Capture every feature and every detail in ultra-high resolution.
Key benefits
- Mission ready; designed to support search, classify and map (SCM) and hydrographic operations
- Small and compact arrays; optimised for low-logistic AUVs and towed bodies
- Survey more ground in a single pass; 200 m-wide swath ensures high coverage rates
- Along track resolution of 0.15°; best in class delivering maximum detection rates
- Collocated side scan image and bathy improves your situational awareness
- Consumes only 18 W power: budget friendly and increases your AUV’s endurance
- Depth rated to 300 or 600 m
Solstice offers enhanced underwater detection capabilities for various missions, including mine countermeasures, archaeological, search, and salvage operations. The system provides high-performance coverage with large 200m swaths on each side, enabling efficient site characterisation without sacrificing detail. Its class-leading imagery allows you to make confident classification decisions more quickly, with the added versatility of deployment on both autonomous underwater vehicles (AUVs) and towfish platforms. By improving probability of detection and decreasing false alarms, Solstice significantly increases the overall efficiency and reliability of underwater exploration and survey missions. It is suitable for:
- Autonomous underwater vehicles (AUV)
- Site survey and characterisation
- Mine countermeasures (MCM)
- Remotely operated vehicles (ROV)
- Delivering pixel perfect imaging
Exceptional high-contrast seafloor imagery across diverse water depths
How it works
Solstice, designed by Wavefront Systems and commercialised by Sonardyne, is a world-leading side scan sonar for autonomous underwater vehicles (AUVs) and towed bodies. Its advanced technology delivers exceptional seafloor imagery through multiple aperture arrays with 32 multibeam