Overview
Compatt 6 has been superseded by the Compatt 6+ transponder.
Compatt 6 is our Wideband 2 enabled transponder compatible with all 6G equipment and our latest LBL, INS and USBL systems, including Ranger 2 and Marksman.
At a glance
- Compatible with all 6G LBL, INS and USBL systems
- Wideband 2 enabled
- Versatile, flexible and cost-effective
- Over 3,600 different configurations available
- Choice of depth ratings to 7,000 m
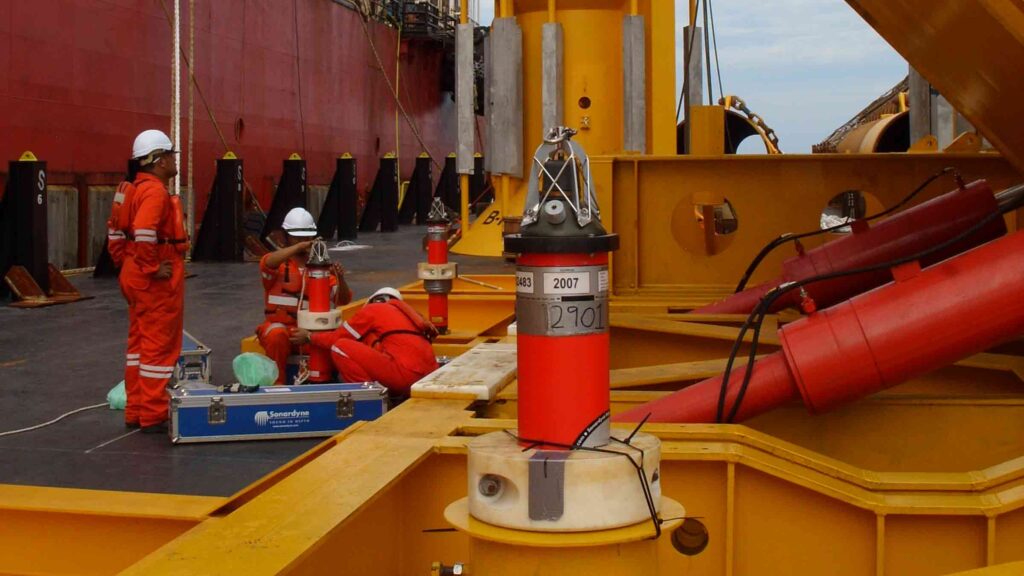
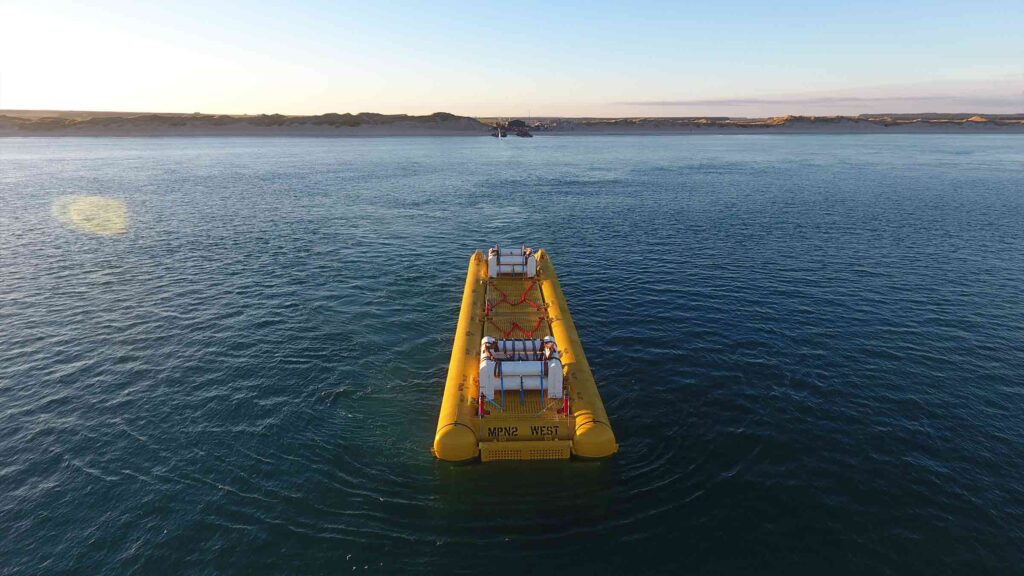
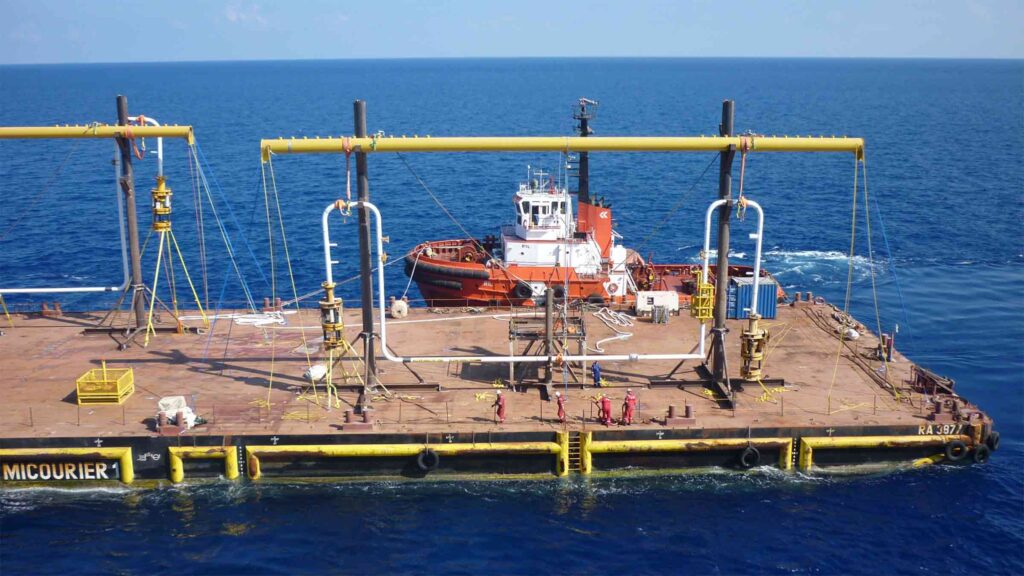
Specifications table
Feature | Type 8300-3111 | Type 8300-3113 | Type 8300-5213 | Type-8300-7216 | |
---|---|---|---|---|---|
Depth Rating | 3,000 m | 3,000 m | 5,000 m | 7,000 m | |
Operating Frequency | MF (20–34 kHz) | MF (20–34 kHz) | MF (20–34 kHz) | LMF (14-19 kHz) | |
Transducer Beam Shape | Omni-directional | Directional | Directional | Directional | |
Transmit Source Level (dB re 1 µPa @ 1 m) |
187–196 dB (4 levels) |
190–202 dB (4 levels) |
190–202 dB (4 levels) |
187–202 dB (4 levels) |
|
Tone Equivalent Energy (TEE) | 193–202 dB | 196–208 dB | 196–208 dB | 193–208 dB | |
Receive Sensitivity (dB re 1 µPa) | 90–120 dB (7 levels) |
80–120 dB (7 levels) |
80–120 dB (7 levels) |
80–120 dB (7 levels) |
|
Ranging Precision | Better than 15 mm | Better than 15 mm | Better than 15 mm | Better than 15 mm | |
Number of Unique Addresses Wideband 1 & 2 |
>500 | >500 | >500 | >500 | |
Battery Life (Listening) | Alkaline | 833 days | 833 days | 833 days | 833 days |
Lithium | 1,390 days | 1,390 days | 1,390 days | 1,390 days | |
External Power Supply | 24 V | 24 V | 24 V | 24 V | |
Safe Working Load (4:1) | 250 kg | 250 kg | 250 kg | 250 kg | |
Operating Temperature | -5 to 40°C | -5 to 40°C | -5 to 40°C | -5 to 40°C | |
Storage Temperature | -20 to 55°C | -20 to 55°C | -20 to 55°C | -20 to 55°C | |
Dimensions (Maximum) (Length x Dia) |
With Sensor Guard | 1,034 x 200 mm | 1,034 x 200 mm | 1,034 x 200 mm | 1,034 x 200 mm |
Without Sensor Guard | 1,034 x 178 mm | n/a | n/a | n/a | |
Weight in Air/Water | 23.8/11.8 kg | 27.0/14.0 kg | 29.0/15.0 kg | 33.3/18.8 kg | |
Endcap Sensors and Options | |||||
Temperature (±0.1°C) | Standard | Standard | Standard | Standard | |
