Wideband support – interrogation and reply signals.
Targeting
0
GW
by 2025
0
m/s
average wind speed
Average water depth
0
m
for each turbine
The results
PDE Offshore spent summer 2020 performing site investigation works from the MV Geo Energy in the Taiwan Strait. Our WSM 6+s were mounted on the seabed frame and tracked using the Mini-Ranger 2’s HPT 3000, which was deployed on an over-the-side deployment pole from the MV Geo Energy.
Huang Hsin-chih, president of PDE Offshore, says, “Where we work in the Taiwan Strait, water depth is from 20 to 60 meters; in the future, there might be a chance to work in offshore wind farm with water depth from 50 to 200 meters, so whilst we do need a very precise USBL, we don’t need one that’s full ocean depth capable. Through renting, we became familiar with Mini-Ranger 2 and the benefits it brought to our busy geotechnical operations. So it was a simple choice to decide to go ahead and purchase one of our own and it has proven fully capable for our needs on this and future offshore wind projects.”
Facing the challenge of speeding up consent in offshore renewable energy
The drive for cleaner, greener energy set against financial constraints in a challenging world market could mean testing times ahead for offshore renewable energy (ORE).
In order to meet pressing timescales, cost saving criteria and governmental targets for energy production, the industry needs shorter consenting periods for offshore wind projects but also better characterisation data. Better data would suggest the need for a longer, more costly, consenting period. So how can this challenge be met?
At Sonardyne, we believe our Origin® acoustic Doppler current profilers (ADCPs) may offer at least part of the solution. ADCPs use acoustics to measure the water column to determine currents and many can also measure wave motion and turbulence. They can provide metocean data for decision making on where to place floating turbines to ensure moorings are not stressed, determining where scour may occur that will damage cables or structures, array cable selection, route planning and cable’s depth of burial predictions etc.
Obtaining high quality, accurate, current and wave data has always been a challenge in the marine environment. Which is far from ideal when there’s a need for more timely, precise data. Meanwhile, traditional ADCP technology does not have resolution high enough to distinguish fine-scale turbulence. The correct measurement of turbulence is a key factor in ensuring that any planning at the consenting stage is based on accurate data.
With accurate data at the consenting stage, developers can reduce options and decide on the exact foundation solution, maximum turbine size etc. They can then plan with certainty and model simple environmental impact assessments for presentation to the consenting authorities.
Enter Origin…
Our Origin 600 and 65 ADCPs signify a sea change in ocean floor ADCP technology and are the most advanced ADCP’s presently on the market.
Alongside industry standard PD0, new and exclusive A-gram and B-gram proprietary data formats offer up to ten times greater spatial resolution and provide superior quality data for more informed decision making.
The inbuilt acoustic modem provides the ability to; check operating status, test data quality and change schedules mid-mission. It also provides remote access to the customisable Edge data processing applications on Origin. This means that while the device is deployed, it can be programmed to output concise, relevant information, rather than bulky raw data that would normally be processed once the device is recovered from the water. All without the cost and risk associated with interfacing an external modem or running a cabled ADCP operation.
Realising the potential
Taking this a step further and combining Origin’s data and communication capabilities with autonomous data collection via an uncrewed surface vehicle (USV) or surface buoy potentially offers many advantages.
Operators can make informed decisions faster as more frequent, concise data samples can be collected throughout the deployment, rather than waiting for the ADCP’s retrieval. Data can be collected at intervals via a USV passing overhead or transmitted to Cloud storage via a LiDAR buoy.
Reduction of carbon emissions during missions can also be achieved. USV data harvesting and an ADCP battery life of over three months are just two in which the need for a carbon-heavy crewed vessel would be reduced. The associated costs and HSE exposure hours would be reduced too.
Origin’s ability to provide high fidelity data, often in near real-time – depending on the harvesting method – offers the potential to meet the data requirements within a shorter timeframe.
Concept testing
A proof-of-concept trial was conducted in Plymouth Sound in April 2023, with the aim of establishing the range and quality of data transmittable from the seabed via Origin and a USV to the shore.