elements, enabling superior signal-to-noise ratio performance and stunning imagery at extended ranges. The sonar’s unique back-projection beam-forming technique ensures focused imaging for every pixel, eliminating distortions caused by platform motion and guaranteeing 100% ground coverage across diverse water depths.
Designed for a wide range of marine missions including hydrographic, archaeological, search, salvage, and mine countermeasure operations, Solstice stands out through its innovative features. Its real-time array calibration dynamically recalibrates hydrophone elements multiple times per second, compensating for dynamic strains and maintaining linear element alignment. The system produces high-contrast imagery in environments ranging from 600-metre depths to very shallow littoral waters, utilising a specialised array technology that provides wide swath coverage with exceptional shadow contrast.
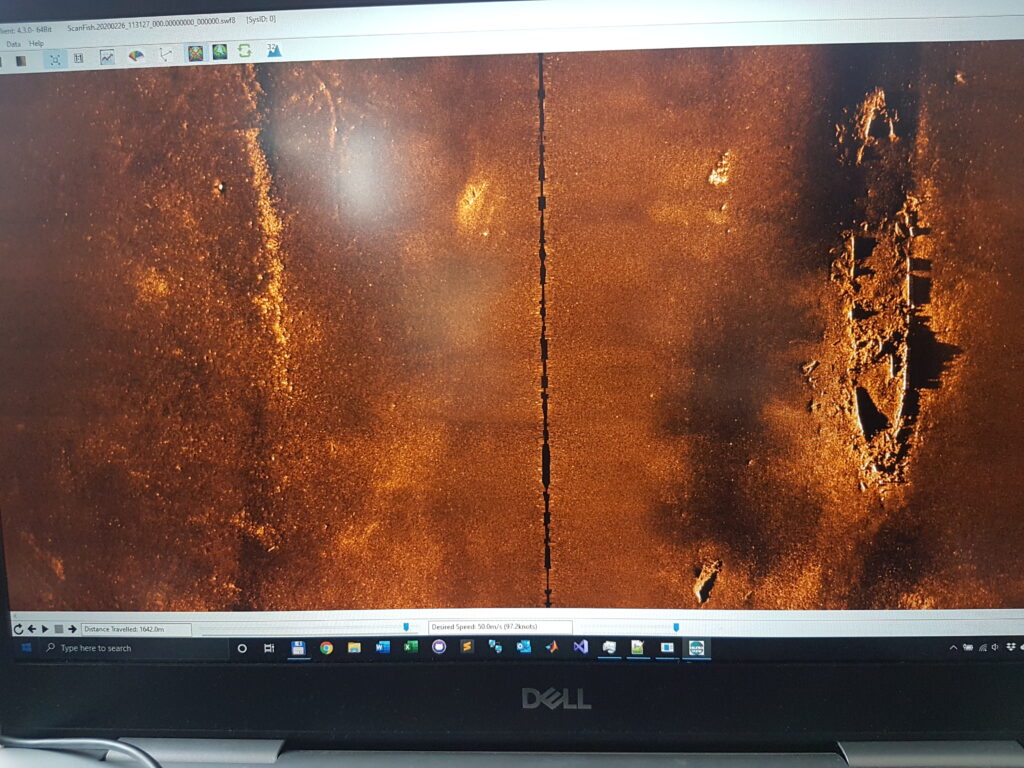
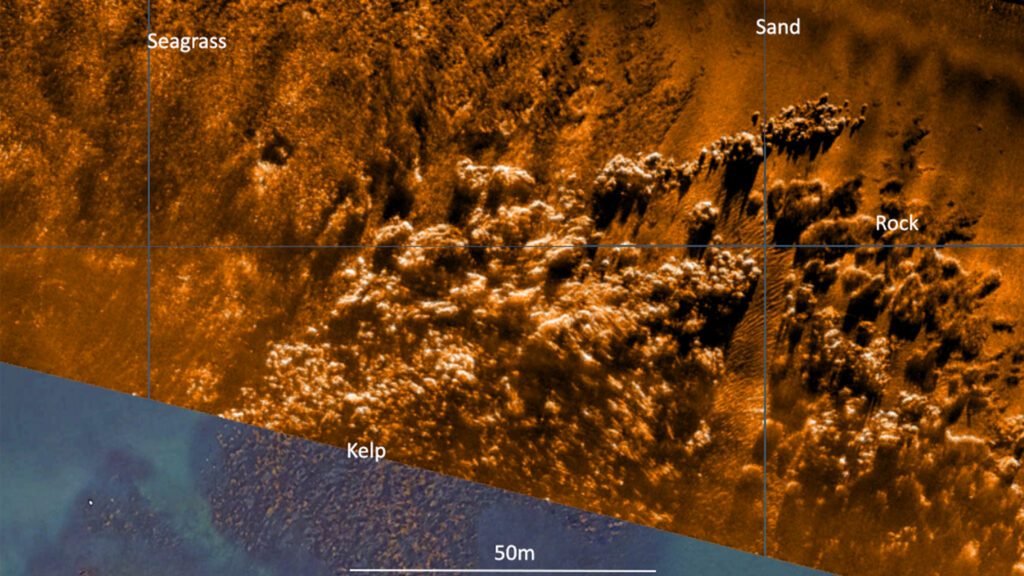
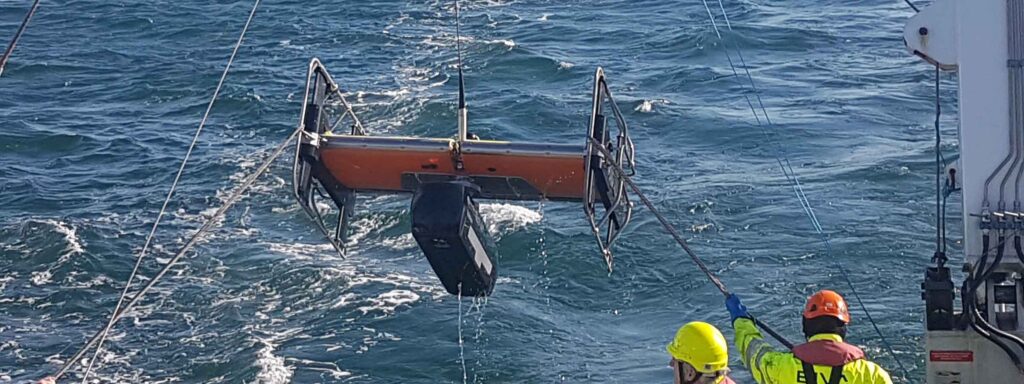
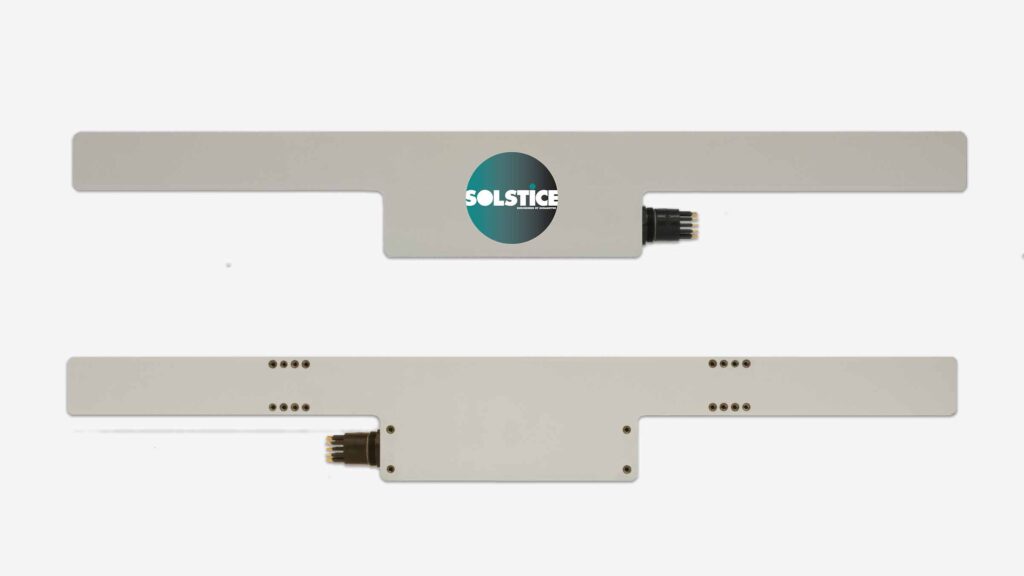
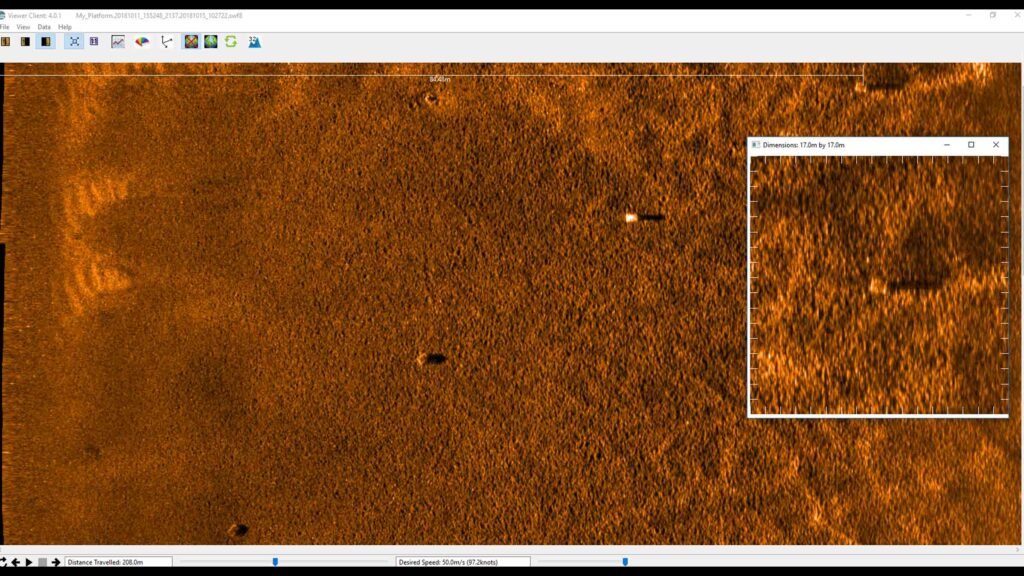
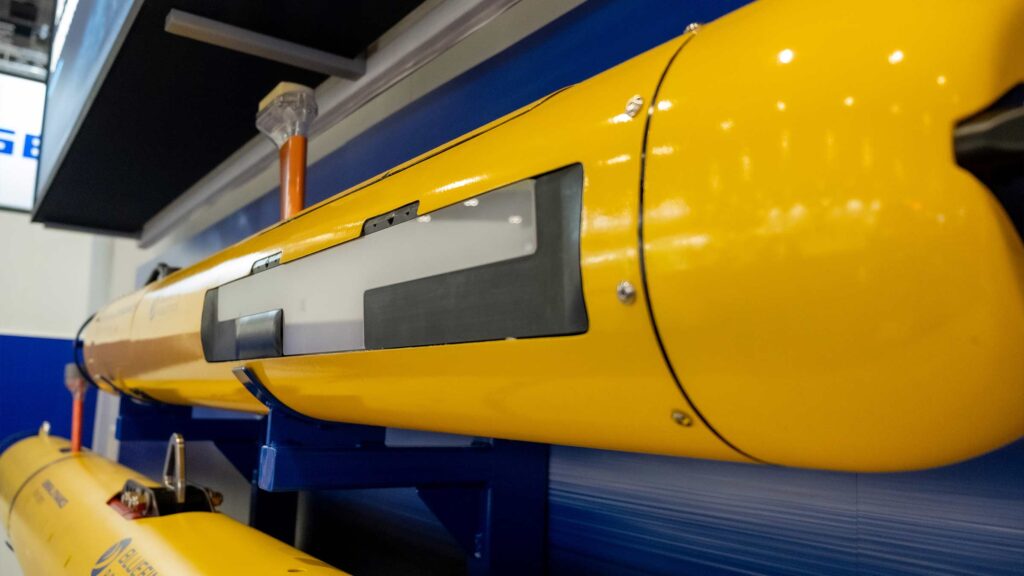
Solstice case studies
Using a hammer to crack a nut? Try using a USV instead
USVs are no longer new. They’ve been used in defence for some time now, for a range of tasks from surveillance to mine counter measures. USVs are being used to survey coastal and offshore waters in hydrographic surveys, for ocean science and in oil and gas
The challenge
Crewed vessels used in offshore construction projects are costly and can even hinder progress. But it doesn’t have to be that way. Other sectors that operate in the marine space are now finding new, smaller, smarter, cleaner tools. They’ve been using uncrewed surface vessels (USVs), so the big, crewed vessels can stick to the jobs they’re good at.