Tilt Switch (±30-45°) | Standard | Standard | Standard | Standard | |
Strain Gauge Pressure Sensor (±0.1%) | Standard | Standard | Standard | Standard | |
High Precision Strain Gauge (±0.01%) Presens or Keller |
Optional | Optional | Optional | Optional | |
Paroscientific DigiQuartz Pressure Sensor 1,350 m, 2,000 m, 4,130 m, 6,800 m (±0.01%) |
Optional | Optional | Optional | Optional | |
Inclinometer (Tilt Sensor) Range ±90°, Accuracy: ±1° |
Standard | Standard | Standard | Standard | |
High Accuracy Inclinometer Range: ±90°, Accuracy: ±0.05° over 0 – ±15°; ±0.2° over 0 – ±45° |
Optional | Optional | Optional | Optional | |
Sound Velocity Sensor ±0.02 m/s Accuracy Under Calibration Conditions |
Optional | Optional | Optional | Optional | |
Release Mechanism | Standard | Standard | Standard | Standard | |
Power for External Sensors | Standard | Standard | Standard | Standard | |
Gyro Input | Standard | Standard | Standard | Standard |
Frequently asked questions
Compatt 6 and 6+ Deployment Tests
6G Terminal Lite Range Test
How can I deploy my Compatt 6+ using iWand?
I want to buy standard red Compatt 6, are they still available for sale?
Can Compatt 6+ be used in the same LBL array as standard Compatt 6?
What is the difference between Compatt 6 and Compatt 6+?
Can ROVNav 6+ be used with standard Compatt 6s?
How to replace a battery in Compatt 6 and 6+ family of transponders
STP files
Software and firmware
Software and control hardware
Manuals and quick start guides
Technical bulletin
Overview
ROVNav 6 has been superseded by ROVNav 6+
ROVNav 6 is a 6G Wideband 2 ranging LBL ROV Transceiver and telemetry transceiver specifically designed for installation on work class ROVs.
At a glance
- Use it with Fusion 6G
- Wideband 2 enabled
- High power, long range LBL transceiver
- 3,000, 5,000 or 7,000 m depth rated
- USBL mode for emergency ROV relocation
- Modem mode for harvesting data from Sonardyne sensors
Specifications table
Feature | 8310-3161 | 8310-5261 | 8310-7261 | |
---|---|---|---|---|
Depth rating | 3,000 m | 5,000 m | 7,000 m | |
Operating frequency | MF (20–34 kHz) | MF (20–34 kHz) | MF (20–34 kHz) | |
Transducer beam shape | Omni-directional | Omni-directional | Omni-directional | |