An Origin 600 was mounted on a tripod frame and integrated with a third-party turbidity sensor before being deployed at a depth of approximately 8m in Cawsand Bay. For the purposes of the test, Origin was configured, via the Edge processing app, to average out its readings alongside those from the turbidity sensor for the previous 20 minutes and to send the results acoustically every five minutes. In a real-world scenario, this update rate would usually be configured less frequently.
Our USV ‘Decibel’ was fitted with; an Avtrak6 Nano to receive the data, a deck topside box running the Origin topside software and a control unit payload supplied by the Metocean, Science and Technology team at RPS, to push the data to a Cloud storage via Iridium. For this trial, the team at RPS took LiDAR technology and integrated it into a buoy with power, data storage and satellite communication capabilities. Applying deep expertise of offshore measurement, the design and development process was focussed on creating a reliable design to maximise data accuracy and return, while making the process of information gathering easier and more cost-effective.
Decibel then hovered on the surface above Origin and performed a slow drift off test to establish an understanding of communication coverage/range limits. A lateral excursion of 87 metres was achieved, which equates to a very small elevation angle of almost five degrees – important for shallow water buoys in areas with strong tidal patterns. Once the test was complete, data that had been stored by Origin was compared to the data it had transmitted to the Cloud, via the acoustic modem, Nano and the RPS control unit.
As expected, there was no significant difference between the two data sets other than Origin storing more data than was transmitted to the cloud. This was due to the USV drifting off location to test its range. In a real-life situation, a USV or buoy would maintain a set position and link to the Cloud so more data would be transmitted.
The trial proved proof of concept getting data into the Cloud. Further work is now underway into how we can further integrate Origin with floating LiDAR buoys.
Edge’s future value to offshore wind
As discussed, Edge computing enables users to process data directly on the Origin 600 and send only the critical information over the acoustic modem to the topside. This approach has numerous benefits, including early data insights, more efficient data management at the front end and a sense of relief that the unit is performing as expected (or reducing PDA: post-deployment anxiety!).
Implementing Edge computing via an Origin ADCP can help revolutionise the way in-situ ORE monitoring is conducted in the future. Processing the data at source before transmission reduces data overload by focusing solely on critical information. When combined with AI learning, it will reduce data swamping, lead to quicker but better decision-making and, hopefully, help get turbines in the ground sooner. All while advancing the move towards cleaner, greener, autonomous ORE operations.
Delivering subsea synergy in ORE inspections
There are numerous challenges associated with offshore wind visual inspections, including currents, turbidity, time and cost. Sonardyne, EIVA and Voyis, all part of the Covelya Group, are working together to bring a complete imaging, navigation and autonomy solution to overcome these obstacles and enhance the inspection data product.
With almost a century of combined subsea expertise between them, the companies are ideally placed to offer a solution to the offshore renewable energy (ORE) market that is even greater than the sum of its parts.
Combining great experience to create even greater things.
Bringing together their combined expertise at a technology accelerator event at the ORE Catapult Subsea and Marine testing facility in Blyth, Northumberland, UK, Sonardyne, EIVA and Voyis were able to demonstrate the potential of their ORE inspection solution to industry users, vehicle manufacturers and end clients recently.
Each company brought its own existing technologies which were integrated, on remotely operated vehicles (ROVs) provided by Atlantas Marine , to demonstrate an even more effective solution for underwater surveying.
During the demonstration, NaviSuite VSLAM leveraged the Discovery Stereo system to enable augmented piloting through real-time 3D point cloud images for quality control, while NaviSuite Mobula provided an end-to-end software solution for acquisition, processing and delivery of data.