So why are we not using them heavily in offshore construction?
One reason may be because offshore construction was in fact an early adopter. But, at the time, there were only a handful of commercial USV operators whose vehicles were just too big for what was needed, making them unwieldy to deploy from an offshore vessel, defeating the point of the exercise.
Another may be the worry of the complexity involved in offshore construction. Creating complex structures on shore is one thing. Creating them under metres of salt water is entirely another.
Then there is the issue of communication and control over the construction process. Making sure each step is taken exactly as planned is fundamental to the overall success of a construction project.
The solution
USV technology has come a long way since their inception. They’ve been used in defence for some time now, for a range of tasks from surveillance to mine countermeasures. USVs are being used to survey coastal and offshore waters in hydrographic surveys, for ocean science and in oil and gas. They’re being used to go out and gather data, either as a platform for oceanographic instruments or by carrying acoustic communications systems to harvest data from sensors deployed at the seabed. You could think of them being like a remote-controlled Dunker.
USVs are now part of the toolbox across a number of sectors and the levels of sophistication and capability are increasing. Worries about lack of control, the complexity of operations or large clunky kit that isn’t up to the delicate tasks required in offshore construction are today unfounded.
In offshore renewables and oil and gas USVs are being used as part of site and seismic surveys, and then through field life, for inspection operations. They’re also being used for maintenance and repair, by acting as deployment platforms for autonomous underwater vehicles (AUVs), remotely operated vehicles (ROVs) and even aerial drones (UAVs).
The results
Today there’s a wide choice of USVs to choose from. From one-man portable USVs to full sized vessels, and on to fully electric coastal systems and hybrid long-range ocean-going vehicles that can operate for weeks on end. The range of commercial models has also grown. You can buy them outright or purchase a data service where you just order the end result – be it data or an inspection campaign.
USVs can now play a central role in construction operations. They can streamline operations and reduce risk for manned offshore construction teams. When deployed they reduce reliance on heavier, costlier tools and free-up crewed assets to be used on elements of a project where they’ll bring more value.
How to optimise carbon storage monitoring with marine robotics
For a long time, while carbon capture and storage (CCS) in offshore underground reservoirs had been widely regarded as a major way to reduce carbon emissions, it failed to attract the up-front investment needed to make it work. That’s now changing.
The challenge
In today’s far more climate conscious world, sentiment and interest in CCS has very much changed. Significant projects are now being planned. Projects are moving forward in Norway, Netherlands and the UK. Carbon storage licenses are being awarded and wells are being drilled specifically for carbon capture and storage.
Since 1996, CCS projects have been relatively small, yet their potential is vast. On the UK Continental Shelf alone there’s at least 78 gigatonnes of CO2 potential storage capacity – some 200 times the UK’s 2016 emissions*.
From capture to transport by pipeline and injection into a suitable geological formation offshore, there’s a lot to process. But the challenges do not end there. What happens to the CO2 once injected? How will we know if it finds a leak path to the surface?
To answer these challenges and achieve the visions that operators from Equinor in Norway to BP in the UK are promoting, increased capability for marine robotics is required.
The solution
Thanks to the Energy Technologies Institute (ETI) funded three-year research programme back in 2014, this challenge for increased capability of marine robotics has been attained. The project was delivered by a consortium of experienced companies including Fugro, National Oceanography Centre (NOC), British Geological Survey (BGS), Plymouth Marine Laboratory (PML) and ourselves, Sonardyne.
Along with increasing the capability of marine robotics for successful CO2 storage, four key technology elements for large carbon storage and monitoring projects were identified.
The first is a low-power and hence long-endurance autonomous underwater vehicle (AUV). This is required for cost-effective wide-area coverage surveys during baseline and repeat environmental surveys. We found using a combination of our Solstice side scan sonar and chemical sensing worked extremely well.
Second and third elements are seabed landers capable of detecting and monitoring any leakage at high-risk locations. These consist of two different landers, one using an active sonar and the second combining passive sonar and chemical sensing.
The active sonar lander, based on our Sentry integrity monitoring system (IMS), gives sensitive and reliable automated leak detection capability across a wide area. For instance, around an injection well, Sentry can monitor an area of over 2.3 million square metres, to help visualise that’s equivalent to around 325 football pitches. The passive sonar and chemical lander, uses the smarts from our underwater acoustics capabilities. It’s capable of both detection of leaks, but offers improved verification and has the potential to estimate leak rates at shorter ranges.
The fourth and final element is a surface gateway to enable communication between a shore-based monitoring office and the underwater systems. Such a gateway can be deployed from a fixed platform, from a moored buoy or from an uncrewed surface vessel (USV), many variants of which are now readily available in the market for over-the-horizon data harvesting missions.