Transmit source level (dB re 1 µPa @ 1 m) | 187–196 dB (4 Levels) | 187–196 dB (4 Levels) | 187–196 dB (4 Levels) | |
Tone Equivalent Energy (TEE) | 193–202 dB | 193–202 dB | 193–202 dB | |
Receiver sensitivity (dB re 1 µPa) | 90–120 dB | 90–120 dB | 90–120 dB | |
Range precision | Better than 15 mm | Better than 15 mm | Better than 15 mm | |
Serial communications (software programmable) |
Primary port | RS232 or RS485 (half-duplex) | RS232 or RS485 (half-duplex) | RS232 or RS485 (half-duplex) |
Secondary port | RS232 or RS485 (half-duplex) or SYNC IN | RS232 or RS485 (half-duplex) or SYNC IN | RS232 or RS485 (half-duplex) or SYNC IN | |
Battery life Li-ion (listening) | 3 days | 3 days | 3 days | |
Operating voltage | 24 or 48 V dc (±10%) | 24 or 48 V dc (±10%) | 24 or 48 V dc (±10%) | |
External power | Active (listening) | <3 W typical (maximum 10 W when charging) | <3 W typical (maximum 10 W when charging) | <3 W typical (maximum 10 W when charging) |
Peak (during transmission) | <80 W | <80 W | <80 W | |
Serial communications connector | AGP (8-way female) |
AGP (8-way female) |
Subconn (8-way female) |
|
Remote transducer connector | AGP (4-way male) | AGP (4-way male) | Burton (3-way male) | |
Housing mechanical construction | Hard anodised aluminium 6082 |
Hard anodised aluminium 7075 |
Hard anodised aluminium 7075 |
|
Remote transducer mechanical construction | Stainless steel 316 | Stainless steel 316 | Stainless steel 316 | |
Dimensions (maximum) (length x diameter) | 768 x 200 mm | 768 x 200 mm | 768 x 200 mm | |
Housing diameter | 134 mm | 134 mm | 140 mm | |
Weight in air/water | Housing assembly | 14.3/5.3 kg | 14.7/5.7 kg | 15.5/6.0 kg |
Transducer | 3.2/2.7 kg | 3.2/2.7 kg | 3.3/2.8 kg | |
Cable (5 m) | 2.7/1.4 kg | 2.7/1.4 kg | 2.7/1.4 kg | |
Sensors | ||||
Temperature (±0.1°C) | Standard | Standard | Standard | |
Strain gauge pressure sensor (±0.1%) | Standard | Standard | Standard | |
High precision strain gauge (±0.01%) | Optional | Optional | Optional | |
Inclinometer (tilt sensor) Range ±90°, accuracy: ±1° (vertical orientation) |
Standard | Standard | Standard | |
Sound velocity sensor ±0.02 m/s accuracy under calibration conditions |
Standard | Standard | Standard |
Frequently asked questions
STP files
Datasheets