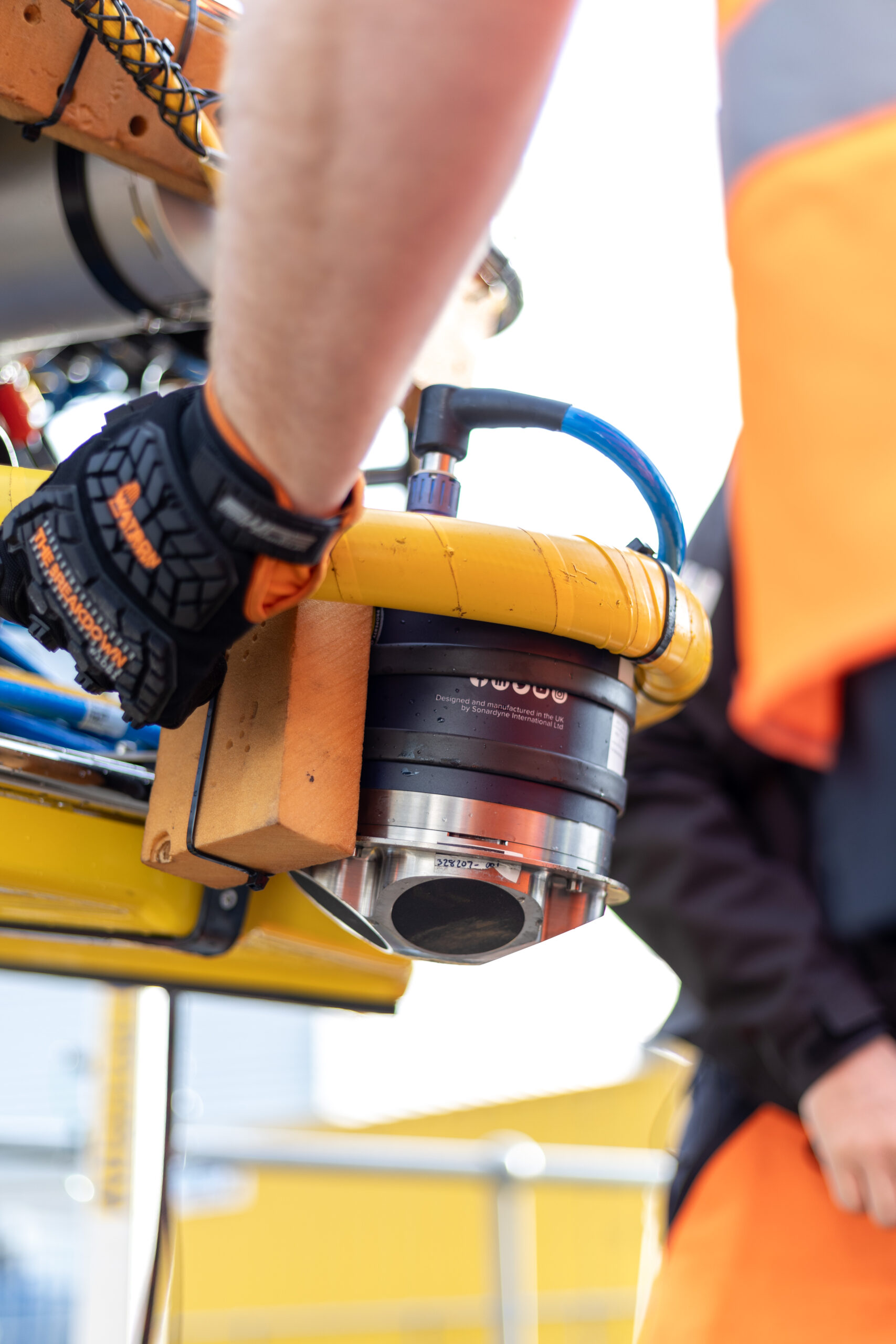
Sonardyne SPRINT-Nav Mini
Sonardyne’s SPRINT-Nav Mini provides robust, reliable, navigation for piloting and surveying. It is the world’s smallest hybrid acoustic-inertial navigation system and can be used as an all-in-one vessel and marine robot navigation instrument with performance beyond its size. The SPRINT-Nav Mini eliminates the need for separate sensors, such as AHRS, DVL, INS, and depth sensors. This results in no further calibration requirements, fewer cables and connectors to manage and it is more cost-effective than the four sensors it replaces.