We have a range of payloads suited specifically for use on operator’s USVs for their requirements. We also offer our own end-to-end data-harvesting service, when you just want the data without the worry about the interfaces involved in getting it.
Our system of systems approach to CCS was tested on the ETI project. Wideband acoustic communications between the underwater landers and a buoy on the surface was used to forward all data via satellite communications to a server. This type of set-up is well-proven and used globally on tsunami monitoring systems. Display and interpretation of the monitoring data can be simply integrated into a third-party system to allow non-expert users access via a web portal. From here they can see data visualizations and run reports.
The leak target was deployed in the North Sea, east of Bridlington. The NOC’s Autosub Long Range (ALR) was deployed from the small port at Bridlington and towed a short distance off the coast. After the ALR performed a series of tests to demonstrate safe navigation, the leak – a small CO2 leak – was turned ‘on’ with a flow rate of between 16 and 20 litres per minute of gas at depth, depending on the state of the tide.
With the leak “on”, ALR performed a series of different wide-area and fine-area search patterns over five days to seek out the leak. The sensor hub on the vehicle processed in real-time a complex set of Solstice sonar, physical and chemical sensor data, into useful information.
Automatic target recognition algorithms were used to identify any leaks or regions of interest. The system then scored these regions of interest and saved a small “snippet” of the sonar image data. At regular intervals throughout the survey, ALR would surface and send back data via satellite, including navigation data, chemical and physical sensor data and details of snippets of sonar data from detected leaks – an example of which can be seen below.
All of the uploaded data was simultaneously transferred to an internet server which allowed for presentation and interpretation using Fugro’s Metis software. This is an intuitive data delivery platform that allows metocean, vehicle navigation, chemical and sonar snippet data to be combined and displayed. This allowed data sharing across a wide team and supported operational decision making.
During the five days of testing, the ALR travelled a total of 270 km and could have surveyed 54 sq km of seabed in normal operation. However, for the purposes of the demonstration, a total of 16.1 sq km was actually surveyed. Throughout its mission, the ALR was remotely controlled from the shore, mostly from the NOC’s control room in Southampton.
The results
The ETI project consortium demonstrated a functional “system of systems” which can provide operators of offshore CO2 storage sites with a high level of confidence in their safe operation and assist in the provision of regulatory compliance.
We’ve proven it is possible to conduct shore-to-field-to-shore environmental survey operations using a long-endurance AUV. We’ve also shown it’s more than possible to operate well in excess of normal AUV deployments.
This method of working makes it possible to rely on a small local deployment team for CCS projects. The small team can then be supported by remote shore-based operations and a data interpretation team. This cuts both the time and cost of CCS operations considerably.
It is also entirely possible, and has been demonstrated elsewhere, that a further reduction of human decision making can be achieved to reduce operator intervention.
The ETI project demonstrated that it is possible to build highly cost-effective and autonomous sensing systems with on-board intelligence. These systems are both simple to deploy and operate and are very cost competitive with vessel-based or vessel supported AUV survey operations.
The project members have also developed two flexible seabed lander packages capable of extended duration deployments of six months to a year. These can provide localised and still also wide-area monitoring, automated processing of data subsea and communication of that information to surface.
Looking beyond carbon capture, the potential applications of such integrated marine robotic and intelligent remote sensing technologies are many and varied across ocean science, renewables, security and naval domains.
Extending the limits of autonomous system
Sending autonomous and unmanned underwater vehicles (AUV/UUV) out on missions that will last for days or weeks, unaided by vessels or any other supporting offshore infrastructure is a major goal for the ocean science, offshore energy and defence sectors.
The challenge
Improving the endurance and navigational precision of underwater autonomous systems, while also reducing costs, could provide disruptive capability in the subsea monitoring and inspection space. All three are goals in a two-year collaborative project we are leading.
If you can do this you remove the need for a surface vessel. Risk to personnel and mission costs are reduced along with the environmental footprint generated by manned surface vessels. You are able to survey more seabed for longer and with fewer or even no people offshore.
Current constraints on AUV or UUV operations, such as limited power capacity and navigational accuracy degradation over long deployments, means that the capabilities of these systems are not quite able to meet mission requirements on their own.
The solution
We’re leading a two year, £1.4 million project, with partners the National Oceanography Centre (NOC) and L3Harris ASV, to change all that. We aim to develop new positioning technologies that will extend the limits of AUVs and UUVs.
The project – Precise Positioning for Persistent AUVs, or P3AUV for short – is supported by funding through Innovate UK’s research and development competition for robotics and artificial intelligence in extreme and challenging environments.
So, what’s involved? In short, we’re developing ways to provide greater positioning accuracy for long-endurance operations in deep water. At the same time, we’re reducing power requirements for AUVs and UUV. We’ll also be increasing the use of autonomy to make Long BaseLine (LBL) positioning transponder box-in faster and easier, with onboard data processing and calibration.
This is all being done through work in three key and complementary areas: improved lower power navigational accuracy over long distances for AUV/UUVs; autonomous transponder box-in with an unmanned vessel; and improved positioning accuracy during vehicle descent/ascent in the water column.
Central to this work is the vehicle’s acoustic and inertial navigation system (INS). This is because low power sensors have much lower navigation accuracy meaning they often have to surface to correct positioning error with a GPS fix. However, by integrating low and high-power sensors to work together, the best of both worlds – high performance and much lower power consumption – can be achieved.
As an example, the NOC’s Autosub Long Range (ALR) currently uses a low-power microelectronic mechanical system (MEMS) supported by separate Doppler velocity log (DVL) and ADCP input to calculate how far it has travelled on missions. These missions can be several months long. To increase the ALR’s positioning accuracy over longer distances, we’re using our SPRINT-Nav, alongside MEMS technology to work towards high-precision solutions that save space and power.
The project also involves improving positioning accuracy when subsea vehicles transition through the water column. This is a notoriously difficult area for AUV deployments, because it relies on the Doppler velocity log (DVL) being able to ‘lock’ on to the seafloor (bottom lock), so that vehicle XYZ velocities can be calculated, supported by pressure data.
However, DVLs are range limited, so there is often a period where the DVL is out of range. When there are thousands of metres of water between the surface and the seabed, this can introduce significant positioning uncertainty. This problem is solved by using the acoustic Doppler current profiler (ADCP) capability in our SPRINT-Nav INS instrument (looking down) and a second Syrinx DVL (looking up). We can then build up a layer by layer profile of the water column velocities that can be used as tracking layers.