Using a hammer to crack a nut? Try using a USV instead
USVs are no longer new. They’ve been used in defence for some time now, for a range of tasks from surveillance to mine counter measures. USVs are being used to survey coastal and offshore waters in hydrographic surveys, for ocean science and in oil and gas
The challenge
Crewed vessels used in offshore construction projects are costly and can even hinder progress. But it doesn’t have to be that way. Other sectors that operate in the marine space are now finding new, smaller, smarter, cleaner tools. They’ve been using uncrewed surface vessels (USVs), so the big, crewed vessels can stick to the jobs they’re good at.
So why are we not using them heavily in offshore construction?
One reason may be because offshore construction was in fact an early adopter. But, at the time, there were only a handful of commercial USV operators whose vehicles were just too big for what was needed, making them unwieldy to deploy from an offshore vessel, defeating the point of the exercise.
Another may be the worry of the complexity involved in offshore construction. Creating complex structures on shore is one thing. Creating them under metres of salt water is entirely another.
Then there is the issue of communication and control over the construction process. Making sure each step is taken exactly as planned is fundamental to the overall success of a construction project.
The solution
USV technology has come a long way since their inception. They’ve been used in defence for some time now, for a range of tasks from surveillance to mine countermeasures. USVs are being used to survey coastal and offshore waters in hydrographic surveys, for ocean science and in oil and gas. They’re being used to go out and gather data, either as a platform for oceanographic instruments or by carrying acoustic communications systems to harvest data from sensors deployed at the seabed. You could think of them being like a remote-controlled Dunker.
USVs are now part of the toolbox across a number of sectors and the levels of sophistication and capability are increasing. Worries about lack of control, the complexity of operations or large clunky kit that isn’t up to the delicate tasks required in offshore construction are today unfounded.