It will work in the most challenging environments and remains unaffected by steel structures such as wind turbine foundations and provides a continuous stream of positions, orientation, velocities, depth and altitude at up to 200 updates per second.
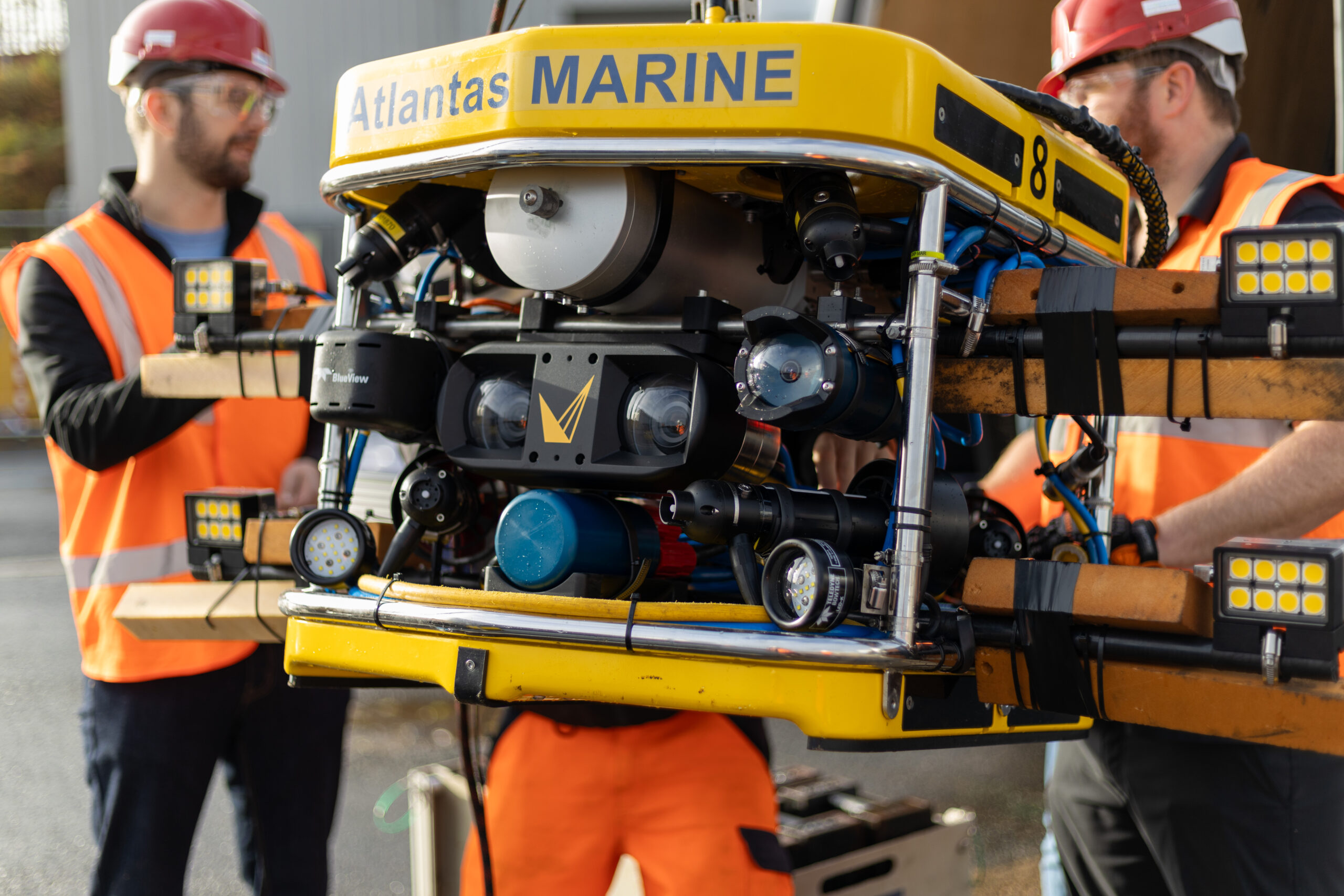
Voyis Discovery Stereo camera
Voyis’ Discovery Stereo camera provides a powerful platform for a vehicle’s subsea vision needs, delivering stills images, video, IMU data and 3D data with a data-centric DDS architecture. Through edge computing, it integrates with EIVA’s visual simultaneous localisation and mapping (VSLAM) software technology to provide real-time 3D reconstruction, ensuring area coverage mapping and augmented piloting. Mounted on the front of the ROV, the Discovery Stereo provided 4K video stream and high-resolution images for both navigation and inspection throughout the demonstration.