The objective is to reduce positioning errors significantly during both the dive and surfacing phases of an operation. This does depend on the variability of the current regime in any given area, but we’re putting this to the test throughout the P3AUV project.
The data collected during the descent and surfacing phases can be processed to provide a full ocean depth current profile – collection of which is required for many offshore energy projects. It can also be valuable for ocean research.
At the heart of this capability is our class-leading SPRINT-Nav instrument, which combines our SPRINT INS, Syrinx DVL and a high-accuracy pressure sensor in a single housing. These instruments are tightly integrated, enabling the SPRINT-Nav to use individual beam level measurements from our Syrinx DVL. This makes it a much more robust and reliable system than a separate DVL, which calculates velocity from all the beams.
Additionally, we’re implementing systems to box-in our trusted Compatt seafloor positioning transponders with a USV to make LBL operations faster and easier.
The goal is to enable full ocean depth, 1 m accuracy wide-area seabed mapping, using the L3Harris ASV’s C-Worker USV, to precisely position them (box them in). These Compatts could then be used in combination with SPRINT-Nav to calculate a Sparse Long BaseLine (Sparse LBL) solution.
Using autonomous calibration techniques will remove the need for a manned vessel to do this, providing a dramatic cost saving over current ‘state-of-the-art’ AUV operations, as well as any other operations where an LBL positioning system is needed.
To put this into perspective, an offshore support or research vessel will typically burn some 3,000 tonnes of fuel annually and generate about 10,000 tonnes (equivalent) of greenhouse gases. The environmental footprint of an independent ASV or AUV is, by comparison, negligible.
The reduction of manned vessel operations, as well as reducing deployment/recovery of vehicles over-the-side of such vessels, will reduce risk in offshore survey operations. Furthermore, the ability to mobilise this capability at short notice, without the high cost of mobilising a ship, could generate a new service industry model.
The results
Combining all of these capabilities will bring about a step-change in AUV operations, providing a disruptive capability in the subsea monitoring and inspection space. Indeed, reducing the cost and improving the navigation precision of autonomous ocean research in remote areas could bring a disruptive capability to a wide variety of applications.
Sustained ocean observation without the need for ship support is coming under increasing focus from the research community, especially in ice-covered polar areas. Long-duration navigational capability is also a key enabler for persistent covert surveillance operations in the defence sector, as well as emerging applications, including resident seabed-based systems, deep sea mining, aquaculture and UXO surveys for renewable installations.
There are also emerging requirements to monitor decommissioned offshore infrastructure ‘in perpetuity’, all of which will generate a market for this rapid and efficient mode of seabed navigation. As the only company that produces a complete hybrid acoustic navigation solution for AUVs, we are uniquely placed to work with our partners L3Harris ASV and NOC to produce a game-changing capability through the P3AUV project.
Long ROV excursions, high elevation tracking, noisy waters – not a problem
As it stands, underwater positioning is not always easy. But some environments – like shallow waters – are more challenging than others. If you don’t have good subsea positioning accuracy, you won’t have a good baseline or repeatability for comparing new survey data with old.
The challenge
Recently, our long-term customer, CCC, was engaged to carry out subsea pipeline external inspections offshore the United Arab Emirates.
It was a periodic integrity survey of an operator’s pipeline network, some of it dating back to the 1960s and 1970s. The subsea inspection campaign amounts to approximately 2,000 km of pipeline inspection distance, covering 316 pipelines over various offshore fields.
In the past, baseline data could be three metres out – and that was acceptable. Now, more than half a metre is unacceptable and repeatability is key for creating a solid baseline that can be matched for future surveys.
The main challenge for CCC was the shallow water the pipelines are situated in – as little as 5.5 m depth and not more than 30 m. Added to the shallow water complications were the length of the ROV excursions. For safety reasons, their ROV sometimes had to navigate more than 70 – 100m away from the vessel and its transceivers.
When conducting operations in shallow water you inevitably put a lot of man-made noise from engines and the ROV into the water. Surface reflections and high signal to noise, also add to the potential reduction in accuracy of subsea positioning when using a USBL system.
Long ROV excursions can be inclined to become unreliable or erratic simply because of the distance between transponder and transceivers. When combined with shallow waters, further difficulties arise. The distance between the seabed, the transceiver head, the top of the beacon and the angle of the distant vessel’s acoustic transceiver complicates and interferes with the transmission of data.
The solution
The platform used to undertake the subsea external inspection was the CCC owned and operated Saab Seaeye Leopard 1706 remote operated vehicle (ROV). Fitted with three HD cameras, Valeport bathy suite, mini SVP, CP, UT, laser line generator, MCS PRC system and two Kongsberg M3 profiling sonars. The fully equipped ROV was tracked using our Mini-Ranger 2 Ultra-Short BaseLine (USBL) system from our CCC Maritime 2 multipurpose dive support vessel.
The Ranger 2 Pro USBL system is found on all of CCC’s vessels. Because of the shallowness of the water, CCC decided to use a Mini-Ranger 2, which has a beam plot that suits these needs, and Wideband Sub-Mini 6 Plus (WSM 6+) beacons, which are proven to be reliable when operated in shallow water.
But, they still needed to deal with noise in the water, which could impact their USBL effectiveness. They decided to optimise their USBL. An ROV-mounted gyro and motion sensors were added to help improve the position with pitch, roll, attitude and heading, when the USBL started to jitter. But, because they weren’t fully integrated, it didn’t really do what they needed.
Then, we introduced them to SPRINT-Nav. SPRINT-Nav is an all-in-one navigational instrument, which combines a SPRINT INS sensor, Syrinx 600 kHz Doppler Velocity Log (DVL) and a high accuracy intelligent pressure sensor in a single unit. SPRINT-Nav tightly integrates all the raw sensor data, including individual DVL beams, to provide its high performance.
One of its advantages is, with bottom lock enabled, it doesn’t matter if you lose your USBL. The integrity of the positioning solution is preserved until your next acoustic fix comes in. This had a great advantage for CCC in achieving subsea positioning repeatability and reliability.
With SPRINT-Nav 500 fitted to their Leopard, the shallow water inspections project became far simpler. CCC achieved the best of both worlds – USBL and a high-performance INS. The USBL position is fed to SPRINT-Nav from Mini-Ranger 2 and it outputs a corrected position, based on the information from its INS and the DVL.
The results
When an ROV goes on a long excursion away from their vessel now, it doesn’t matter. If the USBL tracking drops out or if it starts jittering, SPRINT-Nav still knows where it is. The survey and data acquisition team on board the vessel were amazed; straight out of the box, SPRINT-Nav kept the ROV on course.