In offshore renewables and oil and gas USVs are being used as part of site and seismic surveys, and then through field life, for inspection operations. They’re also being used for maintenance and repair, by acting as deployment platforms for autonomous underwater vehicles (AUVs), remotely operated vehicles (ROVs) and even aerial drones (UAVs).
The results
Today there’s a wide choice of USVs to choose from. From one-man portable USVs to full sized vessels, and on to fully electric coastal systems and hybrid long-range ocean-going vehicles that can operate for weeks on end. The range of commercial models has also grown. You can buy them outright or purchase a data service where you just order the end result – be it data or an inspection campaign.
USVs can now play a central role in construction operations. They can streamline operations and reduce risk for manned offshore construction teams. When deployed they reduce reliance on heavier, costlier tools and free-up crewed assets to be used on elements of a project where they’ll bring more value.
Deepwater structure installation made easy
For five decades, we’ve been working to make subsea developments safer, cleaner and more efficient than ever before. Our aim is always to mitigate risk for our partners, reduce the complexity of deepwater structure installations and increase efficiencies so projects cost less and teams spend less time offshore.
The challenge
When offshore contractor China Offshore Fugro Geosolutions (COFG) approached us looking for ways to improve the installation of multiple deepwater structures, we were excited to support their operation. The project required the installation of four pipeline end terminations. Measuring up to 15 m long, 10 m high and weighing as much as 45 tonnes each, the challenge was to accurately place each structure efficiently and reduce the time needed for the project to be completed.
These kinds of deepwater installations are usually done by installing a gyro frame and placing a subsea gyro into it, with a battery, a modem, sound velocity sensor, and maybe also a depth sensor. These then need to be wired up, turned on, and fingers crossed that it’ll all work. The various connections, components and necessary wiring between each, create multiple opportunities for things to go wrong.
The solution
Gyro Compatt 6 is a compact and versatile positioning transponder with a subsea gyro used to simplify structure positioning. From one instrument everything can be monitored and controlled from the topside using our Ranger 2 6G Ultra-Short BaseLine (USBL) positioning system or Fusion 1 or 2 Long BaseLine (LBL) software. What’s more, it’s quick to recharge on deck, making it a perfect choice for multi-structure installation campaigns.
Onboard the HSYS 201, COFG already use our Ranger 2 USBL positioning system, our Fusion LBL software and a ROVNav 6 transceiver onboard their ROV, all of which work seamlessly with our 6G USBL family of products, of which the Gyro Compatt 6 is a part.
This compact unit is much more than a positioning transponder. The unit combines an LBL transponder Wideband acoustic positioning, Lodestar attitude and heading reference sensor (AHRS), a depth sensor and sound velocity, plus an integrated high-speed acoustic modem. By combining these technologies into one small unit, a single yet highly versatile and easy to install instrument can provide high update rate wireless attitude, heading, heave, surge, sway, pressure, sound speed and acoustic positioning of any subsea object.
There is no need for the traditional gyro frame and subsea gyro technique and all the wiring and crossing of fingers that goes along with it. By deploying the Gyro Compatt 6, ranges from the LBL array can be gathered in real time by a ROVNav 6 LBL ROV transceiver onboard the ROV, and, in turn, tracked in the LBL array.
The results
With just the Gyro Compatt 6 installed and secured for structure monitoring, COFG’s installations were successfully carried out on the Liuhua 29-1 gas field development in water depths ranging from 520 m to 1120 m, between mid-October and the end of November 2019. Each of the four installations was made much easier – with reduced stress, fewer complications and in less time.
Jia Wu, Operation Manager, Engineering Survey Division at China Offshore Fugro Geosolutions (Shenzen) Co. was pleased with how their Gyro Compatt 6 performed.
“This all-in-one system offers us the biggest advantage for the operation, being easier to use, smaller in size and more efficient for preparation,” he says. “It is more convenient to secure as well as recover and does not require wiring between components, compared with a conventional gyro basket (transponder plus battery plus gyro).”