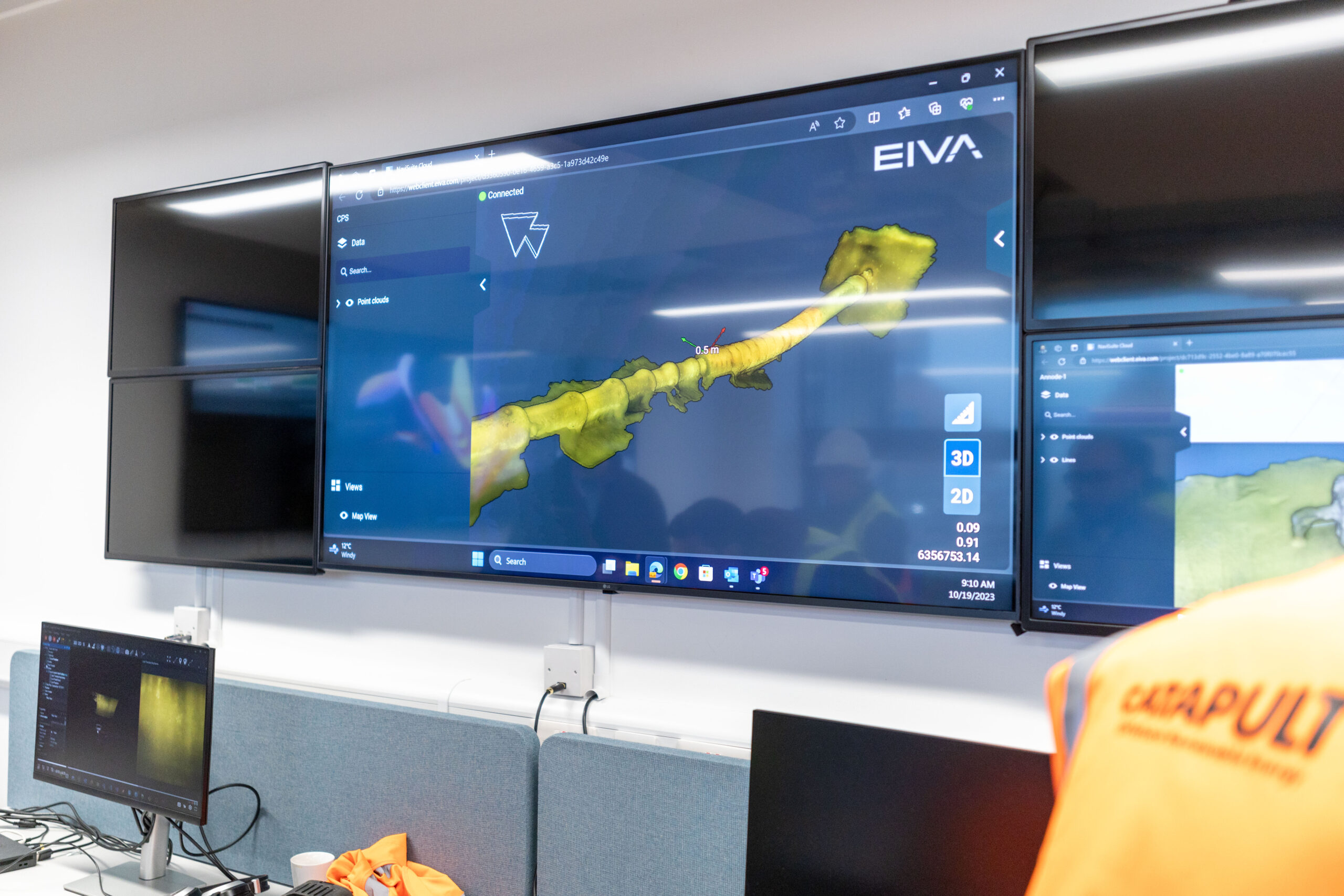
EIVA NaviSuite Mobula
EIVA’s NaviSuite Mobula software package provides a complete topside software solution for the ROV, enabling efficient acquisition of data with the Voyis Discovery Stereo and Sonardyne SPRINT-Nav Mini. This software offers unique capabilities for automating remotely operated subsea inspection and surveying operations – using tools for a wide variety of tasks, leveraging the software toolbox of NaviSuite.