CCC achieved survey accuracy below half a metre, thanks to the SPRINT-Nav. Excellent positioning and repeatability were obtained, a critical need for quality inspection projects. Furthermore, CCC now has full confidence in the start and end position and doesn’t even require any post-processing.
Over-the-horizon uncrewed ocean data collection
Seabed monitoring over large areas has entered the age of autonomy, thanks to a combination of our long-endurance, wireless Fetch seabed sensors and a wide choice of uncrewed surface vessels (USVs) able to wirelessly collect their data. Read how Shell is making use of both for ocean data collection.
The challenge
A/S Norske Shell is running a long-term seabed monitoring campaign over the giant Ormen Lange gas field, 120 km offshore Norway, using an array of our Fetch pressure monitoring transponders (PMTs) in 800 – 1,100 m water depth at the field.
Fetch PMTs accurately collect pressure, temperature and inclination data at the seafloor, at pre-programmed intervals. Using this data, any vertical displacement of the seabed can be calculated. The data will help Norske Shell to proactively inform its reservoir management strategy. Each incorporates a high-speed acoustic modem, allowing stored data to be extracted at any time, wirelessly through the water, on demand.
During previous seabed monitoring campaigns, Norske Shell used a vessel of opportunity to travel out to the field to harvest the data using wireless acoustic communications. However, regularly visiting the sensors to gather the information they contain comes with costs, emissions and puts employees in potential harm’s way offshore.
The solution
We provided a full seabed to shore data collection service. Using a USV, controlled remotely, over the horizon, we visited the site and collected all the Fetch PMT data, without a single person having to travel offshore or from their home office.
The USV, an XOCEAN XO-450, was “posted” via cargo ship to Norway for the project and was launched by local marine operations service provider SafePath AS. The USV, piloted by XOCEAN staff in Ireland, then carried out the full mission, covering 300 km from Kristiansund and back, over just three days.
Throughout the mission, all those involved in the project, including Sonardyne’s remote operations specialists in the UK, XOCEAN’s pilots and Shell’s geophysicists in Norway and the US, remained working from their home offices where they were able to quality check and then receive the data, live.
0
km
offshore Norway
Up to
0
m
water depth
Meets
0
%
UK gas needs
The results
One of the largest data harvesting missions using a USV, to date, achieved safely, quickly and with significantly lower emissions and costs than could otherwise be achieved. An estimated 5.4 tonnes less CO2 per day was emitted compared with a manned vessel had been used. XOCEAN offset any remaining emissions created by its vessel.
As well as minimizing risk to personnel, reducing costs and emissions, using a USV for data collection also meant the time download the data was halved, thanks to the maneuverability and low hull and electric propulsion noise of the USV.
Planning your next ocean data collection mission? Read our white paper to find out how to move to uncrewed.
Or let us handle your next ocean data collection mission with our USV Data Harvesting Service.
Read more about why Sonardyne instruments were chosen for Ormen Lange here.
Dude, where's my ocean robot?
Autonomous naval robots are operating for longer and travelling further. Enabling them to know where they are underpins every mission so we have been investing in navigation technology that improves accuracy over time and distance.
The challenge
Any submariner will tell you that navigating underwater is no easy task. That’s because links to the global navigation satellite system (GNSS) are unreliable. Instead, submariners tend to make do with other sensors. SPRINT-Nav X, is our most accurate system yet, as the UK’s national Defence and Security Accelerator (DASA) and the Defence Science and Technology Laboratory (Dstl) would discover.
It’s a different story for autonomous craft and a lot harder to navigate without a crew. That’s why almost all uncrewed operations at sea today require access to a reliable GNSS signal. Without it, vehicles are literally lost at sea.
Our peer adversaries are investing to develop tools that block our access to GNSS, ensuring they can operate, while we’re left in the dark. It’s not just deliberate signal jamming or degradation of performance – known as spoofing – that can interrupt connections with GNSS. Loss of satellite-based timing and navigation signals needed for positioning occurs where GPS or GNSS receivers may not have a clear line of sight with the sky. This frequently affects ports and harbours situated close to tall structures or even close to cliffs and inside fjords.
We figured there had to be another way to keep track of autonomous underwater vehicles (AUVs) and remotely operated vehicles (ROVs) in challenging underwater environments. So, Sonardyne entered Phase one of the Autonomy in Challenging Environments competition run by DASA on behalf of Dstl.
The solution
We started out with the SPRINT-Nav, which is already the world’s highest performing all-in-one hybrid navigator for uncrewed vehicles, to create the hybrid navigation system, SPRINT-Nav X. This is our highest-grade SPRINT-Nav in the SPRINT-Nav family to date.
We innovated to combine four instruments in a single subsea pressure house: an attitude-heading and reference system (AHRS), a depth sensor, a Doppler velocity log (DVL) and an inertial navigation system (INS). All onboard sensors were optimally integrated to provide seamless operation and unprecedented levels of performance when compared with standalone instruments.
SPRINT-Nav also integrates individual DVL beam velocities thus providing sub millimetre level relative accuracy and making SPRINT-Nav robust over structures and rugged terrain.
However, SPRINT-Nav X delivers more certainty and higher accuracy while dead-reckoning and still maintaining the same form factor and weight as the other systems in the family. This level of performance opens the door to improved capabilities while still using commercial-off-the-shelf instruments.
Would this level of performance be sufficient to replace GNSS positioning?
DASA autonomy in challenging environments
Working with a 12 m-long SEA-KIT X class unmanned surface vehicle (USV), Sonardyne tested and validated SPRINT-Nav. How could we determine if it could be used instead of GNSS? We integrated with a SEA-KIT X and tested it against local GNSS for real-time kinematic (RTK) 50 mm accuracy positioning.
The SEA-KIT is a 10,000 nautical mile-range vessel able to carry up to 2.5 tonnes of payload, deploy and recover AUVs and ROVs. This capability, and flexibility, means it is well suited to support naval missions including intelligence gathering, hydrographic surveying and as a communications gateway.
We learned that SPRINT-Nav can provide a high integrity, continuously available navigation solution for a USV, like SEA-KIT X, operating in littoral zones in water depths up to 150 m.