Do you need to simplify a deep water structure installation project? Speak with an expert today.
Repeatable, configurable, long-term surveillance
The Autonomous Monitoring Transponder (AMT) is a long-endurance transponder engineered for your long term subsea survey tasks and is capable of autonomously acquiring acoustic ranges and sensor data without surface control.
AMTs can detect subtle movement often not picked up by traditional ROV surveys so it’s ideal for monitoring slow movements, like creeping or buckling pipelines. Using structure and seafloor transponder buckets, they can be ROV-deployed, removed and re-installed to provide insight over time. Your AMTs can be configured to take measurements at specific intervals and be adjusted on-demand by you as your campaign progresses. Data can even be collected in real time using a USV should your operation need it.
As it’s collected, data is time-stamped and logged internally for recovery via the integrated high-speed acoustic telemetry modem. This autonomy allows measurements to be made over a long period of time without requiring a surface vessel or ROV to command the process. This enables new applications that save vessel and survey time so reducing cost and risk.
At a glance
- Recommended for long endurance site surveys
- Leave it deployed for six years or more
- Extensive choice of monitoring sensors
- Depth rated to 3,000 m
- Harvest data using a ship, buoy, AUV or USV
AMT has many of the same acoustic functions as Compatt 6, our most popular navigation transponder. It operates in the Medium Frequency (MF) band and is fully Sonardyne Wideband 2 compatible.
Precision pressure, temperature, sound velocity and dual-axis inclinometer sensors are integrated and are intelligently powered up at the requested time and sampling period, providing an ultra-low power platform for up to three years deployment. Sampling regimes can be re-programmed, and recovery of all data can be achieved via the acoustic modem.
The instrument is available with a range of omni and directional transducers, depth ratings and pressure housings dependent on deployment duration and application. Additional external sensors can be easily integrated via the power and communications port.
Acoustics
• Sonardyne Wideband 2 MF band (18 – 36 kHz)
• Over 500 unique addresses, ideal for large array deployments
• Data transfer rates of 100 to 9,000 bps – user selectable
• Omni-directional and directional transducers to suit environmental conditions
• Ranging precision: Better than 15mm
Sensing
• Standard onboard: Temperature, tilt, strain gauge
• Optional onboard: high precision stain gauge, DigiQuartz pressure sensor, high accuracy inclinometer, sound velocity
• Sampling rate: user configurable
• Vessel, USV or AUV data harvesting options
• Optional external: current meters, turbidity sensors
Design
• 3,000 m depth rating
• Aluminium or aluminium-bronze housing depending on environmental conditions and duration of deployment
• Can be deployed for over 5 years without recovery (maxi housing)
• ROV-friendly design: integrated acoustic release mechanism as standard
Ownership
• Warranty: 1 year return to Sonardyne service centre
• ITAR Controlled: No
• UK Export Licence: Not required
• A typical system: multiple seafloor and structure mounted AMTs (typically 6), vessel-based Modem 6 or Dunker 6 or HPT 5000 / 7000, SIU, Monitor software
Specifications
Feature | Type 8305-3411 | Type 8305-3111 | Type 8305-3113 | |
---|---|---|---|---|
Depth rating | 3,000 m | 3,000 m | 3,000 m | |
Operating frequency | MF (20–34 kHz) | MF (20–34 kHz) | MF (20–34 kHz) | |
Transducer beam shape | Omni-directional | Omni-directional | Directional | |