Demonstrating the difference.
The technology accelerator event at Catapult provided the perfect opportunity to showcase the possibilities in developing this combined subsea inspection solution. The test dock contains a turbine foundation and various other structures, perfect for subsea navigational and photogrammetry demonstrations.
The ROV was fitted with a SPRINT-Nav Mini at the rear, Discovery Stereo camera at the front and utilised the NaviSuite Mobula and VSLAM software packages to control the ROV movements, represent the operation in a real-time 3D visualisation and pilot view, along with monitoring coverage and inspection data quality.
Once the ROV was launched, focus shifted to the control room where the assembled delegates watched the live 4K video stream from the Discovery Stereo camera as the vehicle navigated the dock.
Whilst its primary navigation and positioning was provided by the SPRINT-Nav Mini, as the ROV navigated and surveyed the subsea structures the Discovery Stereo camera and NaviSuite software combined their capabilities to provide millimetric positioning precision and 3D point cloud detail which was fed back to the control room. A video from the demonstration, giving more information about the technology, can be viewed here.
In real-life operations, these actionable insights could then be used to make immediate decisions about state of the asset, the quality of the data and subsequent actions required from the ROV. Having the capability to make real-time operational decisions greatly reduces the risk of collecting inaccurate data and helps to avoid the associated wasted time and cost.
For Sonardyne, EIVA, Voyis and the wider Covelya Group, this demonstration of synergetic working is just the beginning of our ‘Better Together’ approach. The opportunities for delivering smarter, faster, cleaner and more effective subsea technology solutions from within the group of companies are almost endless.
Pinpointing Precision: Arctia chooses Sonardyne system for subsea surveys
When Finnish state-owned hydrographic services and icebreaking company Arctia need to accurately and reliably position their subsea survey equipment there is only one logical solution.
Arctia provide a wide range of services for Finland’s maritime industry including icebreaking, hydraulic engineering, planning and permit services, fairway maintenance and survey services, hydrographic services and research.
Their services all rely on precise subsea navigation and tracking, especially those using towed survey equipment. This is where Sonardyne come in, Arctia have chosen their Mini-Ranger 2 Ultra Short BaseLine (USBL) system with WSM 6+ transponders for their marine survey services.
Many of their marine surveys are conducted around offshore wind farms where teams of internationally certified hydrographic surveyors and shallow water experts provide tailor-made survey, analysing and planning solutions to meet even the most demanding of customer needs.
Mini-Ranger 2 is one of Sonardyne’s most popular USBL systems, chosen for its small size, value and dependable performance in all underwater environments. It’s the perfect choice for fitting to small survey vessels, moored barges and uncrewed vessels.
For Arctia, it is the perfect partner for towed hydrographic survey equipment such as magnetometers and sidescan sonars used as part of their survey services. With depth ratings of up to 1000 metres and able to operate in temperatures as low as -5 degrees Celsius, it’s ideal for the Baltic Sea and offers the opportunity to upgrade to other versions for depths up to 4,000 metres should Arctia and their customers operate at greater depths in future.