SEA-KIT range
0
nautical miles
SEA-KIT can carry
0
tonnes of payload
0
km
mission
0
hour
long mission
The results
In 2020, during the exercise the team ran several missions, the longest of these was a 90 km mission that lasted over 13 hours. The mission was conducted in tough conditions with a swell of 2m and approximately 20 degrees of roll in places. The altitude of the USV was anywhere between 0.5 to 70 m from the seafloor with deep and shallow gradients and difficult terrain that included mud, rock, sand and shingle.
The USV moved predictably out to sea on a long straight line and then returned to conduct a traditional lawnmower survey pattern typically used in mine countermeasures (MCM). The drift between the estimated SPRINT-Nav position and the actual GNSS RTK signal never exceeded the 0.01% error relative to distance travelled within the specification, proving that AUVs and ROVs can find their way, with SPRINT-NAv technology. No other COTS system or product matches this performance.
Remote advances; operational advantages
A joint operation between Sonardyne and Subsea 7 has helped to de-risk technology adoption on BP’s Mad Dog Phase 2 development by allowing 24-hour remote access to offshore survey systems for onshore staff, de-risking the use of new technology, reducing project overheads, and paving the way for new ways of working in the future.
The challenge
There’s more desire than ever to be smarter and more efficient, to reduce vessel days, improve safety performance and lessen environmental footprints – all without losing performance, accuracy, reliability or downtime. Sonardyne has been working with Subsea 7 on reducing hardware requirements and vessel time in survey operations, including through the adoption of sparse Long BaseLine (LBL) navigation.
The latest step-change has been through the roll-out of Sonardyne’s Fusion 2 software, alongside the adaptation of new embedded calibration routines. By combining inertial navigation (INS) and LBL into a single system, Fusion 2 took away much of the interface complexity that had been involved in sparse LBL operations (using separate INS and LBL systems), reduced hardware overheads, and enabled whole work flows to be removed, through the ability to perform real-time simultaneous location and mapping (SLAM) calibration of sparse arrays without any need for post-processing.
SLAM
Simultaneous location and mapping
Sonardyne surveyors offer
24/7
support
The solution
During construction operations, at BP’s Mad Dog Phase 2 development in the deep water Gulf of Mexico, mobilising Fusion 2 trained surveyors to the right place at the right time had posed a challenge, due to global travel and working restrictions imposed by the coronavirus pandemic. To ensure continuity of operations across multiple vessels and offshore campaigns, Sonardyne’s Zoom and Microsoft Teams-based remote training was utilised to convert Fusion 1 trained surveyors to Fusion 2, which can be done in just one day or tailored to requirements.
In a first for both companies, Sonardyne then supplied its new Remote Operations Access Module (ROAM) giving its survey experts 24-hour remote access to Subsea 7’s onboard Sonardyne systems. ROAM provides an interface between the vessel’s Fusion 2 systems and communications systems (i.e. satellite or 4G) so that a Sonardyne surveyor can securely dial in, using a secure Portal and Virtual Network Computing (VNC) connection to support operations as if he or she were on board.
In this first project using ROAM, Sonardyne Surveyors in the UK were able to update firmware and software and provide a planned 24/7 operational service during SLAM calibration operations.
The combination of remote training and virtual support de-risked the continued adoption of Fusion 2, and Sonardyne’s remote service provided the assurance to continue with Fusion 2 and sparse LBL operations, avoiding the need to revert to full LBL and the extra equipment and inefficiencies that would bring. The ROAM system was supported by Subsea 7 survey personnel based in Aberdeen and Houston who worked to ensure efficient onboard integration.
Of course, it’s a learning process, part of which is being able to replicate the experience of being on board – where it’s easier for an experienced surveyor to see immediately what equipment there is and how it can be best deployed. This brings challenges – such as bringing on new surveyors and making sure they get the experience they need. “These are challenges that need to be and will be addressed as we move to a more digitally enabled future where remote operation become more the norm,” says Moller, “or even where operations are conducted using unmanned surface vessels.
Fusion 2 is a step towards this and there are more ways that, through ROAM, Sonardyne can help offshore clients directly – remotely – on planned operations. For example, rather than having a VNC connection, lower bandwidth connections could be used via the ROAM interface to a slave system onshore and having a digital twin running onshore where you can change settings, send these configurations offshore and then monitor operations; this is all on the Fusion 2 development roadmap.”
The results
Philip Banks, Survey Operations Manager for Global Projects at Subsea 7 added, “The mitigation of the risks for new technologies is a key gate to pass through. This allowed us to develop a roadmap to demonstrate the level of development or support required for its use, including management of any change. “Mad Dog 2 installation activities will span three years with managing changes in vessels and operational plans. The adaptation and evolution of Fusion 2 into both a cost saving and now remote support and operations platform has been a key driver in classifying it as a field-proven system for the wider business.”
Long-endurance AUV development with shallow water simplicity
Developing large, deepwater and long-endurance autonomous underwater vehicles (AUVs) isn’t a challenge for the feint hearted. But with the right approach to USBL-inertial systems, it’s a task that can be made simpler, without having to dive straight in at the deep end.
The challenge
That’s the approach that Anduril Industries has taken for its large displacement unmanned underwater vehicle (LD-UUV) vehicle, the DIVE-LD. It’s a rapid development programme that has included support from the Defense Advanced Research Projects Agency (DARPA) and technology partnerships with organizations including the Center for Marine Autonomy and Robotics at Virginia Tech.
Deepwater capability, shallow-water USBL-inertial test bed
The DIVE-LD is targeting littoral and deepwater survey, inspection and intelligence, surveillance, and reconnaissance (ISR). To meet these tasks, the 1.2 m-diameter, 5.8 m-long AUV has been designed to operate in down to 6,000 m water depth, traveling at 2-8 knots and covering, in a single mission, nearly 600 km.
To hone the vehicle’s systems, Anduril wanted to be able to conduct testing in its home waters. They already have one of our Ranger 2 Gyro USBL (Ultra-Short BaseLine) systems for full ocean depth positioning on vessels of opportunity. But they wanted something for positioning in just 6 – 20 m water depth that they could quickly set up on small coastal boats or even RHIBs.
The solution
The company, which recently acquired Quincy, Massachusetts-based underwater robotics innovator Dive Technologies, chose our Micro-Ranger 2 USBL system.
It’s a perfect fit. Micro-Ranger 2 is portable; everything you need comes in one, medium-sized IP67-rated ruggedised case, complete with its own 10-hour rechargable power supply. It’s also easy to set up and use from any waterside location, with Wi-Fi and ethernet connection to your laptop. It is able to track up to 10 targets out to 995 m range, including in shallow waters, thanks to our Wideband digital signal architecture. It’s also available with an integrator kit for those wanting to both track and communicate with targets, whether that’s divers, ROVs or even large displacement AUVs!