Transmit source level (dB re 1 µPa @ 1 m) | 187–196 dB (4 levels) |
187–196 dB (4 levels) |
190–202 dB (4 levels) |
|
Tone Equivalent Energy (TEE) | 193–202 dB | 193–202 dB | 196–208 dB | |
Receive sensitivity (dB re 1 µPa) | 90–120 dB (7 levels) |
90–120 dB (7 levels) |
80–120 dB (7 levels) |
|
Ranging precision | Better than 15 mm | Better than 15 mm | Better than 15 mm | |
Number of unique addresses Wideband 1 & 2 | >500 | >500 | >500 | |
Battery life (listening, disabled) | Alkaline | 833 days | 833 days | 833 days |
Safe working load (4:1) | n/a | 250 kg | 250 kg | |
Mechanical construction | Aluminium-bronze | Aluminium | Aluminium | |
Dimensions (length x diameter) | 1007 x 130 mm | 1034 x 134 mm | 1018 x 134 mm | |
Weight in air/water | 35/24 kg | 24/12 kg | 24/12 kg | |
Endcap sensors and options | ||||
Temperature (±0.1°C) | Standard | Standard | Standard | |
Tilt switch (±30-45°) | Standard | Standard | Standard | |
Strain gauge pressure sensor (±0.1%) | Standard | Standard | Standard | |
High precision strain gauge (±0.01%) Presens or Keller | Optional | Optional | Optional | |
Paroscientific digiQuartz pressure sensor 1350 m, 2000 m, 4130 m, 6800 m (±0.01%) |
Optional | Optional | Optional | |
High accuracy inclinometer range: ±90°, Accuracy: ±0.05° over 0 – ±15°; ±0.2° over 0 – ±45° | Optional | Optional | Optional | |
Sound velocity sensor ±0.02 m/s accuracy under calibration conditions | Optional | Optional | Optional | |
Release mechanism | n/a | Standard | Standard |
Frequently asked questions
Software and firmware
Software and control hardware
Datasheets
Manuals and quick start guides
Overview
Compatt 6+ is used for high precision survey and construction operations in all water depths, including: spool piece metrology, pipeline touchdown monitoring, structure installation and dynamic positioning reference.
Compatt 6+ offers significant time saving with fast update rates (up to 1 Hz LBL tracking), all made possible using the Wideband 3 acoustic telemetry protocols. Support of Wideband 2 ranges maintains backwards compatibility. This makes any system operating with Compatt 6+ significantly easier to operate therefore de-risking operations, reducing vessel time and reducing training requirements for offshore personnel.
At a glance
- Compatible with all 6G LBL, INS and USBL systems
- Wideband 3 enabled
- Versatile, flexible and cost-effective
- Over 3,600 different configurations available
- Choice of depth ratings to 7,000 m
Our Wideband advanced signal processing offers improved acoustic performance in challenging conditions, longer ranges, improved multipath rejection around structures and real-time range diagnostics for quality control. Wideband also reduces the interference to and from adjacent Sonardyne and other acoustic positioning systems.
The integrated communications and navigation technology allows the transponder to be used as a multi-purpose modem, autonomous data logger and navigation reference transponder.
Wideband 3
For the first time, sensor telemetry data (e.g. pressure, depth or temperature) is embedded within ranging data so no more waiting for sensor readings at vital moments.
Compatible
Compatt 6+ transponders are backwards compatible with your existing Compatt 6 inventories so you can mix and match in the field.
Upgradable
We can upgrade your existing Compatt 6 into plus units quickly and cost effectively meaning you can go on to realise the full benefits of Fusion 2.
Overview
Compatt 6+ is used for high precision survey and construction operations in all water depths, including: spool piece metrology, pipeline touchdown monitoring, structure installation and dynamic positioning reference.