For Anduril, it ticked all the boxes for helping develop their navigation techniques and to implement USBL aiding while testing in areas with less than 20 m total water depth.
Combining USBL-inertial systems
What’s more, the DIVE-LD already has our highest grade hybrid acoustic-inertial instrument, SPRINT-Nav X, and our AvTrak 6 combined transponder, transceiver and telemetry instrument onboard. This allowed for seamless integration with Micro-Ranger 2, thanks to them all being built on our common hardware platform, 6G. All equipment with 6G hardware talks the same language. This gives the user added flexibility of working with various transponders, or in this case topsides, to get the job done.
DIVE-LD
0
kg
weight in air
Up to
0
days
endurance
0
m
depth rating
The results
Tim Raymond, founding engineer at Dive Technologies and now Chief Engineer at Anduril, says, “Micro-Ranger 2 allows us to deploy on almost any vessel while performing shallow water AUV testing. At the same time, it’s still capable of providing quality USBL positional aiding to the AUV, despite the small form factor and challenging acoustic environment.
“This system has already allowed us to develop navigation techniques and implement USBL aiding while testing in areas with less than 20 m total water depth, giving us high confidence in the capabilities of our DIVE-LD’s onboard software and aiding systems, prior to deployment in more austere environments where USBL aiding is critical for AUV navigation.
“The ability to rapidly deploy on almost any vessel and test integration and implementation of USBL aiding systems, without the overhead of a large host vessel and deployment into deep water, allowed us to develop USBL aiding capabilities for the DIVE-LD on an extremely tight schedule and with very low cost to test and validate.”
Are you developing an AUV or UUV? Get in touch to find out how we can support your development programme, no matter how shallow or deep you want to go.
Underpinning USV navigation; ensuring survey data quality
Uncrewed surface vehicles (USVs) are now a regular sight in our coastal waters, across energy, defence and ocean science. It’s essential we ensure their navigational and situational awareness. Find out how we’re ensuring robust USV navigation, even when traditional navigation aids drop out.
The challenge
Uncrewed surface vessels (USVs) are fast becoming a standard tool in the box across the defence, energy and science sectors. Whether it’s for mine countermeasures or offshore wind farm site characterisation surveys, they’re proving to be valuable, low footprint and low logistics platforms for an increasing array or operations.
ut USVs rely on uninterrupted GPS or GNSS signal updates to inform their situational awareness, safe navigation and to reliably position any data they’re gathering. Loss of satellite-based timing signals needed for navigation and positioning can occur in ports and harbours around tall structures or close to cliffs or inside fjords, where GPS or GNSS receivers may not have a clear line of sight with the sky. It can also happen in offshore wind farms and through deliberate signal jamming or degrading of performance, known as spoofing.
Plugging the gaps in USV navigation
When this is a risk, alternative navigation sensors and instruments must be considered – otherwise USVs need to be remotely piloted, adding expense and risk to over-the-horizon operations. This was a challenge identified by the UK’s Defence Science and Technology Laboratory (Dstl).
Dstl saw a need to aid autonomous vehicle operations in challenging environments. So, via the UK’s national Defence and Security Accelerator (DASA), the Autonomy in a Challenging Environments competition set out to address factors that affect the military effectiveness of current autonomous technologies – and we were one of the companies chosen to help solve this challenge.
The solution
We worked with USV manufacturer SEA-KIT to take sensors already used for unmanned and autonomous underwater vehicle (UUV/AUV) navigation and tested them on one of their USVs. Specifically, we took our market leading SPRINT-Nav hybrid inertial navigation instrument and integrated into a SEA-KIT X class USV. We then tested it against local real-time kinematic (RTK) GPS positioning.
Acoustic-inertial navigation, in one
SPRINT-Nav is already proven as a reliable navigation instrument for autonomous and uncrewed underwater vehicles (AUV/UUVs), which operate in what is effectively a GPS or GNSS denied environment.
It was designed to create a “best of all worlds”; an all-in-one acoustic-inertial sensor that replaces the need for a separate Doppler velocity log (DVL), pressure sensor and INS/AHRS, saving cost, cabling and integration challenges. By tightly integrating these separates, SPRINT-Nav delivers class-leading performance. With the addition of SPRINT-Nav Mini, that’s also available in an even smaller and lighter package.
0
km
mission
0
hours
Over
0
m
swell
Over
0
%
roll
The results
The test environment for our SPRINT-Nav onboard the SEA-KIT X was in Plymouth Sound. This is a very busy marine environment. A USV without a reliable GPS signal is not only dead-in-the-water, it’s also a danger to others. In addition, without reliable navigation its payloads will lack the situational awareness to be effective.
To test SPRINT-Nav in this environment, we planned a series of runs over different seafloors at different heights from the seafloor. In essence we tried to stress the sensors on board to observe if the system would perform to spec.
Stress testing SPRINT-Nav as a USV navigator
We ran these runs many times, but one particular run was a great example of the system’s performance. This mission ran for more than 13 hours and covered 87 km. During the run, we had a lot of swell. Fortunately, because we integrate our SPRINT INS (complete with Honeywell ring laser gyro-based AHRS), with our Syrinx DVL in SPRINT-Nav, we were able to compensate for motions.
To give the system as difficult scenario as possible, we ran on an almost straight line as far away from port as possible. So, essentially, we are dead-reckoning for a prolonged period of time, without absolute references.
Success: <0.01% of distance travelled
The result? The peak error was below 0.01% of distance travelled when furthest from origin (30km away), rising to 0.016% over the 87km travelled. On the way back, we also ran a lawnmower pattern typical of mine countermeasure (MCM) missions or typical surveys. By integrating SPRINT-Nav onto a USV, we showed we can provide a continuous and resilient navigation solution in denied environments.
Since the trials, SPRINT-Nav and SPRINT-Nav Mini have both been selected for and integrated onto multiple additional USV platforms, including Ocean Infinity’s Armada Fleet and a hybrid surface and underwater uncrewed platform.
*The competition Autonomy in a Dynamic World competition was funded through the MOD’s Chief Scientific Adviser’s Research Programme’s Autonomy Incubator project that aims to: Identify and develop underpinning research and technologies to support the development and fielding of unmanned systems across defence which may be matured through the DSTL Autonomy Programme and other Research and Development programmes.