Specifications table
Feature | Type 8300-3111 | Type 8300-3113 | Type 8300-5213 | |
---|---|---|---|---|
Depth rating | 3,000 m | 3,000 m | 5,000 m | |
Operating frequency | MF (20–34 kHz) | MF (20–34 kHz) | MF (20–34 kHz) | |
Transducer beam shape | Omni-directional | Directional | Directional | |
Transmit Source level (dB re 1 µPa @ 1 m) | 187–196 dB (4 levels) |
190–202 dB (4 levels) |
190–202 dB (4 levels) |
|
Tone Equivalent Energy (TEE) | 193–202 dB | 196–208 dB | 196–208 dB | |
Receive sensitivity (dB re 1 µPa) | 90–120 dB (7 levels) |
80–120 dB (7 levels) |
80–120 dB (7 levels) |
|
Ranging precision | Better than 15 mm | Better than 15 mm | Better than 15 mm | |
Number of unique Wideband 2 addresses | >300 | >300 | >300 | |
Battery life (listening) | Alkaline | 833 days | 833 days | 833 days |
Lithium | 1,390 days | 1,390 days | 1,390 days | |
External power supply | 24 V | 24 V | 24 V | |
Safe working load (4:1) | 250 kg | 250 kg | 250 kg | |
Operating temperature | -5 to 40°C | -5 to 40°C | -5 to 40°C | |
Storage temperature | -20 to 55°C | -20 to 55°C | -20 to 55°C | |
Dimensions (maximum) (length x diameter) |
With sensor guard | 1,034 x 200 mm | 1,018 x 200 mm | 1,018 x 200 mm |
Without sensor guard | 1,034 x 178 mm | n/a | n/a | |
Weight in air/water | 23.8/11.8 kg | 27.0/14.0 kg | 29.0/15.0 kg | |
Endcap sensors and options | ||||
Temperature (±0.1°C) | Standard | Standard | Standard | |
Tilt switch (±30–45°) | Standard | Standard | Standard | |
Strain gauge pressure sensor (±0.1%) | Standard | Standard | Standard | |
High precision strain gauge (±0.01%) Presens or Keller |
Optional | Optional | Optional | |
Paroscientific digiQuartz pressure sensor 1,350 m, 2,000 m, 4,130 m, 6,800 m (±0.01%) |
Optional | Optional | Optional | |
Inclinometer (tilt sensor) range ±90°, accuracy: ±1° |
Standard | Standard | Standard | |
High accuracy inclinometer
range: ±90°, accuracy: ±0.05° over 0 – ±15°; ±0.2° over 0 – ±45° |
Optional | Optional | Optional | |
Sound velocity sensor ±0.02 m/s accuracy under calibration conditions | Optional | Optional | Optional | |
Release mechanism | Standard | Standard | Standard | |
Power for external sensors | Standard | Standard | Standard | |
Gyro input | Standard | Standard | Standard |
Frequently asked questions
Compatt 6 and 6+ Deployment Tests
Frequency management is obsolete. Here’s why.
6G Terminal Lite Range Test
When to use a float, when to use a stand?
How can I get the best performance from my long layback tracking operations?
How can I deploy my Compatt 6+ using iWand?
How to correctly set a Compatt 6+ release mechanism
Does Compatt 6+ have modem capabilities?
How often do endcap sensors need calibrating to keep them in spec?
Is it possible to position Compatt 6+s independently within the same array and send each positioning out of Fusion to our navigation software?
Will Compatt 6+ work with Ranger 2 and Marksman?
I want to buy standard red Compatt 6, are they still available for sale?
Can Compatt 6+ be used in the same LBL array as standard Compatt 6?
What is the difference between Compatt 6 and Compatt 6+?
If I’m using Fusion 2, can I choose to use Wideband 2 or Wideband 3 telemetry?
Can ROVNav 6+ be used with standard Compatt 6s?
Will my ROVNav 6 work with Compatt 6+?
Do I need to upgrade to Compatt 6+ and ROVNav 6+?
How to QC a Sound Velocity (SV) in Fusion 2
How far can my Compatt 6+ be above the seabed?
How to replace a battery in Compatt 6 and 6+ family of transponders
How to plan my sparse LBL array (guidance note)
How do I calibrate my sparse LBL array?
How do I set up structure deflection monitoring (SDM) in Fusion 2?
Can I use Compatt 6+ Multiuser in Fusion 2?
How do I perform a SLAM calibration in Fusion 2?
How do I set up sound speed collection and pressure to depth conversion in Fusion 2?
Software and firmware
Software and control hardware
Transponders
Manuals and quick start guides
Did you know?
Compatt 6+ uses Wideband 3 technology